How Metso implemented Service Parts Management (SPM) in the Cloud to unearth value from its global supply chain
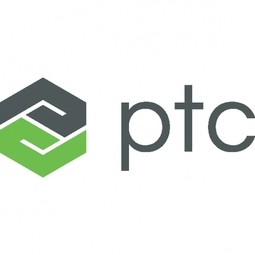
公司规模
Large Corporate
地区
- Europe
国家
- Finland
产品
- PTC’s Service Parts Management (SPM)
- Multi Echelon Optimization
- PTC Cloud Services
技术栈
- Cloud Computing
- ERP Integration
- Inventory Management System
实施规模
- Enterprise-wide Deployment
影响指标
- Cost Savings
- Productivity Improvements
技术
- 平台即服务 (PaaS) - 数据管理平台
- 基础设施即服务 (IaaS) - 云计算
适用行业
- 矿业
- 石油和天然气
- 回收与废物管理
适用功能
- 物流运输
- 采购
用例
- 供应链可见性(SCV)
- 库存管理
- 需求计划与预测
服务
- 云规划/设计/实施服务
- 系统集成
关于客户
Metso is a world-leading industrial company serving the mining, aggregates, recycling, oil, gas, pulp, paper, and process industries. The company is headquartered in Helsinki, Finland, and reported net sales of EUR 2.6 billion in 2016. Metso operates a global network of over 80 service centers, services professionals, and employs over 11,000 people in more than 50 countries. The company's operations are spread across 39 locations, each of which used a global inventory management system. However, the inventory at each location was managed independently and isolated from the inventory in the entire Metso supply chain.
挑战
Metso, a world-leading industrial company, was facing challenges with its global supply chain. The company was using a location-based, on-shelf availability model, which resulted in isolated and independently managed inventories across its 39 locations. This approach was inefficient and reduced Metso's ability to serve its customers effectively. The company also had to manage intricate material flows, making it difficult to predict part lead time. Furthermore, the constraints of a legacy system and a focus on individual supply issues rather than broader strategic improvements were hindering Metso's growth and profitability. The company needed a solution that could match its complicated network and grow with its business.
解决方案
Metso adopted PTC’s Service Parts Management (SPM) with Multi Echelon Optimization to manage its global supply chain more efficiently. The solution allowed Metso to move from a location-based planning to planning the supply chain as a whole. The implementation of SPM started with a pilot phase in June 2014. During the initial months, Metso's cost of inventory increased as the system evaluated product mix and procured the optimal inventory levels. However, once the right parts were procured in the right locations, inventory stopped increasing and started to go down. The design, build, and implementation of the project took place over nine months, with a highly focused project team dedicated to the launch. Much of the team’s focus was on change management and master data as the go-live would be simultaneous in all the 39 locations. SPM was integrated into Metso's global SAP, improving efficiency.
运营影响
数量效益
Case Study missing?
Start adding your own!
Register with your work email and create a new case study profile for your business.
相关案例.
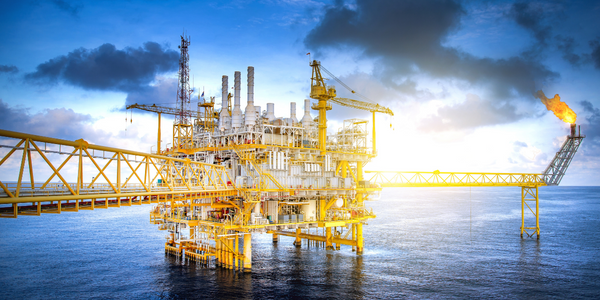
Case Study
Taking Oil and Gas Exploration to the Next Level
DownUnder GeoSolutions (DUG) wanted to increase computing performance by 5 to 10 times to improve seismic processing. The solution must build on current architecture software investments without sacrificing existing software and scale computing without scaling IT infrastructure costs.
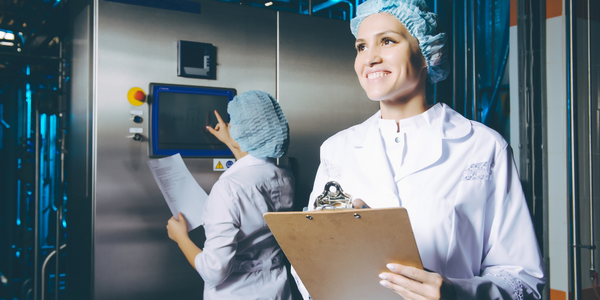
Case Study
Remote Wellhead Monitoring
Each wellhead was equipped with various sensors and meters that needed to be monitored and controlled from a central HMI, often miles away from the assets in the field. Redundant solar and wind generators were installed at each wellhead to support the electrical needs of the pumpstations, temperature meters, cameras, and cellular modules. In addition to asset management and remote control capabilities, data logging for remote surveillance and alarm notifications was a key demand from the customer. Terra Ferma’s solution needed to be power efficient, reliable, and capable of supporting high-bandwidth data-feeds. They needed a multi-link cellular connection to a central server that sustained reliable and redundant monitoring and control of flow meters, temperature sensors, power supply, and event-logging; including video and image files. This open-standard network needed to interface with the existing SCADA and proprietary network management software.
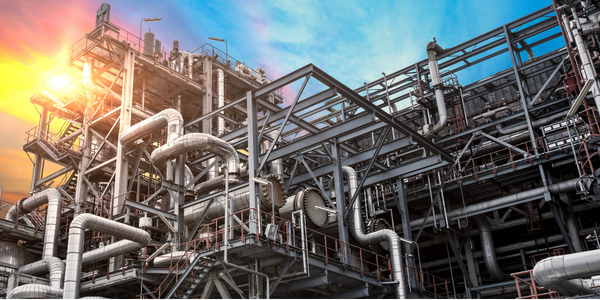
Case Study
Refinery Saves Over $700,000 with Smart Wireless
One of the largest petroleum refineries in the world is equipped to refine various types of crude oil and manufacture various grades of fuel from motor gasoline to Aviation Turbine Fuel. Due to wear and tear, eight hydrogen valves in each refinery were leaking, and each cost $1800 per ton of hydrogen vented. The plant also had leakage on nearly 30 flare control hydrocarbon valves. The refinery wanted a continuous, online monitoring system that could catch leaks early, minimize hydrogen and hydrocarbon production losses, and improve safety for maintenance.