公司规模
Large Corporate
地区
- Europe
国家
- Finland
产品
- QlikView
- SAP
- SAP BW
技术栈
- Business Intelligence
- Data Analysis
- Data Reporting
实施规模
- Enterprise-wide Deployment
影响指标
- Productivity Improvements
- Customer Satisfaction
技术
- 分析与建模 - 实时分析
- 应用基础设施与中间件 - 数据交换与集成
适用功能
- 销售与市场营销
用例
- 过程控制与优化
- 实时定位系统 (RTLS)
服务
- 数据科学服务
- 系统集成
关于客户
Halton Group is an international group of companies that specializes in developing, manufacturing, and marketing indoor climate products and solutions. The company was founded in Finland in 1969 and has a turnover rate of €100 million per year. Halton operates in 16 countries around the world, including Finland, the United States, the United Kingdom, and many more. The company has more than 800 employees worldwide. Halton's aim was to find a product that promoted self-sufficiency and could be used to peer into its multiple enterprise software applications that manage the company's business areas.
挑战
Halton Group, an international company specializing in indoor climate products, was facing challenges in managing its worldwide growth. The company's existing enterprise software systems were unable to deliver the types of reports and analysis needed to proactively manage day-to-day business operations. The business warehouse module connected to one of its enterprise resource planning (ERP) systems was complex to operate and provided a limited number of reports. Halton needed a solution that promoted self-sufficiency and did not require programming or any extensive set-up to create and run reports. The company also needed a product that could integrate with its multiple enterprise software applications to centralize and standardize its reporting processes and improve supply chain efficiency and customer service.
解决方案
Halton Group chose to implement QlikView, a business intelligence tool, to address its challenges. The solution was deployed to 75 employees in less than a week. With QlikView across seven functional areas, Halton now analyzes customer profitability, sales trends, operations, and CRM performance – all focused on driving corporate profitability. QlikView Server supports security and visibility while handling a large data volume. Through QlikView Connector, Halton immediately leveraged the invaluable data that was locked in SAP BW to achieve a real-time view of operational performance. The company now has the ability to keep track of all financial and operational status by creating seamless reports on sales trends, profitability margins, customer activity, and more.
运营影响
数量效益
Case Study missing?
Start adding your own!
Register with your work email and create a new case study profile for your business.
相关案例.
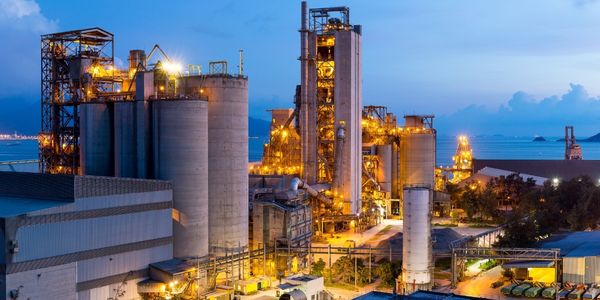
Case Study
System 800xA at Indian Cement Plants
Chettinad Cement recognized that further efficiencies could be achieved in its cement manufacturing process. It looked to investing in comprehensive operational and control technologies to manage and derive productivity and energy efficiency gains from the assets on Line 2, their second plant in India.
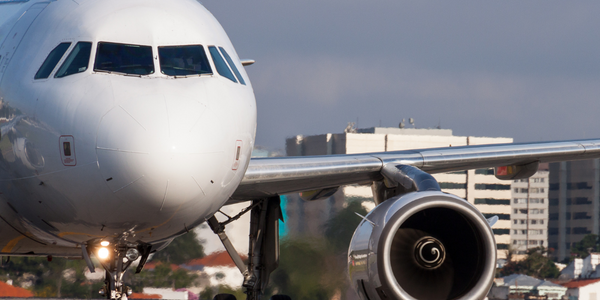
Case Study
Airbus Soars with Wearable Technology
Building an Airbus aircraft involves complex manufacturing processes consisting of thousands of moving parts. Speed and accuracy are critical to business and competitive advantage. Improvements in both would have high impact on Airbus’ bottom line. Airbus wanted to help operators reduce the complexity of assembling cabin seats and decrease the time required to complete this task.
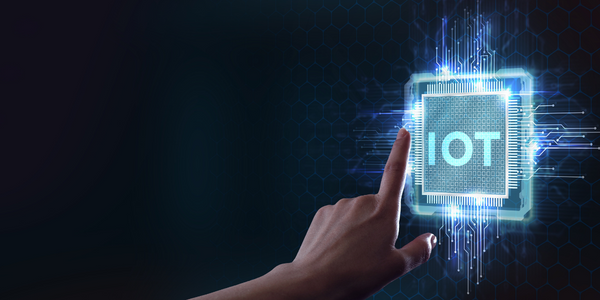
Case Study
Leading Tools Manufacturer Transforms Operations with IoT
Stanley Black & Decker required transparency of real-time overall equipment effectiveness and line productivity to reduce production line change over time.The goal was to to improve production to schedule, reduce actual labor costs and understanding the effects of shift changes and resource shifts from line to line.
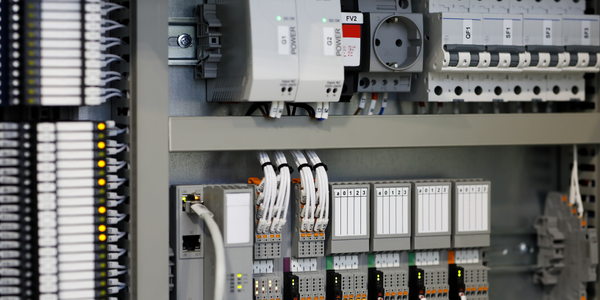
Case Study
Improving Production Line Efficiency with Ethernet Micro RTU Controller
Moxa was asked to provide a connectivity solution for one of the world's leading cosmetics companies. This multinational corporation, with retail presence in 130 countries, 23 global braches, and over 66,000 employees, sought to improve the efficiency of their production process by migrating from manual monitoring to an automatic productivity monitoring system. The production line was being monitored by ABB Real-TPI, a factory information system that offers data collection and analysis to improve plant efficiency. Due to software limitations, the customer needed an OPC server and a corresponding I/O solution to collect data from additional sensor devices for the Real-TPI system. The goal is to enable the factory information system to more thoroughly collect data from every corner of the production line. This will improve its ability to measure Overall Equipment Effectiveness (OEE) and translate into increased production efficiencies. System Requirements • Instant status updates while still consuming minimal bandwidth to relieve strain on limited factory networks • Interoperable with ABB Real-TPI • Small form factor appropriate for deployment where space is scarce • Remote software management and configuration to simplify operations