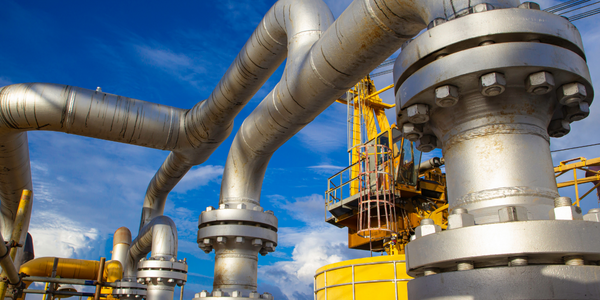
技术
- 分析与建模 - 预测分析
- 功能应用 - 远程监控系统
- 传感器 - 气体传感器
- 传感器 - 液位传感器
适用行业
- 石油和天然气
适用功能
- 维护
用例
- 预测性维护
客户
丛林能源
关于客户
这家总部位于俄克拉荷马城的独立公司已探明储量超过 1.5 亿桶原油当量,并拥有超过 3,000 口生产井的权益。它主要在俄克拉荷马州、堪萨斯州和二叠纪盆地的成熟油气田开展业务。
挑战
在花费数百万用于提高石油采收率 (EOR) 基础设施(包括二氧化碳、压缩机、管道、注入井口和流体分离器)之后,随着石油产量的增加,Chaparral 开始看到其长期投资得到回报。但是,当 CO2 压缩机发生故障时,管道中的 CO2 量会骤降 50% 或更多。操作员需要预测智能来防止此类事件发生。
解决方案
Chaparral 选择 Veros ForeSight 来提供工业资产监控解决方案。项目团队选择了 12 台压缩机和 1 台泵来监控堪萨斯州 Liberal 的 CO2 压缩设施。
收集的数据
Asset Performance, Asset Utilization, CO2 consumption, Fault Detection, Oil Level
运营影响
数量效益
Case Study missing?
Start adding your own!
Register with your work email and create a new case study profile for your business.
相关案例.
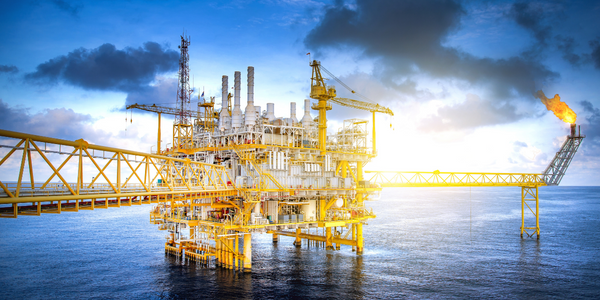
Case Study
Taking Oil and Gas Exploration to the Next Level
DownUnder GeoSolutions (DUG) wanted to increase computing performance by 5 to 10 times to improve seismic processing. The solution must build on current architecture software investments without sacrificing existing software and scale computing without scaling IT infrastructure costs.
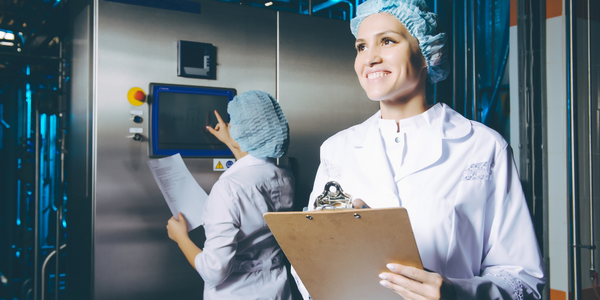
Case Study
Remote Wellhead Monitoring
Each wellhead was equipped with various sensors and meters that needed to be monitored and controlled from a central HMI, often miles away from the assets in the field. Redundant solar and wind generators were installed at each wellhead to support the electrical needs of the pumpstations, temperature meters, cameras, and cellular modules. In addition to asset management and remote control capabilities, data logging for remote surveillance and alarm notifications was a key demand from the customer. Terra Ferma’s solution needed to be power efficient, reliable, and capable of supporting high-bandwidth data-feeds. They needed a multi-link cellular connection to a central server that sustained reliable and redundant monitoring and control of flow meters, temperature sensors, power supply, and event-logging; including video and image files. This open-standard network needed to interface with the existing SCADA and proprietary network management software.
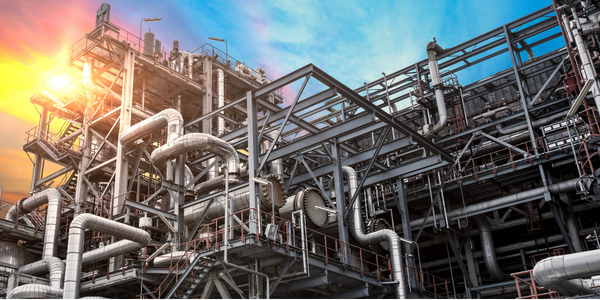
Case Study
Refinery Saves Over $700,000 with Smart Wireless
One of the largest petroleum refineries in the world is equipped to refine various types of crude oil and manufacture various grades of fuel from motor gasoline to Aviation Turbine Fuel. Due to wear and tear, eight hydrogen valves in each refinery were leaking, and each cost $1800 per ton of hydrogen vented. The plant also had leakage on nearly 30 flare control hydrocarbon valves. The refinery wanted a continuous, online monitoring system that could catch leaks early, minimize hydrogen and hydrocarbon production losses, and improve safety for maintenance.