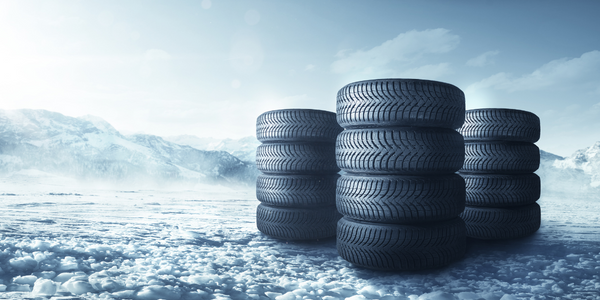
Technology Category
- Analytics & Modeling - Digital Twin / Simulation
- Platform as a Service (PaaS) - Application Development Platforms
Applicable Industries
- Automotive
- Cement
Applicable Functions
- Procurement
- Product Research & Development
Use Cases
- Manufacturing Process Simulation
- Virtual Prototyping & Product Testing
Services
- System Integration
- Testing & Certification
The Customer
Toyo Tire Corporation
About The Customer
Toyo Tire is a Japanese-based tire manufacturer that prides itself on its loyal customer base, who they refer to as their 'fans'. The company is known for its high specification features, performance, and progressive design, which gives customers confidence to drive in all weather conditions and terrains. Toyo Tire is committed to creating innovative tires to suit the specific needs of new modes of transport, such as electric vehicles and connected cars. The company's mission is to create excitement and surprise with products that exceed customer expectations and enrich society. Toyo Tire has a growing base of loyal customers worldwide.
The Challenge
Toyo Tire, a Japanese-based tire manufacturer, was facing the challenge of keeping up with the rapid changes in the automotive industry. With the advent of electric vehicles and connected cars, the company recognized the need to innovate and develop new types of tires to meet these specific needs. However, their existing product development processes were not sufficient to keep pace with the industry's transformation. The company's data was held in siloes, preventing users from easily accessing all the information they needed. This lack of integration was hindering their ability to innovate and develop new products efficiently. Toyo Tire needed a solution that would accelerate its product development processes and put innovation at the core of its activities.
The Solution
To address these challenges, Toyo Tire decided to build a new simulation process and data management (SPDM) system. The company partnered with Dassault Systèmes to develop its SPDM system, called T-MODE, based on the 3DEXPERIENCE® platform. This platform provided an integrated environment for its R&D processes, helping the company to develop innovative products more efficiently. The 3DEXPERIENCE platform allowed Toyo Tire to consolidate its data, gain a better overview of its processes, and carry out both tire design and drive simulation. This enabled the company to optimize the structure, pattern, and compound of its tires according to specific vehicle types and usages. The platform also provided a user-friendly environment where designers and engineers could conduct simulations themselves, reducing design lead times and increasing the number of viable designs brought to market.
Operational Impact
Quantitative Benefit
Case Study missing?
Start adding your own!
Register with your work email and create a new case study profile for your business.
Related Case Studies.
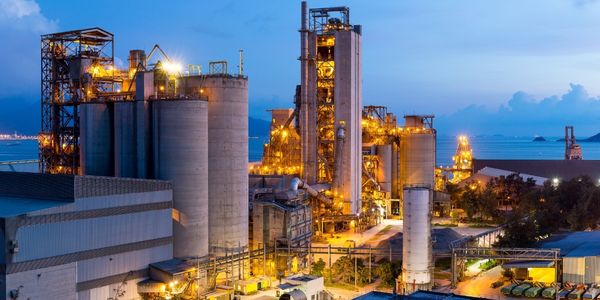
Case Study
System 800xA at Indian Cement Plants
Chettinad Cement recognized that further efficiencies could be achieved in its cement manufacturing process. It looked to investing in comprehensive operational and control technologies to manage and derive productivity and energy efficiency gains from the assets on Line 2, their second plant in India.
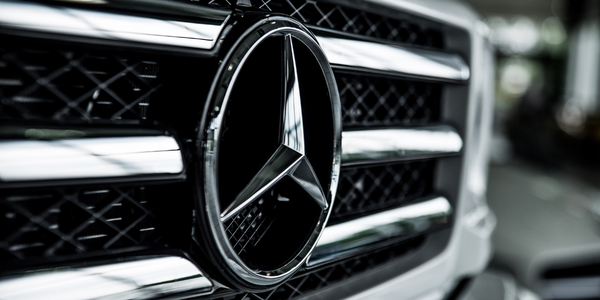
Case Study
Integral Plant Maintenance
Mercedes-Benz and his partner GAZ chose Siemens to be its maintenance partner at a new engine plant in Yaroslavl, Russia. The new plant offers a capacity to manufacture diesel engines for the Russian market, for locally produced Sprinter Classic. In addition to engines for the local market, the Yaroslavl plant will also produce spare parts. Mercedes-Benz Russia and his partner needed a service partner in order to ensure the operation of these lines in a maintenance partnership arrangement. The challenges included coordinating the entire maintenance management operation, in particular inspections, corrective and predictive maintenance activities, and the optimizing spare parts management. Siemens developed a customized maintenance solution that includes all electronic and mechanical maintenance activities (Integral Plant Maintenance).

Case Study
Monitoring of Pressure Pumps in Automotive Industry
A large German/American producer of auto parts uses high-pressure pumps to deburr machined parts as a part of its production and quality check process. They decided to monitor these pumps to make sure they work properly and that they can see any indications leading to a potential failure before it affects their process.