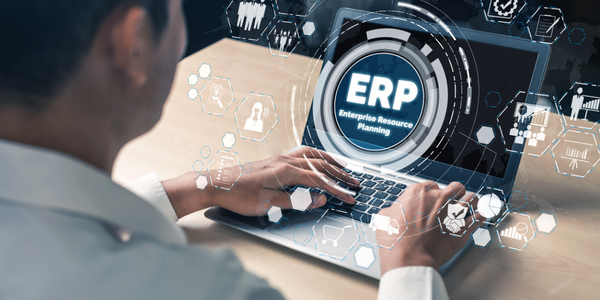
Technology Category
- Automation & Control - Automation & Process Control Systems
- Automation & Control - Distributed Control Systems
Applicable Industries
- Electronics
- Mining
Applicable Functions
- Facility Management
- Procurement
Use Cases
- In-process Traceability
- Process Control & Optimization
Services
- Cloud Planning, Design & Implementation Services
- System Integration
The Customer
Copps Industries
About The Customer
Copps Industries is a global provider of epoxy resins to civil engineering, mining, electronics, and adhesive markets. The company has been in operation since 1979, offering reactive polymers with countless applications. Despite its global reach and diverse product offerings, Copps was a small team that relied heavily on manual processes and outdated technology. The company faced challenges in scaling its operations and managing its processes, particularly after the retirement of two long-term employees. Copps needed a solution that would allow it to scale its business, ensure process control, and centralize information for easy access by all employees.
The Challenge
Since 1979, Copps Industries has been a global provider of epoxy resins to various markets. However, the company faced challenges in scaling to meet market demand due to outdated technology and manual workarounds to fill in process gaps. The company relied heavily on people to deliver scalable and repeatable processes, which limited the volume of SKUs manageable by their small team. Copps was also burdened with an outdated disk-operating system (DOS) that no longer supported its business needs, and employees struggled with managing a paper trail of documents. The retirement of two 20+ year veterans further complicated matters, leading to issues with process control and onboarding new employees. Copps Industries needed a solution that would tighten process control, scale with its business, and centralize information for easy access.
The Solution
After exploring several solutions, Copps Industries selected Deacom ERP, a comprehensive enterprise resource planning solution for global manufacturers and distributors, in 2008. Twelve years later, the company upgraded their system to Deacom’s Managed Cloud Services (MCS). Deacom’s MCS provided Copps employees with fast, secure, and reliable access to the data they needed to perform their jobs. The company began migrating to the cloud and running a full Deacom upgrade in October 2019, becoming fully operational by February 2020. This switch eliminated the need for outside IT support to maintain the server. Deacom’s Managed Cloud Services solved the issue of providing vital information to employees, making it accessible to anyone on staff without relying on others. The timing of the cloud migration also proved fortuitous, as the COVID-19 pandemic surfaced mere weeks after the migration was complete, allowing Copps to move to remote work seamlessly.
Operational Impact
Quantitative Benefit
Case Study missing?
Start adding your own!
Register with your work email and create a new case study profile for your business.
Related Case Studies.
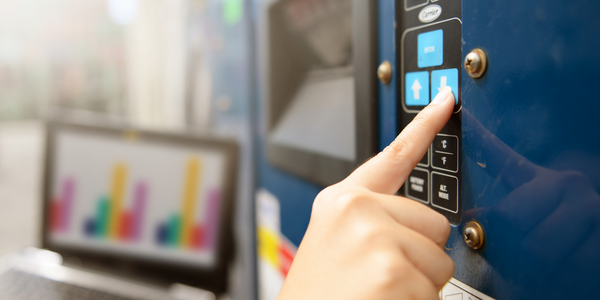
Case Study
Remote Temperature Monitoring of Perishable Goods Saves Money
RMONI was facing temperature monitoring challenges in a cold chain business. A cold chain must be established and maintained to ensure goods have been properly refrigerated during every step of the process, making temperature monitoring a critical business function. Manual registration practice can be very costly, labor intensive and prone to mistakes.
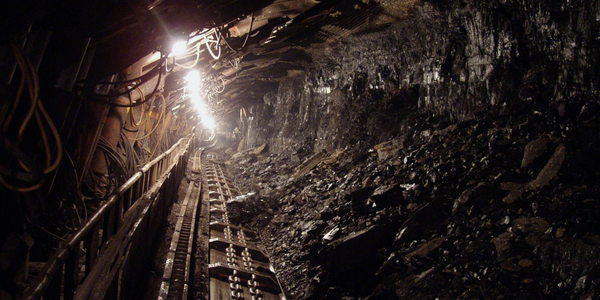
Case Study
Underground Mining Safety
The goal was to produce a safety system to monitor and support underground mining operations; existing systems were either too simple (i.e. phone line) or overly complex and expensive, inhibiting deployment, and providing little-to-no support in event of an accident. Given the dangerous nature of the mining work environment and the strict regulations placed on the industry, the solution would have to comply with Mine Safety and Health Administration (MSHA) regulations. Yet the product needed to allow for simple deployment to truly be a groundbreaking solution - increasing miner safety and changing daily operations for the better.
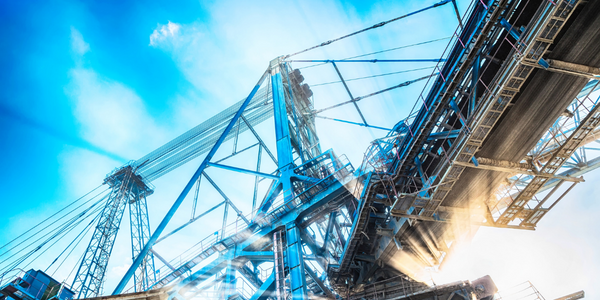
Case Study
Mining Firm Quadruples Production, with Internet of Everything
Dundee Precious Metal’s flagship mine, in Chelopech, Bulgaria, produces a gold, copper, and silver concentrate set a goal to increase production by 30%. Dundee wanted to increase production quality and output without increasing headcount and resources, improve miner safety, and minimize cost.
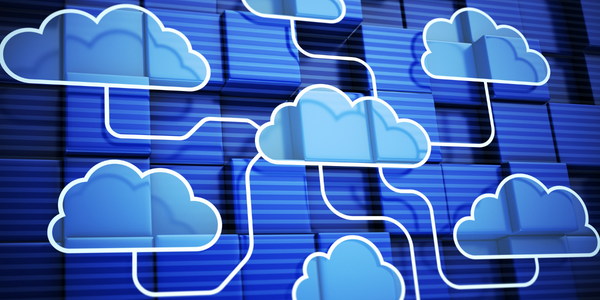
Case Study
Cloud Solution for Energy Management Platform-Schneider Electric
Schneider Electric required a cloud solution for its energy management platform to manage high computational operations, which were essential for catering to client requirements. As the business involves storage and analysis of huge amounts of data, the company also needed a convenient and scalable storage solution to facilitate operations efficiently.