Customer Company Size
Large Corporate
Region
- Europe
- Asia
Country
- Germany
- India
Product
- EXALEAD OnePart
- SOLIDWORKS PDM Professional
Tech Stack
- SQL databases
Implementation Scale
- Enterprise-wide Deployment
Impact Metrics
- Productivity Improvements
- Cost Savings
Technology Category
- Application Infrastructure & Middleware - Data Exchange & Integration
- Analytics & Modeling - Data Mining
Applicable Industries
- Equipment & Machinery
Applicable Functions
- Discrete Manufacturing
- Product Research & Development
Use Cases
- Manufacturing System Automation
- Predictive Maintenance
Services
- System Integration
- Software Design & Engineering Services
About The Customer
Wittur is a leading global supplier of components, modules and systems for the elevator industry. The company started out in 1968 as a manufacturer and distributor of elevator swing doors and experienced steady growth since then, both organically and through acquisitions. Wittur manufactures a wide range of elevator components from sophisticated mechatronic mechanisms for the cabin and landing doors to other components that include gearless drives, slings, safety gears, cars and braking systems. The company focuses on comfort and safety when designing its products. Wittur's customers are global elevator installers that include Kone, Otis, Schindler, Hitachi, and ThyssenKrupp Elevator as well as smaller independent installers operating on a more local scale. One of Wittur’s strengths is its ability to accurately analyze market trends, which enables it to anticipate its customers’ needs for innovative products.
The Challenge
Wittur, a leading manufacturer of elevator components, modules and systems, faced a challenge following a series of acquisitions. The company needed to leverage the massive amount of diverse data across its globally-located plants and to increase part reuse. As it acquired companies and established production plants and sales organizations around the world, Wittur found itself faced with a diverse IT environment that prevented its employees from easily finding and leveraging all of its information. Data was stored in different legacy SQL databases each with their own material codes, norms and structure, which had to be sifted through individually. This was extremely time-consuming. Another challenge was to reduce the number of duplicate parts in its system. The engineers were having difficulty finding existing parts for new projects, so they preferred redesigning them, even though, in many cases, a similar part existed. This continuous duplication of parts required additional storage space. It also drove up costs as redesigning a part includes R&D, manufacturing, testing, logistics and inventory, all activities that could be avoided if they could just find an existing part to fit the bill.
The Solution
To meet its challenges, Wittur chose the EXALEAD OnePart application as its global search solution. The company initially invested in 15 seats of OnePart for its 3D geometry searches and more recently deployed EXALEAD for its 2D drawing and metadata searches. For 3D search, one of OnePart’s advantages is its shape search feature, which locates part similarities and displays the closest parts in the search results. For 2D drawings, Wittur created its Drawing Information System (DIS), which is powered by EXALEAD. They are not only able to find the 2D drawings themselves, but all the metadata - part tolerances, material information, and where drawings are used - associated to each drawing. They can also display a component’s design history and show the latest revisions. Wittur takes advantage of EXALEAD’s many search possibilities by using its full-text search features, parent-child relationships, attributes-based data such as drawing codes, and filtering possibilities to narrow down the search.
Operational Impact
Quantitative Benefit
Case Study missing?
Start adding your own!
Register with your work email and create a new case study profile for your business.
Related Case Studies.
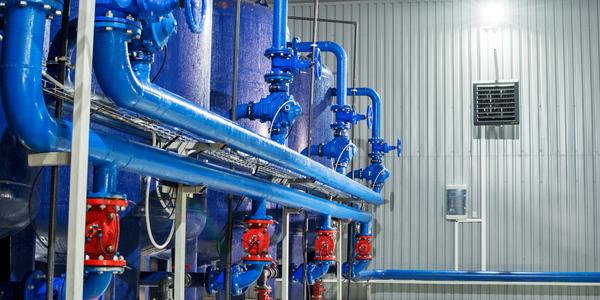
Case Study
Smart Water Filtration Systems
Before working with Ayla Networks, Ozner was already using cloud connectivity to identify and solve water-filtration system malfunctions as well as to monitor filter cartridges for replacements.But, in June 2015, Ozner executives talked with Ayla about how the company might further improve its water systems with IoT technology. They liked what they heard from Ayla, but the executives needed to be sure that Ayla’s Agile IoT Platform provided the security and reliability Ozner required.
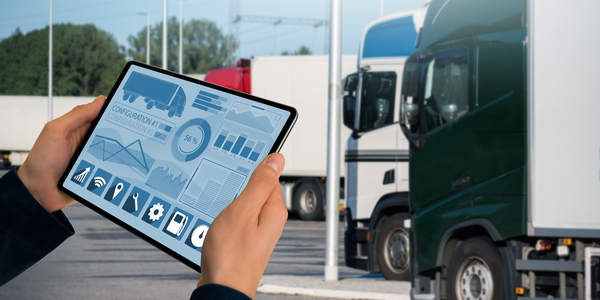
Case Study
IoT enabled Fleet Management with MindSphere
In view of growing competition, Gämmerler had a strong need to remain competitive via process optimization, reliability and gentle handling of printed products, even at highest press speeds. In addition, a digitalization initiative also included developing a key differentiation via data-driven services offers.
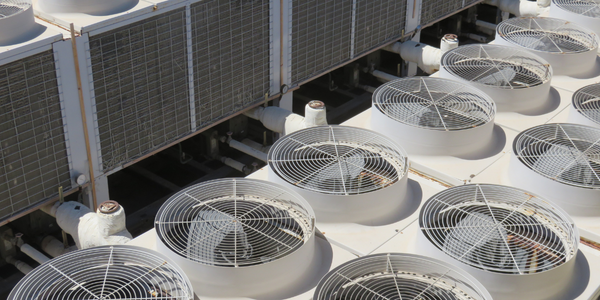
Case Study
Predictive Maintenance for Industrial Chillers
For global leaders in the industrial chiller manufacturing, reliability of the entire production process is of the utmost importance. Chillers are refrigeration systems that produce ice water to provide cooling for a process or industrial application. One of those leaders sought a way to respond to asset performance issues, even before they occur. The intelligence to guarantee maximum reliability of cooling devices is embedded (pre-alarming). A pre-alarming phase means that the cooling device still works, but symptoms may appear, telling manufacturers that a failure is likely to occur in the near future. Chillers who are not internet connected at that moment, provide little insight in this pre-alarming phase.
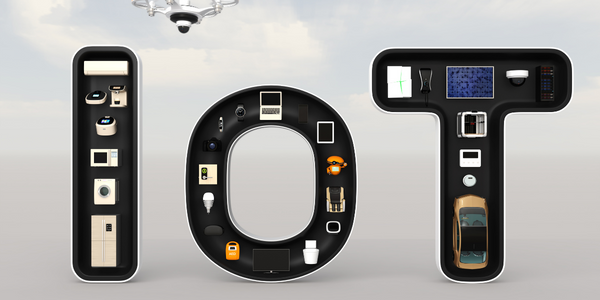
Case Study
Premium Appliance Producer Innovates with Internet of Everything
Sub-Zero faced the largest product launch in the company’s history:It wanted to launch 60 new products as scheduled while simultaneously opening a new “greenfield” production facility, yet still adhering to stringent quality requirements and manage issues from new supply-chain partners. A the same time, it wanted to increase staff productivity time and collaboration while reducing travel and costs.
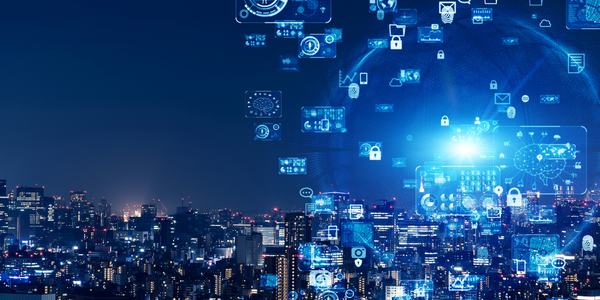
Case Study
Integration of PLC with IoT for Bosch Rexroth
The application arises from the need to monitor and anticipate the problems of one or more machines managed by a PLC. These problems, often resulting from the accumulation over time of small discrepancies, require, when they occur, ex post technical operations maintenance.
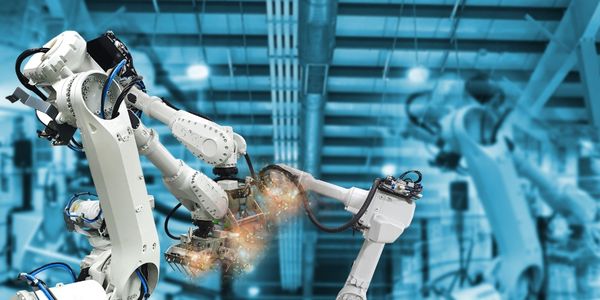
Case Study
Robot Saves Money and Time for US Custom Molding Company
Injection Technology (Itech) is a custom molder for a variety of clients that require precision plastic parts for such products as electric meter covers, dental appliance cases and spools. With 95 employees operating 23 molding machines in a 30,000 square foot plant, Itech wanted to reduce man hours and increase efficiency.