Technology Category
- Sensors - Accelerometers
- Sensors - Acoustic Sensors
Applicable Industries
- Electronics
- Equipment & Machinery
Applicable Functions
- Product Research & Development
Use Cases
- Mesh Networks
- Virtual Prototyping & Product Testing
Services
- Hardware Design & Engineering Services
- System Integration
About The Customer
Zyvex Corporation, based in Richardson, TX, is the first molecular nanotechnology development company and an aggressive developer of commercial nanotech applications. The company has three product lines – materials, tools, and structures – and is focused on three market segments: aerospace and defense; healthcare and medicine; and electronics and semiconductors. Zyvex customers include industry leaders such as Boeing, Easton Sports, Honeywell International, and Texas Instruments. The company is active in several areas of research, funded by grants from state and federal agencies.
The Challenge
Zyvex Corporation, a leading molecular nanotechnology development company, was faced with the challenge of developing micro-electro-mechanical systems (MEMS) technology that could enable new nanotech applications. The majority of commercially available MEMS devices were essentially two-dimensional, grown onto or etched from a flat substrate. However, Zyvex saw the potential for MEMS technology that provided structures and devices with 3D characteristics. The challenge lay in the manufacturing process. Building a 3D MEMS device required some form of assembly to raise structures from the plane of fabrication and move them into the appropriate position. Conventional assembly methods were costly and alternative methods had limitations. Furthermore, the use of computational analysis was critical to the design of microstructures, as a microfabrication cycle could take up to four months.
The Solution
Zyvex Corporation developed a unique approach to overcome these challenges. They designed compliant MEMS components that could be de-tethered, removed from the plane of the wafer, and assembled, all in an automated process. This was achieved through a directed pick-and-place microassembly process using MEMS end-effectors and high-precision robotics. This made it possible to integrate microcomponents that had been fabricated in separate processes. Zyvex also heavily relied on finite-element analysis (FEA) tools in their MEMS design process. These tools allowed them to design, analyze, and test MEMS structures, accelerating their work significantly. They used advanced FEA tools like Altair HyperMesh for more control over the mesh densities and visualization capabilities of post-processing tools like Altair HyperView for understanding the performance and function of MEMS devices.
Operational Impact
Quantitative Benefit
Case Study missing?
Start adding your own!
Register with your work email and create a new case study profile for your business.
Related Case Studies.
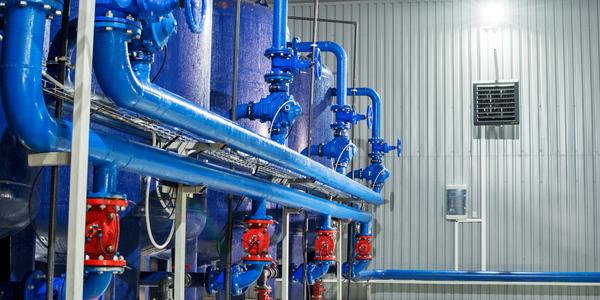
Case Study
Smart Water Filtration Systems
Before working with Ayla Networks, Ozner was already using cloud connectivity to identify and solve water-filtration system malfunctions as well as to monitor filter cartridges for replacements.But, in June 2015, Ozner executives talked with Ayla about how the company might further improve its water systems with IoT technology. They liked what they heard from Ayla, but the executives needed to be sure that Ayla’s Agile IoT Platform provided the security and reliability Ozner required.
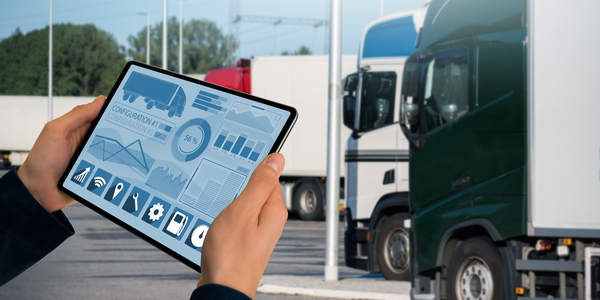
Case Study
IoT enabled Fleet Management with MindSphere
In view of growing competition, Gämmerler had a strong need to remain competitive via process optimization, reliability and gentle handling of printed products, even at highest press speeds. In addition, a digitalization initiative also included developing a key differentiation via data-driven services offers.
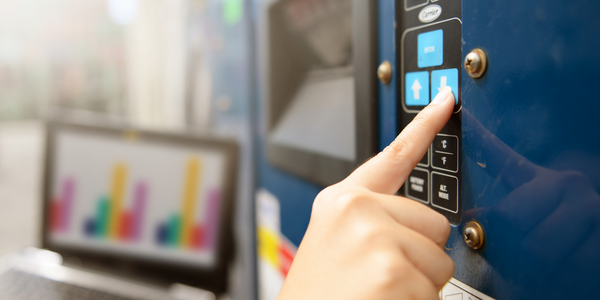
Case Study
Remote Temperature Monitoring of Perishable Goods Saves Money
RMONI was facing temperature monitoring challenges in a cold chain business. A cold chain must be established and maintained to ensure goods have been properly refrigerated during every step of the process, making temperature monitoring a critical business function. Manual registration practice can be very costly, labor intensive and prone to mistakes.
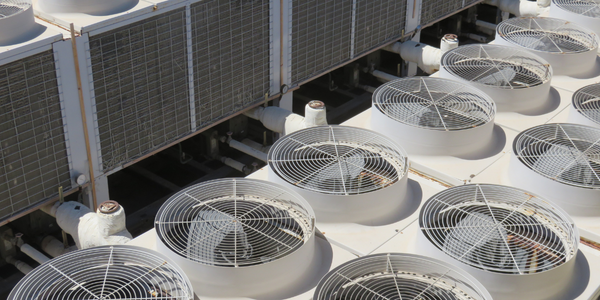
Case Study
Predictive Maintenance for Industrial Chillers
For global leaders in the industrial chiller manufacturing, reliability of the entire production process is of the utmost importance. Chillers are refrigeration systems that produce ice water to provide cooling for a process or industrial application. One of those leaders sought a way to respond to asset performance issues, even before they occur. The intelligence to guarantee maximum reliability of cooling devices is embedded (pre-alarming). A pre-alarming phase means that the cooling device still works, but symptoms may appear, telling manufacturers that a failure is likely to occur in the near future. Chillers who are not internet connected at that moment, provide little insight in this pre-alarming phase.
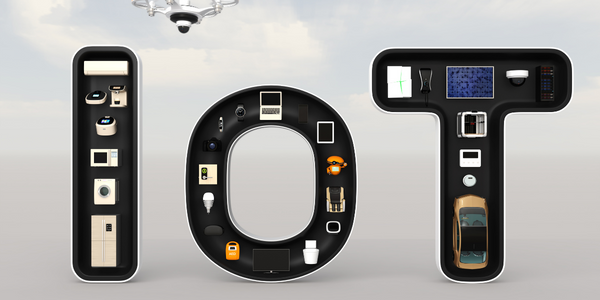
Case Study
Premium Appliance Producer Innovates with Internet of Everything
Sub-Zero faced the largest product launch in the company’s history:It wanted to launch 60 new products as scheduled while simultaneously opening a new “greenfield” production facility, yet still adhering to stringent quality requirements and manage issues from new supply-chain partners. A the same time, it wanted to increase staff productivity time and collaboration while reducing travel and costs.