公司规模
Large Corporate
地区
- Asia
国家
- China
- Hong Kong
- India
- Indonesia
- Korea
- Malaysia
- Philippines
- Singapore
- Taiwan
- Thailand
产品
- QlikView
技术栈
- SAP
- Legacy Systems
- Excel
实施规模
- Enterprise-wide Deployment
影响指标
- Cost Savings
- Productivity Improvements
- Customer Satisfaction
技术
- 分析与建模 - 实时分析
适用行业
- 电子产品
- 零售
适用功能
- 销售与市场营销
- 物流运输
用例
- 库存管理
- 供应链可见性(SCV)
- 实时定位系统 (RTLS)
服务
- 数据科学服务
- 系统集成
关于客户
Established in 1990, FE Global Electronics is one of the leading electronic components distributors in the pan-Asia region, spanning 10 countries (China, Hong Kong, India, Indonesia, Korea, Malaysia, Philippines, Singapore, Taiwan and Thailand) with more than 45 regional offices. The company provides products and value-added services of material management solutions, design and development to customers in information technology, consumer electronics and telecommunications. The business runs at very competitive margins, so cash flow is critical to its success. FE Global has undergone lightningspeed growth, from $5 million in 1991 to $550 million in 2004. It has more than 700 experienced staff worldwide and deals with more than 80 major suppliers and 1,000 active customers.
挑战
FE Global Electronics, a leading electronic components distributor in the pan-Asia region, faced challenges due to its broad distribution coverage and complex web of supplier and customer relationships. The company had trouble getting consistent, timely, and visual information from its legacy systems and other data sources, in addition to its SAP ERP system. This lack of timely and correct information made managing inventory a major headache. The organization faced several problems of increasing and aging inventory, identifying and managing demand and consumption patterns, and managing obsolescence. Managers lacked timely and enough information on receivables aging, which affected cash flow and increased bad debt. Compounding the problem, the company had been unable to get its A/R information in foreign currencies to understand exposure and minimize currency exchange losses.
解决方案
FE Global embarked on a Business Intelligence (BI) initiative to better analyze – and therefore improve – performance. The team looked at the traditional OLAP-based products, but selected QlikView to extract and consolidate data from their various business sources and provide a common view of the various business Key Performance Indicators to their decision makers. QlikView would eliminate this problem through consolidated reporting – extracting data from the sales, financial and inventory modules in the company’s ERP systems, and budgeting and forecasting information from spreadsheets – with easy to understand visual elements like graphs, charts and dashboard gauges. Moreover, the resulting information would be timely enough to provide actionable views of the business. The team developed “proof of concepts” for each functional area to help guide the users along.
运营影响
数量效益
Case Study missing?
Start adding your own!
Register with your work email and create a new case study profile for your business.
相关案例.
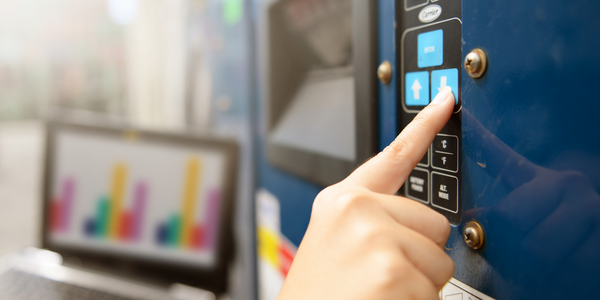
Case Study
Remote Temperature Monitoring of Perishable Goods Saves Money
RMONI was facing temperature monitoring challenges in a cold chain business. A cold chain must be established and maintained to ensure goods have been properly refrigerated during every step of the process, making temperature monitoring a critical business function. Manual registration practice can be very costly, labor intensive and prone to mistakes.
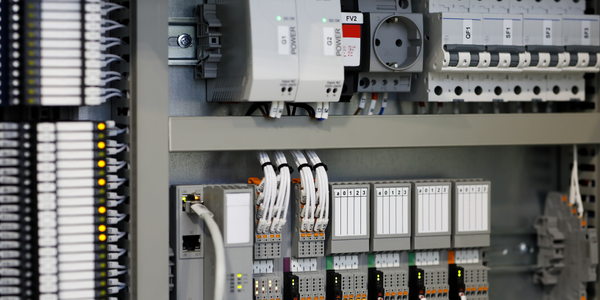
Case Study
Improving Production Line Efficiency with Ethernet Micro RTU Controller
Moxa was asked to provide a connectivity solution for one of the world's leading cosmetics companies. This multinational corporation, with retail presence in 130 countries, 23 global braches, and over 66,000 employees, sought to improve the efficiency of their production process by migrating from manual monitoring to an automatic productivity monitoring system. The production line was being monitored by ABB Real-TPI, a factory information system that offers data collection and analysis to improve plant efficiency. Due to software limitations, the customer needed an OPC server and a corresponding I/O solution to collect data from additional sensor devices for the Real-TPI system. The goal is to enable the factory information system to more thoroughly collect data from every corner of the production line. This will improve its ability to measure Overall Equipment Effectiveness (OEE) and translate into increased production efficiencies. System Requirements • Instant status updates while still consuming minimal bandwidth to relieve strain on limited factory networks • Interoperable with ABB Real-TPI • Small form factor appropriate for deployment where space is scarce • Remote software management and configuration to simplify operations
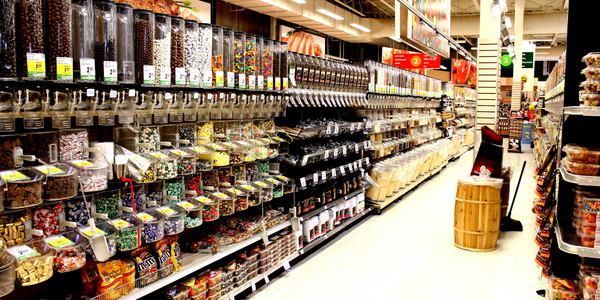
Case Study
How Sirqul’s IoT Platform is Crafting Carrefour’s New In-Store Experiences
Carrefour Taiwan’s goal is to be completely digital by end of 2018. Out-dated manual methods for analysis and assumptions limited Carrefour’s ability to change the customer experience and were void of real-time decision-making capabilities. Rather than relying solely on sales data, assumptions, and disparate systems, Carrefour Taiwan’s CEO led an initiative to find a connected IoT solution that could give the team the ability to make real-time changes and more informed decisions. Prior to implementing, Carrefour struggled to address their conversion rates and did not have the proper insights into the customer decision-making process nor how to make an immediate impact without losing customer confidence.
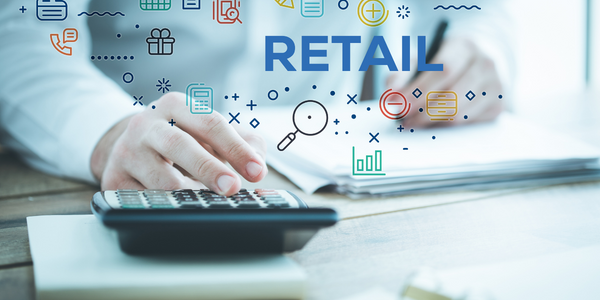
Case Study
Digital Retail Security Solutions
Sennco wanted to help its retail customers increase sales and profits by developing an innovative alarm system as opposed to conventional connected alarms that are permanently tethered to display products. These traditional security systems were cumbersome and intrusive to the customer shopping experience. Additionally, they provided no useful data or analytics.