公司规模
Large Corporate
国家
- Worldwide
产品
- webMethods product suite
技术栈
- XML
- Web services
实施规模
- Enterprise-wide Deployment
影响指标
- Productivity Improvements
- Customer Satisfaction
技术
- 应用基础设施与中间件 - API 集成与管理
- 应用基础设施与中间件 - 数据交换与集成
适用行业
- 包装
适用功能
- 采购
- 销售与市场营销
用例
- 供应链可见性(SCV)
- 库存管理
服务
- 系统集成
关于客户
Mondi Packaging is a growth-oriented supplier of packaging solutions and high-performance materials. The company employs around 14,000 people in 124 sites worldwide. In 2004, the group revenues were well over two billion euros, of which 630 million were generated by the bags business unit alone. This division manufactures paper sacks tailored to the individual needs of its customers. Mondi Packaging Bags is the world leader by market share in this industry sector and a pioneer in its quality and service offering. The company has set itself some demanding objectives, including extending its leadership position in innovation and ensuring that all management decisions have a positive impact on competitiveness, as well as on the bottom line.
挑战
Mondi Packaging Bags’ site acquisition strategy resulted in a heterogeneous IT landscape structure that was rapidly becoming too complex. Over 20 different back-office systems were running on a wide variety of platforms and with varying software release statuses — all systems needed to be connected to the sales portal. The company was also planning to gradually implement SAP systems in all of its larger production sites. The challenge was to create an integration layer to connect all company systems and all of its customers’ procurement systems to the sales portal.
解决方案
Mondi Packaging needed to create an integration layer to connect all company systems and all of its customers’ procurement systems to the sales portal. Using the webMethods product suite, customer procurement, accounting, production planning and control systems are now connected to the portal to underpin Collaborative Planning, Forecasting and Replenishment standards. The sales portal is a globally accessible, open supply chain management infrastructure that was developed using the webMethods product suite. Customer procurement, accounting, production planning and control systems can be easily connected to the portal to underpin Collaborative Planning, Forecasting and Replenishment (CPRF) standards. Customers can search all Mondi Packaging Bags sites for their stock levels, turnover, current order status, and of course they can also enter new orders.
运营影响
Case Study missing?
Start adding your own!
Register with your work email and create a new case study profile for your business.
相关案例.

Case Study
IoT Data Analytics Case Study - Packaging Films Manufacturer
The company manufactures packaging films on made to order or configure to order basis. Every order has a different set of requirements from the product characteristics perspective and hence requires machine’s settings to be adjusted accordingly. If the film quality does not meet the required standards, the degraded quality impacts customer delivery causes customer dissatisfaction and results in lower margins. The biggest challenge was to identify the real root cause and devise a remedy for that.
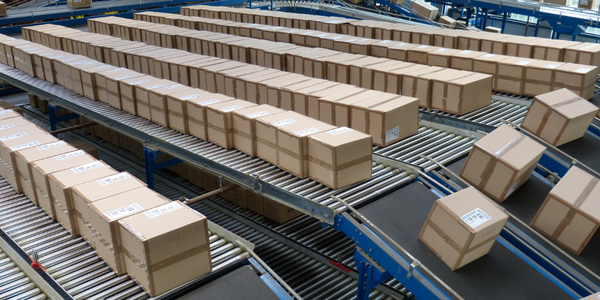
Case Study
Zenon the Ideal Basis for An Ergonomic HMI
KHS develops and produces machines and equipment for filling and packaging in the drinks industry. Because drinks manufacturing, filling and packaging consist of a number of highly complex processes, the user-friendly and intuitive operation of equipment is increasingly gaining in significance. In order to design these processes as simple as possible for the user, KHS decided to introduce a uniform, transparent and standardized solution to the company. The HMI interface should meet the requirement for people with different qualifications and enable them to work on a standard platform.
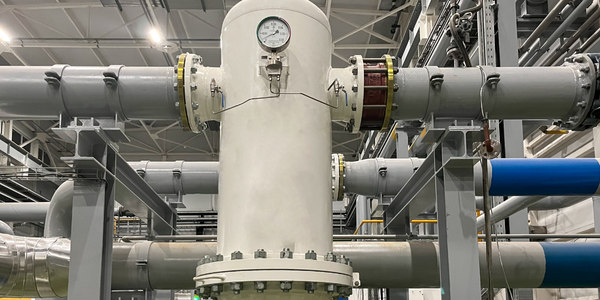
Case Study
Sparks Dynamics Assists Atlas Container Secure a $15,000 BGE Energy Rebate
The ReMASTER Compressed Air Monitoring system was installed in 2015. This system is capable of monitoring compressed air system parameters on a continuous basis and transferring that information to a cloud server which can be accessed by Atlas Container personnel, Industrial Diagnostics and Sparks Dynamics. This information was collected into a database which can be exported to an Excel spreadsheet or displayed graphically using Sparks Dynamics ViewMaster Software. The average annual compressed air electricity expense was estimated to be approximately $116,000. This is based on an incremental $/KWh electric rate of $.091 per KWh and an estimated compressed air energy consumption of 1,279,200 KWH. The implementation phase of Energy Conservation Measures (ECMs) for the Compressed Air System included: • Identification and repair of compressed air leaks • Understanding of compressed air usage per manufacturing machine and installation of shut off valves when the machines are no longer in production mode • Identification of misapplications of compressed air to include blow offs, venturis, and cooling scenarios • Understand system pressure requirements and potential installation of point of use pressure regulation.
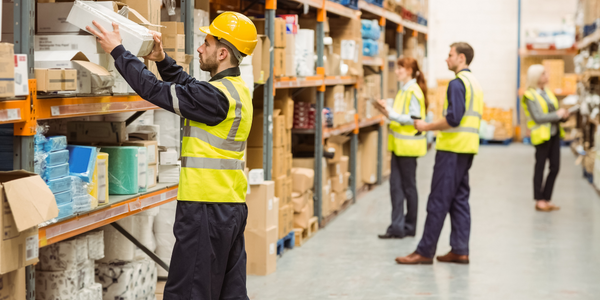
Case Study
Automated Pallet Labeling Solution for SPR Packaging
SPR Packaging, an American supplier of packaging solutions, was in search of an automated pallet labeling solution that could meet their immediate and future needs. They aimed to equip their lines with automatic printer applicators, but also required a solution that could interface with their accounting software. The challenge was to find a system that could read a 2D code on pallets at the stretch wrapper, track the pallet, and flag any pallets with unread barcodes for inspection. The pallets could be single or double stacked, and the system needed to be able to differentiate between the two. SPR Packaging sought a system integrator with extensive experience in advanced printing and tracking solutions to provide a complete traceability system.
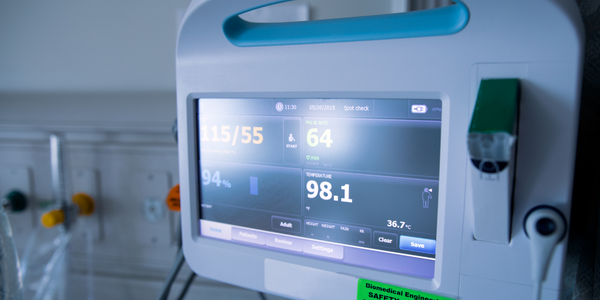
Case Study
Mondi Implements Statistics-Based Health Monitoring and Predictive Maintenance
The extrusion and other machines at Mondi’s plant are large and complex, measuring up to 50 meters long and 15 meters high. Each machine is controlled by up to five programmable logic controllers (PLCs), which log temperature, pressure, velocity, and other performance parameters from the machine’s sensors. Each machine records 300–400 parameter values every minute, generating 7 gigabytes of data daily.Mondi faced several challenges in using this data for predictive maintenance. First, the plant personnel had limited experience with statistical analysis and machine learning. They needed to evaluate a variety of machine learning approaches to identify which produced the most accurate results for their data. They also needed to develop an application that presented the results clearly and immediately to machine operators. Lastly, they needed to package this application for continuous use in a production environment.
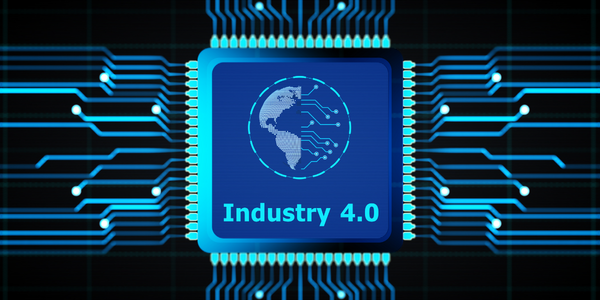
Case Study
Industry 4.0 at ALPLA: Enhancing Factory Efficiency with IoT
ALPLA, a global leader in packaging solutions, faced several challenges as the complexity of their production machinery increased. The need for highly trained specialists in each factory led to higher personnel costs, difficulties in recruiting experienced talent at each location, and costly personnel turnover. Furthermore, less experienced operators running the machines sub-optimally impacted resource consumption and overall equipment effectiveness (OEE). ALPLA also faced the challenge of monitoring visual inspection systems in every line of their plants, which was almost impossible to do manually. In 2016, ALPLA decided to use data from the 900 different types of embedded sensors in each factory to address these issues. However, their initial choice of SQL Server as the data store for the sensor data proved inadequate, as it was unable to cope with their data requirements.