Technology Category
- Analytics & Modeling - Virtual & Augmented Reality Software
- Wearables - Augmented Reality Glasses, Headsets & Controllers
Applicable Industries
- Automotive
- Plastics
Applicable Functions
- Product Research & Development
Use Cases
- Augmented Reality
- Mixed Reality
About The Customer
ar engineers GmbH is a company that supports customers worldwide in the development of lightweight products. They work with industry leaders throughout the marine, automotive, and wind energy sectors. With over 10 years of experience in design, simulation, and implementation of composites products, the company provides extensive composites know-how combined with product planning and innovative technology. In this case, they were approached by the designers of a luxury super yacht to help reduce the weight of the vessel, specifically by investigating the use of carbon composites materials for several access doors used by the yacht crew and service members.
The Challenge
The designers of a luxury super yacht were faced with a significant challenge when the initial design of the vessel was approximately 300 tons above the desired weight. The high-quality super yachts are engineered to perfection, ensuring extraordinary handling in difficult sea conditions while combining maximum power with reduced emissions. To achieve this exceptional performance, the use of lightweight and high-strength materials like carbon composites is often necessary. The designers sought the expertise of ar engineers to find ways to reduce the weight of the yacht. The engineering team was tasked with investigating the use of carbon composites materials for several access doors used by the yacht crew and service members. They used ANSYS Composite PrepPost to determine the feasibility and to optimize the composites design.
The Solution
The engineering team at ar engineers used ANSYS Composite PrepPost to model and analyze the composite layup of the doors. They simulated the composites design using a parametric model from CAD. This allowed them to show the feasibility of the composite design under loading conditions required for certification by Germanischer Lloyd, the classification society for marine vessels. They also analyzed composite failure behavior, buckling, and deformations. The parametric model and intuitive composite workflow allowed for simple design studies and quick changes to the composite layup. ANSYS Composite PrepPost provided detailed evaluations of connection points, proving that the composites design was feasible. This enabled a very accurate cost estimate to be provided within five days.
Operational Impact
Quantitative Benefit
Case Study missing?
Start adding your own!
Register with your work email and create a new case study profile for your business.
Related Case Studies.
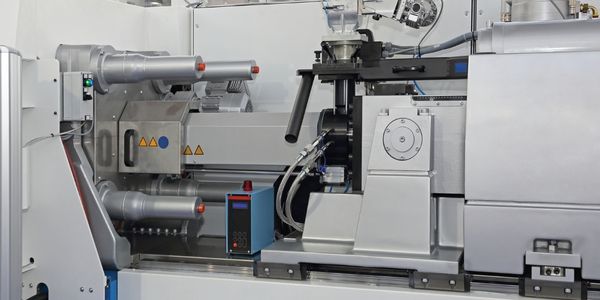
Case Study
Plastic Spoons Case study: Injection Moulding
In order to meet customer expectations by supplying a wide variety of packaging units, from 36 to 1000 spoons per package, a new production and packaging line needed to be built. DeSter wanted to achieve higher production capacity, lower cycle time and a high degree of operator friendliness with this new production line.
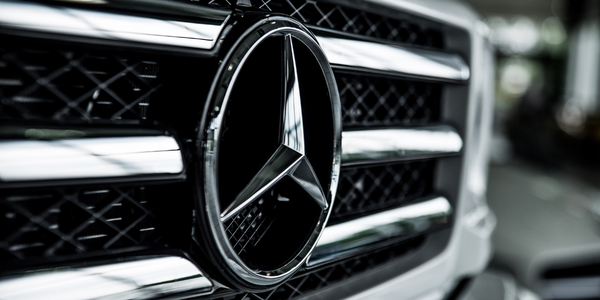
Case Study
Integral Plant Maintenance
Mercedes-Benz and his partner GAZ chose Siemens to be its maintenance partner at a new engine plant in Yaroslavl, Russia. The new plant offers a capacity to manufacture diesel engines for the Russian market, for locally produced Sprinter Classic. In addition to engines for the local market, the Yaroslavl plant will also produce spare parts. Mercedes-Benz Russia and his partner needed a service partner in order to ensure the operation of these lines in a maintenance partnership arrangement. The challenges included coordinating the entire maintenance management operation, in particular inspections, corrective and predictive maintenance activities, and the optimizing spare parts management. Siemens developed a customized maintenance solution that includes all electronic and mechanical maintenance activities (Integral Plant Maintenance).

Case Study
Monitoring of Pressure Pumps in Automotive Industry
A large German/American producer of auto parts uses high-pressure pumps to deburr machined parts as a part of its production and quality check process. They decided to monitor these pumps to make sure they work properly and that they can see any indications leading to a potential failure before it affects their process.