Camelot 3PL Software
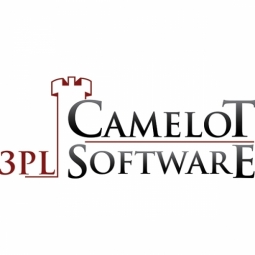
Overview
HQ Location
United States
|
Year Founded
1984
|
Company Type
Private
|
Revenue
< $10m
|
Employees
11 - 50
|
Website
|
Twitter Handle
|
Company Description
Camelot 3PL Software (www.3PLsoftware.com) is a pioneer in the Warehouse Management System (WMS) industry. Since 1987, Camelot has provided 3PL companies with operational technology geared towards Inventory Management, EDI, Wireless Scanning, Transportation Management, etc.
Camelot is one of the first in the industry to introduce a complete Business Management System that encompasses 3PL Warehouse Management (WMS), Transportation Management (TMS), Accounting and CRM all in one seamless software solution.
IoT Snapshot
Camelot 3PL Software is a provider of Industrial IoT infrastructure as a service (iaas), application infrastructure and middleware, functional applications, and robots technologies, and also active in the electronics, packaging, specialty vehicles, and transportation industries.
Technologies
Use Cases
Functional Areas
Industries
Services
Technology Stack
Camelot 3PL Software’s Technology Stack maps Camelot 3PL Software’s participation in the infrastructure as a service (iaas), application infrastructure and middleware, functional applications, and robots IoT Technology stack.
-
Devices Layer
-
Edge Layer
-
Cloud Layer
-
Application Layer
-
Supporting Technologies
Technological Capability:
None
Minor
Moderate
Strong
Supplier missing?
Start adding your own!
Register with your work email and create a new supplier profile for your business.
Case Studies.
Case Study
InterChange Group Enhances Cold Storage Efficiency with IoT Integration
InterChange Group, a cold-storage warehousing and distribution company, was faced with the challenge of increasing the efficiency of its cold storage facility to better service a local customer. The company needed to prove its capability to handle growing volumes in the future. The specific challenge was to integrate their new fleet of semi-automated forklifts with the Camelot Excalibur Warehouse Management System (WMS). The deployment of this technology investment, especially with temperature and date-sensitive food products, within a tight timeline, posed significant challenges.
Case Study
IoT Implementation in Winchester Cold Storage for Improved Accuracy
Winchester Cold Storage, a company providing food grade freezer and temperature-controlled storage solutions, was facing challenges in improving the accuracy and automation of their receiving operations. Despite having an impressive accuracy rate of 99.8%, the company was looking for ways to further enhance this. The inaccuracies primarily occurred during the shipping of smaller orders that were intended to be case-picked but ended up being shipped as full pallets. Winchester needed a system that could verify the contents remaining in the bin location as a second verification of the pick quantity accuracy. The company required a solution that could implement count back checks through the use of MobileLink tablet scanners, include a system to check using counts for Bin or Pallet ID, alert the picker if the count back quantity is incorrect, and send exception notifications via email to the supervisor.
Case Study
Revamping Warehouse Management System: A Case Study of The Order Fulfillment Group
The Order Fulfillment Group (TOFG), a third-party logistics provider (3PL) known for its efficiency and quick turnarounds, was facing a significant challenge. The company had outgrown its legacy warehouse management system (WMS), an Oracle database that had been continually customized over the years. The need for a cloud-based system that was as cutting-edge as the company’s services, but flexible enough to accommodate TOFG’s unique needs was evident. Some of these needs, such as the way the 3PL charges freight, were related to its own business practices, while others were client-specific. The Director of Operations, Robert Kolpien, was frustrated by the lack of flexibility among many software providers. He was looking for a solution that would not force their unique requirements to fit into a standard model.
Case Study
Improving Order Accuracy and Reducing Labor Efforts: A Case Study on Colorado Distribution Group
Colorado Distribution Group (CDG), a Denver-based company providing small parcel fulfillment services, was facing challenges in improving the accuracy of packing high-volume orders and reducing unnecessary labor efforts for printing labels and shipping documentation. The process of picking and packing orders required at least three warehouse operation staff members per shift. When an order was received, the information was communicated to the floor for picking. After the shipment was picked, it was moved to the packing area for packaging and labeling. The cartons were then packed and verified for order accuracy. Finally, the shipping label and packing list were printed to complete the order. CDG was looking for a solution to improve their packing operations and reduce the labor required.