公司规模
Mid-size Company
地区
- America
国家
- United States
产品
- FORCAM FORCE Shop Floor Management tool
- MTConnect
技术栈
- CNC machining
- Lean Manufacturing methodologies
实施规模
- Enterprise-wide Deployment
影响指标
- Productivity Improvements
- Cost Savings
技术
- 功能应用 - 制造执行系统 (MES)
适用行业
- 金属
- 化学品
适用功能
- 离散制造
- 质量保证
用例
- 自动化制造系统
- 预测性维护
服务
- 系统集成
- 培训
关于客户
Richards Industries is the parent company of six distinct industrial product lines: regulators and control valves from Jordan Valve; sanitary regulators and control valves from Steriflow Valve; ball valves and automated products from Marwin Valve; high pressure - extreme low flow regulators from LowFlow Valve; instrument valves and manifolds from Hex Valve; steam traps and steam specialty equipment from Bestobell Steam Traps. Richards meets customer needs with a wide range of new and proven manufacturing technologies. Complete in-house CNC machining, painting, assembly and testing, along with material traceability and extensive quality procedures assures that Richards Industries products exceed expectations. Key markets include chemical, petrochemical, pharmaceutical and food processing industries. Other sectors include paper products, tire and rubber, machinery and electrical equipment, transportation equipment and energy industries.
挑战
Richards Industries, a parent company of six distinct industrial product lines, has been affected by the decline of crude oil, a key source of energy, which has created opportunities and threats for American manufacturing. The company's business has been slowed by the Oil and Gas reductions but has continuously invested in new product development, process improvements, lead time reduction, on-time shipments and quality. Richards Industries practices Lean Management philosophies for almost two decades. Investment in training and technology is key to retain talent and control cost. The company is dedicated to finding ways to improve manufacturing processes, existing products, creating new products, reaching new markets and responding faster to customers.
解决方案
Richards Industries implemented the FORCAM FORCE Shop Floor Management tool, which included setting up real time machine data collection, web visualization and alerting. This first phase included a 10-machine pilot helping operators to become familiar with the user interface and data in the FORCAM FORCE product suite. Phase 1 was rolled out to the remaining machine park of an additional 21 machines 5 months after the deployment of the pilot in late 2015. Phase 2 facilitated access, editing, and loading of operating instructions and also encouraged the collection of processing information and control of processing quality. Records of tool use can be used to predict tool wear and generate replacement schedules before a substandard part is produced. The potential for boosting productivity lies in networking machines to capture production data for evaluation. MTConnect-based machines are connected to the existing Ethernet network.
运营影响
数量效益
Case Study missing?
Start adding your own!
Register with your work email and create a new case study profile for your business.
相关案例.
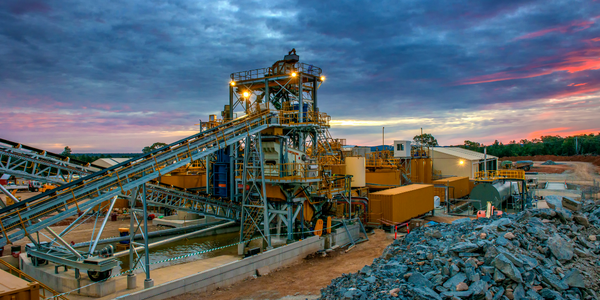
Case Study
Goldcorp: Internet of Things Enables the Mine of the Future
Goldcorp is committed to responsible mining practices and maintaining maximum safety for its workers. At the same time, the firm is constantly exploring ways to improve the efficiency of its operations, extend the life of its assets, and control costs. Goldcorp needed technology that can maximize production efficiency by tracking all mining operations, keep employees safe with remote operations and monitoring of hazardous work areas and control production costs through better asset and site management.

Case Study
KSP Steel Decentralized Control Room
While on-site in Pavlodar, Kazakhstan, the DAQRI team of Business Development and Solutions Architecture personnel worked closely with KSP Steel’s production leadership to understand the steel production process, operational challenges, and worker pain points.
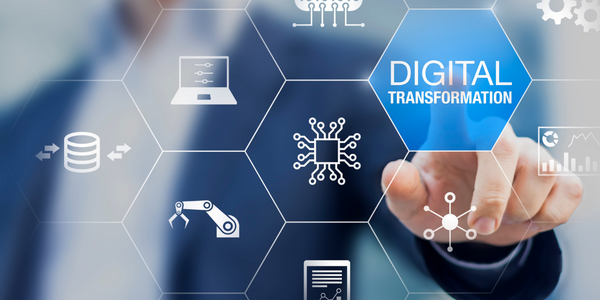
Case Study
Bluescope Steel on Path to Digitally Transform Operations and IT
Increasing competition and fluctuations in the construction market prompted BlueScope Steel to look toward digital transformation of its four businesses, including modern core applications and IT infrastructure. BlueScope needed to modernize its infrastructure and adopt new technologies to improve operations and supply chain efficiency while maintaining and updating an aging application portfolio.
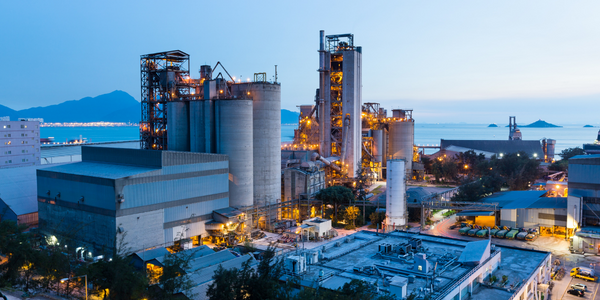
Case Study
Honeywell - Tata Chemicals Improves Data Accessibility with OneWireless
Tata was facing data accessibility challenges in the cement plant control room tapping signals from remote process control areas and other distant locations, including the gas scrubber. Tata needed a wireless solution to extend its control network securely to remote locations that would also provide seamless communication with existing control applications.
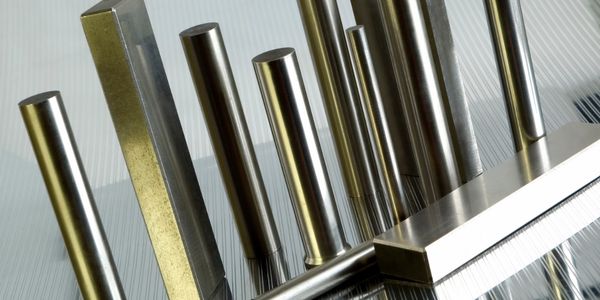
Case Study
RobotStudio Case Study: Benteler Automobiltechnik
Benteler has a small pipe business area for which they produce fuel lines and coolant lines made of aluminum for Porsche and other car manufacturers. One of the problems in production was that when Benteler added new products, production had too much downtime.

Case Study
Advanced Elastomer Systems Upgrades Production
In order to maintain its share of the international market for thermoplastic elastomers AES recently expanded its Florida plant by adding a new production line. While the existing lines were operating satisfactorily using a PROVOX distributed control system with traditional analog I/O, AES wanted advanced technology on the new line for greater economy, efficiency, and reliability. AES officials were anxious to get this line into production to meet incoming orders, but two hurricanes slowed construction.