公司规模
Large Corporate
地区
- Europe
国家
- Switzerland
产品
- Wonderware ActiveFactory
- Wonderware Development Studio
- Wonderware Historian
- Wonderware Information Server
- Wonderware Manufacturing Execution Module
技术栈
- Wonderware Software
- Automation Solution
实施规模
- Enterprise-wide Deployment
影响指标
- Productivity Improvements
- Cost Savings
技术
- 应用基础设施与中间件 - 数据交换与集成
适用行业
- 化学品
适用功能
- 离散制造
- 质量保证
用例
- 自动化制造系统
- 质量预测分析
服务
- 系统集成
- 软件设计与工程服务
关于客户
sia Abrasives Industries AG is one of the world's leading manufacturers of coated abrasives. The company offers a product range of several thousand items that are subject to continuous improvement. The coated abrasives produced at Frauenfeld are made up of a carrier material, such as paper, tissue, vulcanized fiber or plastic film. Through a continuous process, abrasive grains are applied to the backing and anchored by bonding adhesives. sia Abrasives products are distributed worldwide and are used in metalworking, woodworking, automotive bodywork and panel production. The company employs approximately 1,100 people worldwide, 690 of which work in Frauenfeld. In 2007, the business volume reached 298 million CHF, and great attention is being paid to the performance and efficiency of the enterprise.
挑战
sia Abrasives Industries AG, one of the world's leading manufacturers of coated abrasives, was facing challenges with its outdated and inconsistent systems. The lack of connection between the controls of the individual production units made the planning of various production processes and the management of the machines' setup highly laborious and inefficient. Moreover, manufacturing data was administered via different, non-compatible systems, leading to errors caused by media conversions. As process data accumulated locally, significant efforts had to be made for consistent quality control due to the lack of a common database. The company decided to introduce an extensive automation solution that facilitates production control and reporting.
解决方案
sia Abrasives decided to entrust the challenge to Wonderware software and acs ag, a system integrator from Wil, Switzerland. The implementation began in 2003 with the final goal of creating a paperless solution that connected the plant floor to the production planning and control (PPC) system. All plant information is now stored centrally through a Wonderware Historian. Thanks to this high-performance real-time database, the information from the control system used for planning and reporting is available to all work stations, based on the different roles and authorization of the personnel. The Wonderware Manufacturing Execution Module and the open interfaces provided by Wonderware software enables the standardization of data flow. The solution enables production orders to be centrally dispatched via a PPC work station. At any time, it is possible to check and supervise the status of batches in the various process steps and the plant floor is constantly updated with real-time production order information.
运营影响
Case Study missing?
Start adding your own!
Register with your work email and create a new case study profile for your business.
相关案例.
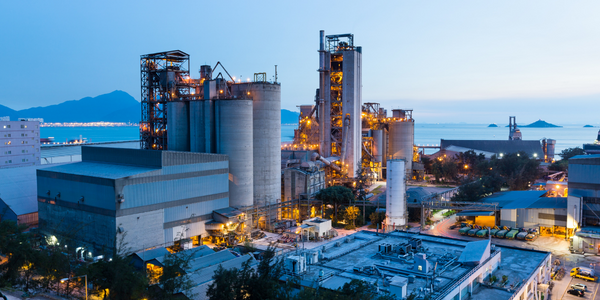
Case Study
Honeywell - Tata Chemicals Improves Data Accessibility with OneWireless
Tata was facing data accessibility challenges in the cement plant control room tapping signals from remote process control areas and other distant locations, including the gas scrubber. Tata needed a wireless solution to extend its control network securely to remote locations that would also provide seamless communication with existing control applications.

Case Study
Advanced Elastomer Systems Upgrades Production
In order to maintain its share of the international market for thermoplastic elastomers AES recently expanded its Florida plant by adding a new production line. While the existing lines were operating satisfactorily using a PROVOX distributed control system with traditional analog I/O, AES wanted advanced technology on the new line for greater economy, efficiency, and reliability. AES officials were anxious to get this line into production to meet incoming orders, but two hurricanes slowed construction.
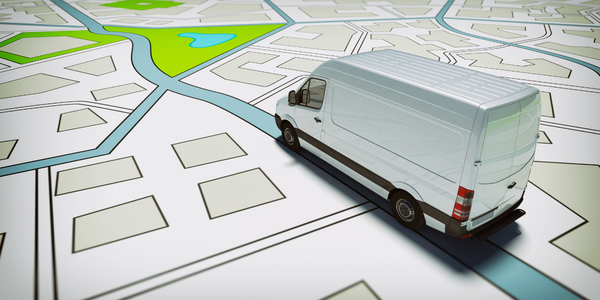
Case Study
Wireless GPS Tracking & Security Monitoring
Enhancing the security of hazardous freight and ensuring compliance with Homeland Security’s Transportation Security Administration mandate that all trains carrying chemicals capable of creating a toxic inhalation condition are equipped with on-board safety monitoring systems.

Case Study
Field Device Asset Management For Chemical Company in China
Chinese chemical subsidiary of multinational corporation serves customers throughout the world. Sales offices and research and technology centers are strategically located to provide rapid response to customer requests. Just two workers were assigned to maintain thousands of intelligent instruments in three production units, so they could do little more than react to device issues as they appeared. This costly maintenance method inevitably led to unexpected downtime when a critical instrument failed. Plant management recognized the need to change from reactive to predictive maintenance for all assets, including instruments and control valves, but help was needed in implementing such a technology-based initiative.
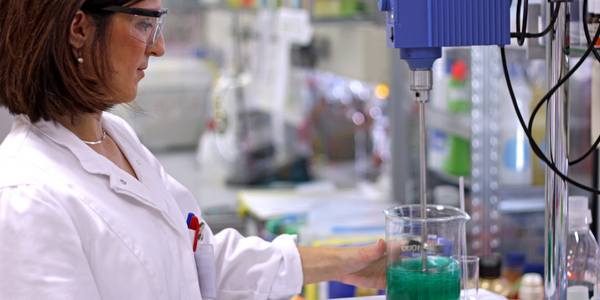
Case Study
Industrial Workforce Mobility for Improved Safety & Operations
Huntsman Corporation, a global manufacturer and marketer of differentiated chemicals, undertook an aggressive program to eliminate injuries, product defects, and environmental releases at their Port Neches facility. Termed “Project Zero”, this program required a completely mobile solution to empower operations and maintenance personnel to capture defects, track work progress and make process and safety related decisions in real-time.