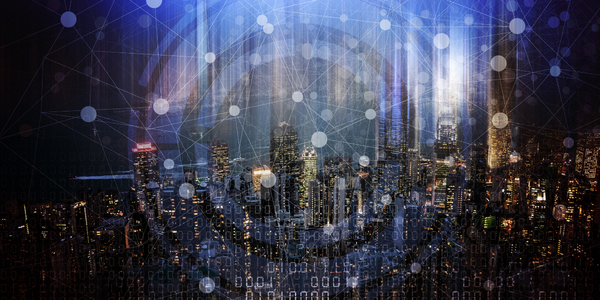
- Functional Applications - Remote Monitoring & Control Systems
- Infrastructure as a Service (IaaS) - Cloud Computing
- Infrastructure as a Service (IaaS)
- Networks & Connectivity - Routers & Bridges
- Agriculture
- Process Manufacturing
- Machine Condition Monitoring
Machine service and maintenance have been a standard in the machine manufacturing industry for years. If you manufacture a substantial amount of machines that are shipped all over the world, you’ll need a remote access solution to keep track of them and to provide high-quality service. It is not unique, however, which is why Water IQ went looking for a partner with whom they could dive into the world of cloud and automation.
Water IQ had far-reaching ambitions early on, aiming to stay ahead of the competition. “We strive to provide solutions that can increase a customer’s company value using water, for example by improving the product quality or production efficiency,” Freddy explains.
To realize these ambitions, they needed a platform where they could access machine data. “That simply requires a data logging and analysis system.”
The main reason Water IQ switched to IXON was the ability to easily log machine data. The first Water IQ machine, which was placed in Australia, was originally equipped with another VPN router. “When we put the Opticlear Diamond in operation, we immediately took the other VPN router out. I had the IXON module with me in my suitcase,” says Freddy. How they found IXON? Freddy met Willem Hofmans (CEO at IXON) during the WoTS trade fair in Utrecht, the Netherlands. He was quickly convinced that the IXON solution was the perfect fit for Water IQ. “To me, IXON is an extension of my business strategy and philosophy. It’s an important part, maybe even more important than you may think,” stated Freddy.
By using the IXON Cloud platform, Water IQ can now realize its ambitions. “[Cloud Logging] is so easy to use, IXON has developed a phenomenal graphic tool. It’s so amazing that many of its functions are still unknown to me, but you can basically do anything with it,” Freddy pointed out. Water IQ is able to perform quick analyses, even on their mobile phone while they’re on-the-go. With the use of Cloud Notify, they now receive an early signal when periodic maintenance is required.
Water IQ no longer delivers any machines without the IXON Cloud application. It’s even become an essential part of the system, and of their strategy. “You have a Water IQ machine, but what you really get is a cloud solution. You just need the machine because you can’t do anything else otherwise,” explains Freddy. It’s also becoming increasingly more common that customers request access to perform their own data analyses.
In the future, they want to go even further with their data analysis and finding trends. Water IQ wants to start giving targeted advice based on current developments. “That’s the added value for the customer,” says Freddy. “The inline sensors that we’re currently developing, will generate real-time water composition data that’s never been available before. That’s really going to mean something for the way we’re going to treat water.”
Case Study missing?
Start adding your own!
Register with your work email and create a new case study profile for your business.
Related Case Studies.
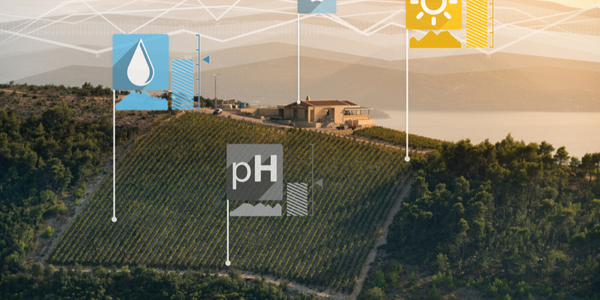
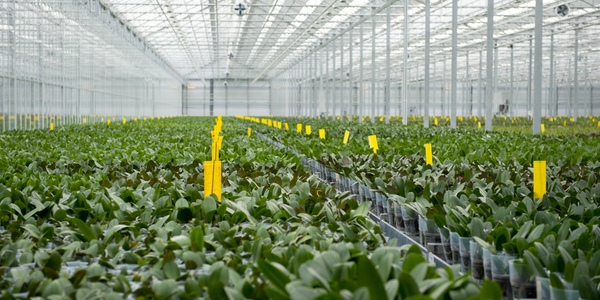
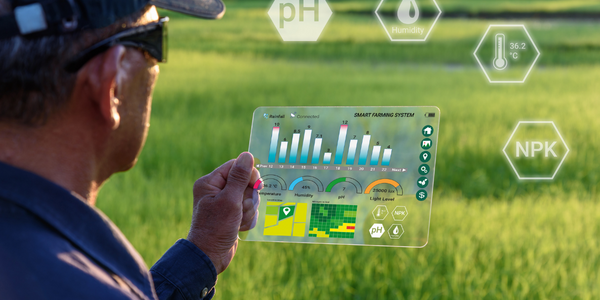
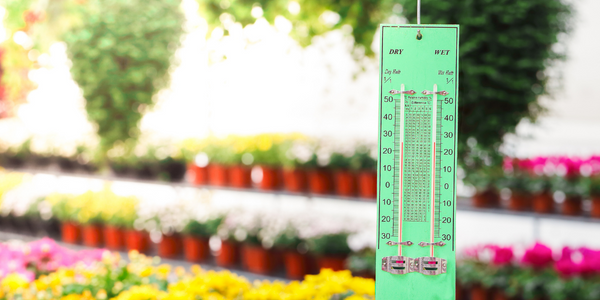