Customer Company Size
Large Corporate
Region
- Asia
Country
- China
Product
- ARIS Design & Strategy
- ARIS Rollout & Change Management
Tech Stack
- ARIS process management platform
- ARIS Business Process Analysis (BPA)
Implementation Scale
- Enterprise-wide Deployment
Impact Metrics
- Productivity Improvements
- Customer Satisfaction
Technology Category
- Application Infrastructure & Middleware - API Integration & Management
Applicable Industries
- Automotive
Applicable Functions
- Discrete Manufacturing
- Sales & Marketing
Use Cases
- Process Control & Optimization
- Supply Chain Visibility
Services
- System Integration
- Software Design & Engineering Services
About The Customer
Weifu High Technology Group is a manufacturer of fuel injection pumps for diesel engines and other automotive components. It is one of China Mechanical Enterprises Top 100 manufacturers. Founded in 1958, Weifu Group now has over 7,000 employees and is headquartered in Wuxi, Jiangsu, China. As one of China's leading providers of engine core components and electronic control solutions, Weifu serves some of the world’s largest car manufacturers. The components that Weifu manufactures are critical to the diesel engine market worldwide.
The Challenge
Weifu High Technology Group, a leading provider of engine core components and electronic control solutions, faced significant challenges due to the Covid-19 pandemic. Government policies to control the spread of the virus forced many companies to stop or reduce production, impacting the supply chain. Social distancing logistics seriously affected the supply of raw materials and components and hampered product sales. Meanwhile, customers were still demanding their essential car parts. However, the manufacturer’s customer relationship management platform was unable to handle the volume of requests and orders. The company launched three investigatory consulting projects: strategic, organizational and process domain to address the problems. The projects revealed a problem: Weifu had a lot of systems with a lot of processes, but it was not able to control and monitor these processes with the product it was using.
The Solution
Weifu discovered that ARIS was the best product for quickly starting process modeling, mining and monitoring. The company needed a platform to host its business processes where it could also model and monitor them. After some investigation, Weifu decided to implement ARIS Design & Strategy and ARIS Rollout & Change Management. Once Weifu completed the installation of the ARIS process management platform, it started process modeling, included rules, and formed an integrated and visual process management model. It is now using ARIS in the process department and almost every new process from the consulting project will be managed with ARIS Business Process Analysis (BPA). The next step in 2021 is expanding ARIS to every subsidiary of Weifu. It will also select one subsidiary to effect complete end-to-end process mining in 2021.
Operational Impact
Case Study missing?
Start adding your own!
Register with your work email and create a new case study profile for your business.
Related Case Studies.
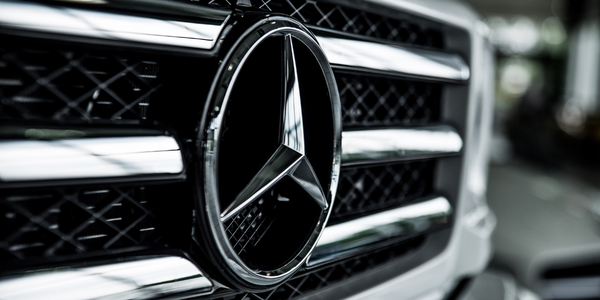
Case Study
Integral Plant Maintenance
Mercedes-Benz and his partner GAZ chose Siemens to be its maintenance partner at a new engine plant in Yaroslavl, Russia. The new plant offers a capacity to manufacture diesel engines for the Russian market, for locally produced Sprinter Classic. In addition to engines for the local market, the Yaroslavl plant will also produce spare parts. Mercedes-Benz Russia and his partner needed a service partner in order to ensure the operation of these lines in a maintenance partnership arrangement. The challenges included coordinating the entire maintenance management operation, in particular inspections, corrective and predictive maintenance activities, and the optimizing spare parts management. Siemens developed a customized maintenance solution that includes all electronic and mechanical maintenance activities (Integral Plant Maintenance).

Case Study
Monitoring of Pressure Pumps in Automotive Industry
A large German/American producer of auto parts uses high-pressure pumps to deburr machined parts as a part of its production and quality check process. They decided to monitor these pumps to make sure they work properly and that they can see any indications leading to a potential failure before it affects their process.