Technology Category
- Sensors - Flow Meters
- Sensors - Liquid Detection Sensors
Applicable Industries
- Electrical Grids
- Packaging
Applicable Functions
- Product Research & Development
- Quality Assurance
Use Cases
- Experimentation Automation
- Intelligent Packaging
Services
- System Integration
- Testing & Certification
About The Customer
CNH Case New Holland is a global leader in the agricultural and construction equipment businesses. With facilities located on every continent, CNH has a worldwide presence and a vast network of 10,800 dealers in 160 countries. The company has been supporting the agricultural industry since the mid-1800s, providing a range of products and solutions to meet the diverse needs of its customers. The company's commitment to innovation and technology is evident in its approach to tractor design, where it leverages advanced flow modeling software to optimize the design and performance of its products.
The Challenge
Large tractors require complex cooling systems that consist of five separate modules. Each cooling module is dedicated to one of the engine’s five different fluid systems, includes its own heat exchanger, and is additionally cooled by the main engine fan. The primary goal of the tractor is to support itself and the added extra load of any attachments it has, such as a mower or a plow. This necessitates a design effort that focuses on maximizing engine power output and efficiency of the cooling package, while also optimizing the locations of all the components within the engine compartment to provide enough air to both the engine and the cooling system modules. For CNH, this design process often only included an in-depth analysis of the individual components, for example, each of the cooling modules. There was no simple way to include the effect of component layout within the engine compartment and the distribution of airflow to each module over the entire system. The alternative used by CNH, though expensive and time-consuming, was to develop and test several prototypes to balance cooling with space requirements.
The Solution
CNH used flow modeling software, ANSYS Fluent and ANSYS TGrid, to simulate the flow of air in and around engine compartment components, allowing the entire system to be examined at once, as opposed to the previous piece-by-piece approach. This analysis enabled CNH to analyze the overall cooling system and its capacity, minimize power used by the cooling system, and optimize the cooling module position. By using flow modeling tools, CNH was able to eliminate the fabrication and testing of multiple costly prototypes, define the best prototype as predicted by ANSYS Fluent software with very good agreement between experimental measurements and computer-simulated values, reduce the amount of power drawn by the cooling system compared to the initial design, and meet all cooling module thermal and packaging requirements.
Operational Impact
Quantitative Benefit
Case Study missing?
Start adding your own!
Register with your work email and create a new case study profile for your business.
Related Case Studies.

Case Study
IoT Data Analytics Case Study - Packaging Films Manufacturer
The company manufactures packaging films on made to order or configure to order basis. Every order has a different set of requirements from the product characteristics perspective and hence requires machine’s settings to be adjusted accordingly. If the film quality does not meet the required standards, the degraded quality impacts customer delivery causes customer dissatisfaction and results in lower margins. The biggest challenge was to identify the real root cause and devise a remedy for that.

Case Study
Hydro One Leads the Way In Smart Meter Development
In 2010, Ontario’s energy board mandated that time-of-use (TOU) pricing for consumers be available for all consumers on a regulated price plan. To meet this requirement, Hydro One needed to quickly deploy a smart meter and intelligent communications network solution to meet the provincial government’s requirement at a low cost. The network needed to cover Hydro One’s expansive service territory, which has a land mass twice the size of Texas, and its customers live in a mix of urban, rural, and remote areas, some places only accessible by air, rail, boat or snowmobile. Most importantly, the network needed to enable future enterprise-wide business efficiencies, modernization of distribution infrastructure and enhanced customer service. To meet these needs, Hydro One conceptualized an end-to-end solution leveraging open standards and Internet Protocols (IP) at all communication levels. The utility drew upon industry leaders like Trilliant to realize this vision.
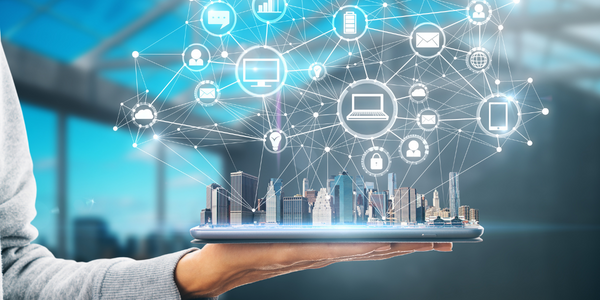
Case Study
Selling more with Whirlpool
Whirlpool wanted to add connectivity to appliances and transform the company's relationship with customers. Traditionally, Whirlpool interaction with customers was limited to purchases made once every ten years. Connected washer and dryers provide exciting new features like remote management of start times and inter-machine communication.
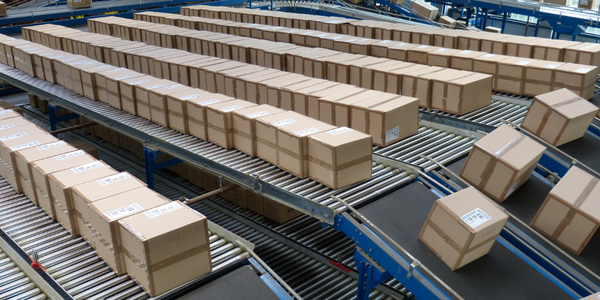
Case Study
Zenon the Ideal Basis for An Ergonomic HMI
KHS develops and produces machines and equipment for filling and packaging in the drinks industry. Because drinks manufacturing, filling and packaging consist of a number of highly complex processes, the user-friendly and intuitive operation of equipment is increasingly gaining in significance. In order to design these processes as simple as possible for the user, KHS decided to introduce a uniform, transparent and standardized solution to the company. The HMI interface should meet the requirement for people with different qualifications and enable them to work on a standard platform.
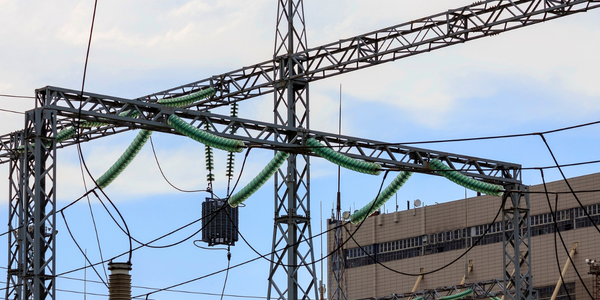
Case Study
SAS® Analytics for IoT: Smart Grid
Companies face falling revenues, rising infrastructure costs, and increasing risk of outages caused by inconsistent energy production from renewable sources. Less money is coming in as more people and organizations take steps to curb their energy use. Utilities are paying more to maintain and build infrastructure due to increasing complexity, resulting from the rising number of intermittent and variable renewable energy sources connected in the distribution grid.
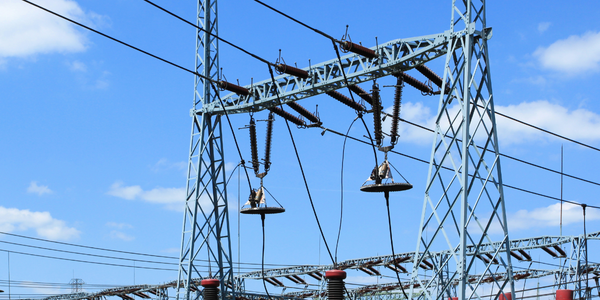
Case Study
Enel Secures Italian Power Generation Network
Electric energy operators around the world are working to increase the reliability and cyber resiliency of their systems. This includes Enel, a global power company that manages and monitors the Italian power grid. This grid:• Serves 31 million customers• Has a net installed energy capacity exceeding 31 gigawatts• Includes more than 500 power generation plants,including hydroelectric, thermoelectric, and wind• Is managed and monitored by Enel 24/7/365• Is operated by Terna, the Italian Transmission System Operator (TSO)Enel is responsible for the availability of the grid’s underlying ICS and industrial network. It also manages Regional Control Centers and Interconnection Centers which connect with the TSO. The TSO manages the flow of energy to the grid plus controls and remotely regulates the power generation of power plants, increasing and decreasing power production as required. The complex system of interaction and cooperation between Enel and the TSO has strong security implications as well as operational and business challenges.