技术
- 网络安全和隐私 - 网络安全
- 平台即服务 (PaaS) - 应用开发平台
适用行业
- 服装
- 金融与保险
适用功能
- 维护
- 产品研发
用例
- 交通监控
- 交通模拟
服务
- 云规划/设计/实施服务
- 系统集成
关于客户
ARIGATOBANK Inc. 是一家总部位于东京的金融服务企业,在其 kifutown 捐赠平台上充当捐赠者和接受者之间的中介。该平台取得了显着增长,截至 2022 年 3 月,已有 2,000 多个捐赠项目达到“存款”状态。股东包括 ZOZO 创始人前泽友作。
挑战
ARIGATOBANK 需要开发一个可扩展的平台来支持其 kifutown 捐赠平台的高流量激增,特别是考虑到高调活动的潜在影响以及前泽友作的参与。
解决方案
ARIGATOBANK 实施了 Google Cloud 技术,包括 Google Kubernetes Engine (GKE)、Cloud Spanner、Cloud Load Balancing 和 Firebase,为 kifutown 构建灵活且可扩展的架构。他们还利用 Cloud Armor 实现网络安全,利用 Cloud NAT 和 Cloud Router 实现网络服务。开发团队选择 Kubernetes 是因为其低成本,而选择 Cloud Spanner 是因为其强大的事务引擎。
运营影响
数量效益
Case Study missing?
Start adding your own!
Register with your work email and create a new case study profile for your business.
相关案例.
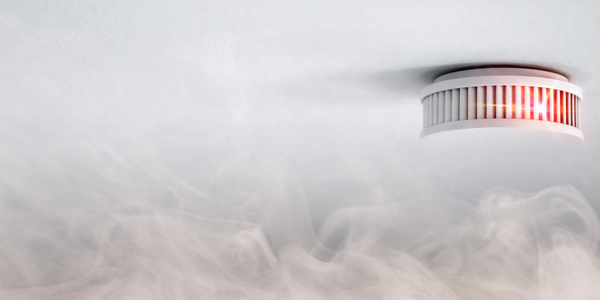
Case Study
Fire Alarm System and Remote Monitoring Sytem
Fire alarm systems are essential in providing an early warning in the event of fire. They help to save lives and protect property whilst also fulfilling the needs of insurance companies and government departments.Fire alarm systems typically consist of several inter-linked components, such as smoke detectors, heat detector, carbon monoxide, manual call points, sounders, alarm and buzzer. The fire alarm system should give immediate information in order to prevent the fire spread and protect live and property.To get maximum protection a shoe manufacturer in Indonesia opted for a new fire alarm system to monitor 13 production sites spread over 160 hectars. Although the company had an existing fire alarm system, it could not be monitored remotely.It was essential that the new system would be able to be monitored from a central control room. It needed to be able to connect to the existing smoke detector and manual call point. Information should be easily collected and passed on to the Supervisory Control and Data Acquisition (SCADA) system. Furthermore, the system should have several features such as alarm management, auto reporting, being connected to many client computers without additional cost, and run 24/7 without fails. The company also needed a system which could be implemented without changing the architecture of the existing fire alarm system.
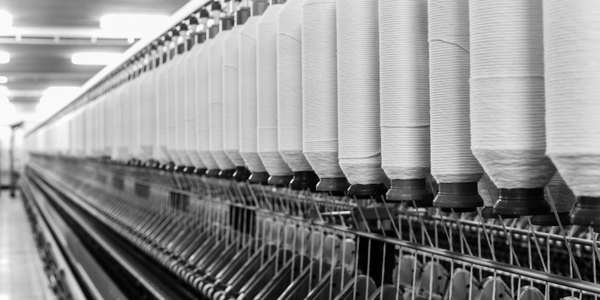
Case Study
IoT Applications and Upgrades in Textile Plant
At any given time, the textile company’s manufacturing facility has up to 2,000 textile carts in use. These carts are pushed from room to room, carrying materials or semi-finished products. Previously, a paper with a hand-written description was attached to each cart. This traditional method of processing made product tracking extremely difficult. Additionally, making sure that every cart of materials or semi-finished products went to its correct processing work station was also a problem. Therefore, the company desired an intelligent solution for tracking assets at their factories. They also wanted a solution that would help them collect process data so they could improve their manufacturing efficiency.
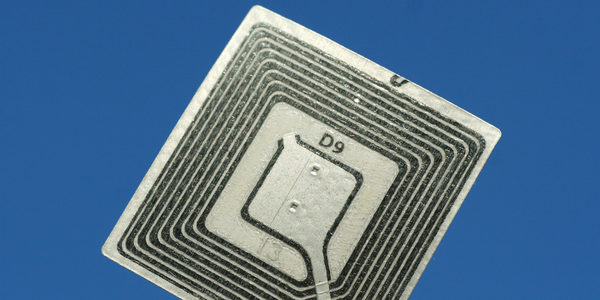
Case Study
Retailer Uses RFID Scanner to Improve Efficiency
Patrizia Pepe wished to improve the logistics of their warehouse: accepting incoming goods from their production sites, movement of items throughout
the warehouse, and packaging of goods for distribution to the retail locations. They initially tried to use barcodes for this function. Because barcodes must be individually scanned within a line-of-sight, the acceptance of goods coming into the warehouse was too time consuming. Working with the University of Florence, Patrizia Pepe instituted a five-month pilot project beginning in August of 2009 to test the validity of an RFID solution. The pilot involved tagging of about 60,000 items for the second seasonal collection, and convinced the company to move forward with tagging all items.

Case Study
Monitoring and Controlling Automatic Mixing and Dispensing Machines
As technology advances, textile manufacturing has been transformed from a labor-intensive to a partially or fully automated industry. Automation is significant in all segments of textile production - from spinning to printing, and textile machinery manufacturers are constantly searching for new technologies and automation processes will increase the productivity of their machines. The color paste mixing and dispensing machine is an essential part of the printing and dyeing process. With the advantage of automatically computerized controls and database management, the system can significantly improve its dispensing precision, working efficiency and production quality as well as reducing material consumption.
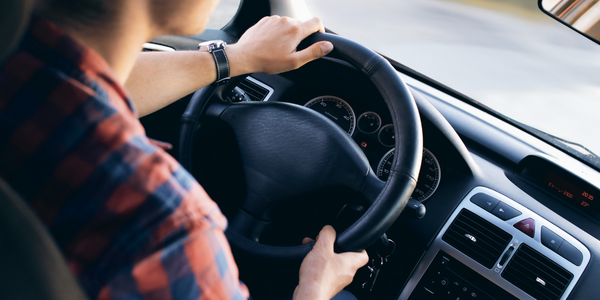
Case Study
Real-time In-vehicle Monitoring
The telematic solution provides this vital premium-adjusting information. The solution also helps detect and deter vehicle or trailer theft – as soon as a theft occurs, monitoring personnel can alert the appropriate authorities, providing an exact location.“With more and more insurance companies and major fleet operators interested in monitoring driver behaviour on the grounds of road safety, efficient logistics and costs, the market for this type of device and associated e-business services is growing rapidly within Italy and the rest of Europe,” says Franco.“The insurance companies are especially interested in the pay-per-use and pay-as-you-drive applications while other organisations employ the technology for road user charging.”“One million vehicles in Italy currently carry such devices and forecasts indicate that the European market will increase tenfold by 2014.However, for our technology to work effectively, we needed a highly reliable wireless data network to carry the information between the vehicles and monitoring stations.”