Technology Category
- Infrastructure as a Service (IaaS) - Cloud Computing
- Sensors - Liquid Detection Sensors
Applicable Industries
- Life Sciences
- Mining
Applicable Functions
- Product Research & Development
- Quality Assurance
Use Cases
- Construction Management
- Experimentation Automation
Services
- Testing & Certification
About The Customer
Hatch Ltd. is a global supplier of engineering, project, and construction management services to the mining, metallurgical, energy, and infrastructure sectors. They were contracted to upgrade the conveyor transfer point at an existing coal preparation plant. The client required upgrades to accommodate a scheduled increase in production. The conveyor carried coarse product coal, topped by a layer of filter cake with a high moisture content. The existing chute was prone to material build-up of this “sticky” filter cake, often plugging during surges in flow rate and causing costly downtime.
The Challenge
Hatch Ltd., a global supplier of engineering, project, and construction management services to the mining, metallurgical, energy, and infrastructure sectors, was contracted to upgrade the conveyor transfer point at an existing coal preparation plant. The client required upgrades to accommodate a scheduled increase in production. The conveyor carried coarse product coal, topped by a layer of filter cake with a high moisture content. The existing chute was prone to material build-up of this “sticky” filter cake, often plugging during surges in flow rate and causing costly downtime. Despite being a relatively small conveyor, at 1,200 t/h, it was critical to ensuring constant product throughput to truck-loading bins.
The Solution
Hatch deployed the EDEM BulkSim Solution, including Material Testing and DEM Material Model Calibration services, to redesign the transfer chute. Dynamic flow testing was performed on actual samples of the product coal and filter cake that were representative of actual materials on-site. DEM Material Models were quickly calibrated by comparison of physical test results with simulations, using automated parameter sweeps on a cloud computing platform. Hatch’s new transfer point design included a flop gate, hinged at the top, to direct flow onto one of two flow paths. Virtual performance testing of design options was performed under a range of material flow conditions and included highly cohesive materials. This enabled Hatch to quickly select the optimal configuration for production of the detailed design.
Operational Impact
Quantitative Benefit
Case Study missing?
Start adding your own!
Register with your work email and create a new case study profile for your business.
Related Case Studies.
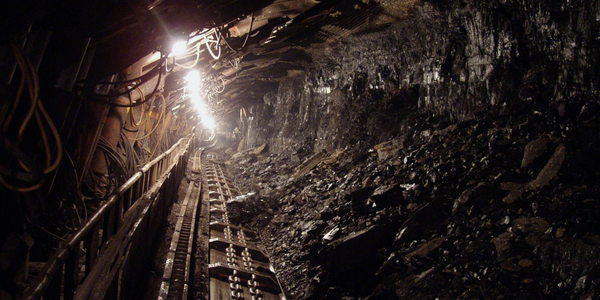
Case Study
Underground Mining Safety
The goal was to produce a safety system to monitor and support underground mining operations; existing systems were either too simple (i.e. phone line) or overly complex and expensive, inhibiting deployment, and providing little-to-no support in event of an accident. Given the dangerous nature of the mining work environment and the strict regulations placed on the industry, the solution would have to comply with Mine Safety and Health Administration (MSHA) regulations. Yet the product needed to allow for simple deployment to truly be a groundbreaking solution - increasing miner safety and changing daily operations for the better.
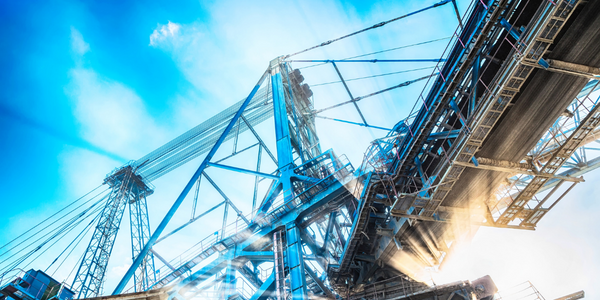
Case Study
Mining Firm Quadruples Production, with Internet of Everything
Dundee Precious Metal’s flagship mine, in Chelopech, Bulgaria, produces a gold, copper, and silver concentrate set a goal to increase production by 30%. Dundee wanted to increase production quality and output without increasing headcount and resources, improve miner safety, and minimize cost.
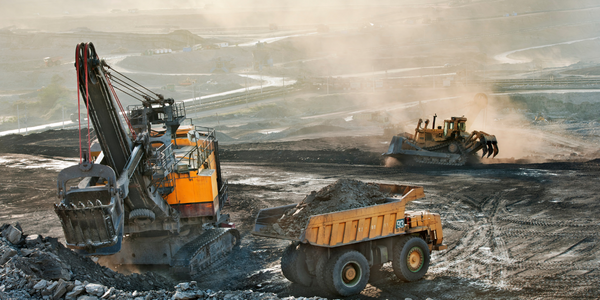
Case Study
Fastenal Builds the Future of Manufacturing with MachineMetrics
Fastenal's objective was to better understand their machine downtime, utilization, quality issues, and to embrace cutting-edge manufacturing technology/process improvement capabilities to bring their team to the next level. However, there was a lack of real-time data, visualization, and actionable insights made this transition impossible.
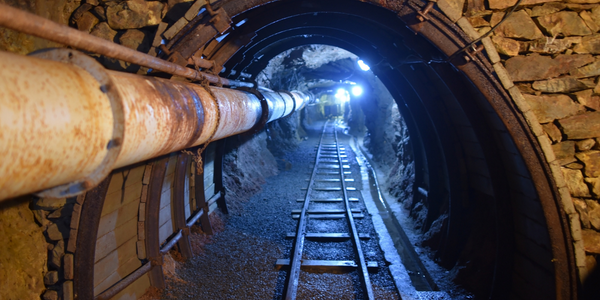
Case Study
Joy Mining Systems
Joy equipment faces many challenges. The first is machine integration and control. The business end of the machine has a rapidly-spinning cylinder with 6-inch diamond-studded cutting teeth. It chews through rock at rates measured in tens of tons per minute. The system grinds through the rock in front, creating a rectangular mine tunnel. Hydraulic lifters support the ceiling as the machine moves forward. Automated drills and screws drive 3-ft long screws into the ceiling to stabilize it. The rock and coal fall into a set of gathering "fingers" below the cutting cylinder. These fingers scoop up the rock and coal and deposit it onto a conveyor belt. The conveyor passes under the machine and out the back. A train of conveyor belt cars, up to a mile long, follows the cutter into the mine. The rock shoots along this train at over 400 feet per minute until it empties into rail cars at the end. Current systems place an operator cage next to the cutter. Choking dust (potentially explosive), the risk of collapse and the proximity of metal and rock mayhem make the operator cage a hazardous location.
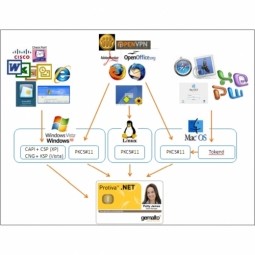
Case Study
Corporate Identity Solution Adds Convenience to Beckman Coulter
Beckman Coulter wanted to implement a single factor solution for physical and remote logical access to corporate network. Bechman Coulter's users were carrying smart card badges for doors, but also needed a one-time password token to access to our corporate network when they were not in the office. They wanted to simplify the process.
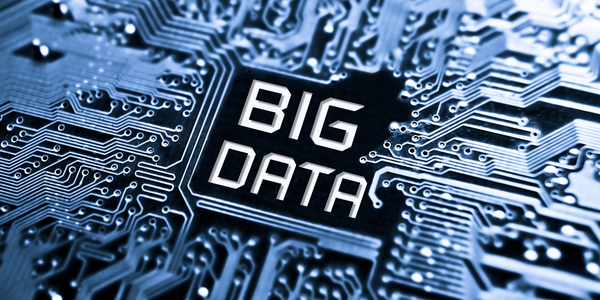
Case Study
Embracing Business Success in Real Time
· Increase control over growing Big Data to improve business decisions · Manage data for 28,000 biotechnology stockkeeping units in the fields of microbiology, molecular biology, animal cell cultures, plant tissue cultures, and lab ware for laboratory chemicals · Accelerate report generation and analysis with real-time data