公司规模
Large Corporate
地区
- Europe
国家
- Sweden
产品
- QlikView
- IFS ERP system
技术栈
- Data Analysis
- ERP
实施规模
- Enterprise-wide Deployment
影响指标
- Cost Savings
- Productivity Improvements
技术
- 分析与建模 - 实时分析
适用功能
- 人力资源
用例
- 供应链可见性(SCV)
服务
- 数据科学服务
关于客户
Nacka Municipality is a government entity located east of Stockholm, Sweden. It is home to approximately 78,000 inhabitants. The municipality's vision is based on openness and multitude, encouraging development and renewal, effective use of resources, and freedom of choice. Through delegating responsibilities, the municipality takes advantage of the skills and capabilities of its employees and listens attentively to its citizens. A few years ago, Nacka Municipality decided to update its ERP system to something more modern and selected IFS as its ERP solution.
挑战
Nacka Municipality, a government entity located east of Stockholm, Sweden, was facing several challenges. The municipality was grappling with high costs associated with purchasing standards noncompliance, which was difficult to police. Controllers were spending too much time on manual data collection and analysis. The IT staff was also burdened with the task of generating ad-hoc reports from the IFS ERP system. The municipality needed a solution that could help them analyze the data within their ERP system and provide detailed, timely follow-up capability.
解决方案
Nacka Municipality deployed QlikView to more than 250 employees across 3 functional areas. With QlikView pulling data from an IFS ERP system, Nacka Municipality analyzes employee purchasing, supplier pricing and budget execution – all with a focus on keeping costs low for the organization. With QlikView Server (64-bit) and Publisher, Nacka Municipality can effectively manage security and visibility requirements while handling massive amounts of data. QlikView enabled Nacka to make mainframe calculations in a Windows environment without complicated data storage. QlikView solves financial control problems by performing detailed analysis of individual invoices in real-time. Now, users simply have to click on the information they require and it is shown down to the individual invoicing level.
运营影响
数量效益
Case Study missing?
Start adding your own!
Register with your work email and create a new case study profile for your business.
相关案例.
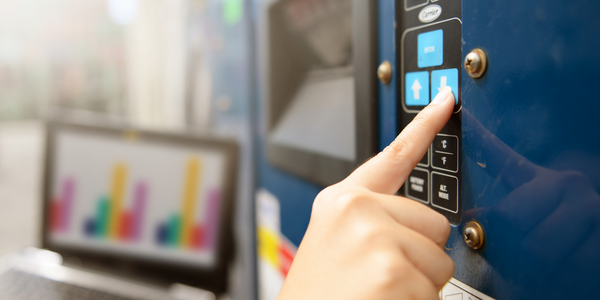
Case Study
Remote Temperature Monitoring of Perishable Goods Saves Money
RMONI was facing temperature monitoring challenges in a cold chain business. A cold chain must be established and maintained to ensure goods have been properly refrigerated during every step of the process, making temperature monitoring a critical business function. Manual registration practice can be very costly, labor intensive and prone to mistakes.
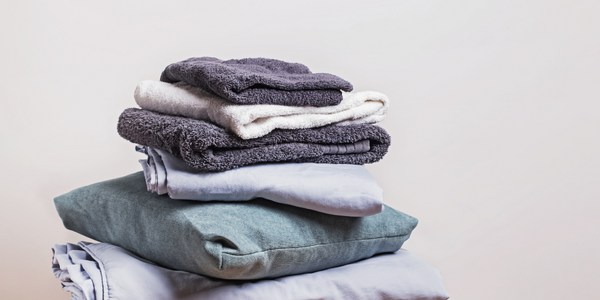
Case Study
Retail Uses RFID to Enable Cold Chain Monitoring
Like most grocery retailers, Hy-Vee is faced with the challenge of providing the highest quality products to its shoppers. Shoppers want the longest possible shelf life from perishable products and expect a consistent product experience each time they shop. Controlling the quality of products sold leads to shopper loyalty, which is of paramount importance to the success of Hy-Vee. Before products arrive in stores, Hy-Vee's distribution centers (DCs) handle items including dairy products, fresh meats, seafood, deli items, produce and frozen goods, all of which have different temperature needs and sensitivities. During transit from suppliers to DCs, Hy-Vee has limited visibility and temperature management abilities due to large amount of supplier managed transportation. For instance, during a week-long transit, a supplier's carrier equipment may malfunction, causing an item to thaw and then refreeze once repairs are made. Hy-Vee sought help from TempTRIP, an RFID solution provider that focuses on shipping, storage, receiving, and temperature control. TempTRIP's EPC RFID tags use Impinj chips to monitor and report temperature readings throughout the shipping and receiving process. The tags can also be re-configured and re-used, a unique feature within the current market of temperature monitoring devices.
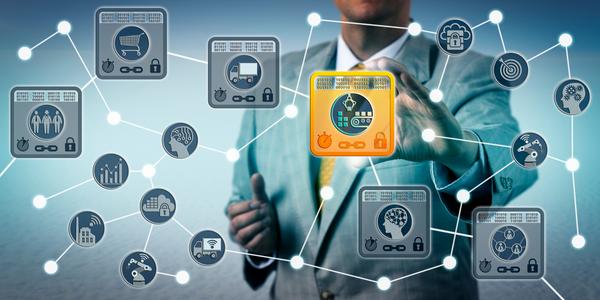
Case Study
Covisint Improves Mitsubishi's Collaboration With Its Supply Chain
Mitsubishi sought to improve supplier relationships on a global basis and to offer an easy-to-use solution to interact with them. In August 2004, Mitsubishi selected Covisint’s platform to help improve sharing of information and collaborative business processes with its global suppliers. Covisint enabled Mitsubishi to provide its suppliers with immediate access to information and applications to obtain more collaborative working relationships