技术
- 分析与建模 - 数字孪生/模拟
- 传感器 - 触觉传感器
适用行业
- 矿业
- 铁路与地铁
适用功能
- 物流运输
- 产品研发
用例
- 数字孪生
- 虚拟现实
关于客户
Electro-Motive Diesel (EMD) 是全球最大的柴电机车供应商,其产品适用于各种商业铁路应用,包括货运、城际客运、通勤、换乘、工业和采矿。自 1930 年代初以来,EMD 已为超过 73 个国家的客户生产了 58,000 多辆机车。 EMD 也是船舶推进、海上和陆上油井钻机以及固定发电用柴油动力发动机的全球供应商。该公司的总部、工程和零部件制造工厂位于伊利诺伊州拉格兰奇,总装位于安大略省伦敦。该公司的主要新产品之一是SD70ACe机车,该机车采用交流驱动系统,可提供157,000磅的连续牵引力,用于牵引重型货运列车以及高速联运列车。
挑战
Electro-Motive Diesel (EMD) 是全球最大的柴电机车供应商,面临着开发 SD70ACe 机车的压力,该机车满足性能、可靠性、燃油经济性、耐撞性和操作员舒适度的高标准。这些机车预计能够在恶劣条件下经济、安全地运行数十年,并且停机时间最短。经受重复疲劳循环的部件的耐用性是一个主要问题,因为大多数设备在前六年的运行中行驶了超过 100 万英里,使用寿命接近 30 年,一些主要部件的使用寿命超过 50 年。由于在如此大型、复杂的机器上运行物理测试相关的大量时间和成本因素,在缩短开发周期的同时实现这些目标尤其具有挑战性。
解决方案
EMD 通过在从开发概念阶段到整个设计过程中融入工程仿真来应对这些挑战。使用仿真作为验证和验证工具有助于 EMD 最大限度地减少物理测试、缩短开发时间并优化 SD70ACe 的结构特性。 ANSYS Mechanical 软件是该仿真策略的关键要素。结构分析用于评估部件的应力、挠度和谐波,指导设计人员在开发早期塑造零件的基本形状和拓扑。该软件还用于悬架动力学、驾驶室和其他子系统的隔振安装的详细分析,以及机车柴油机曲轴箱、气缸盖、活塞杆和其他往复运动部件的开发。
运营影响
Case Study missing?
Start adding your own!
Register with your work email and create a new case study profile for your business.
相关案例.
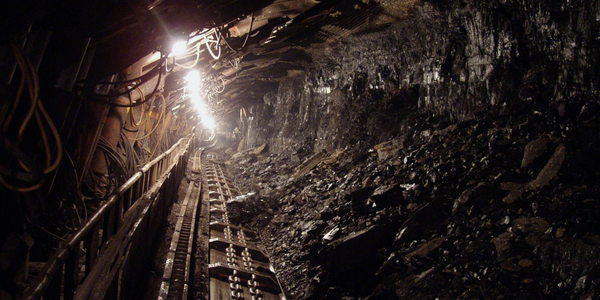
Case Study
Underground Mining Safety
The goal was to produce a safety system to monitor and support underground mining operations; existing systems were either too simple (i.e. phone line) or overly complex and expensive, inhibiting deployment, and providing little-to-no support in event of an accident. Given the dangerous nature of the mining work environment and the strict regulations placed on the industry, the solution would have to comply with Mine Safety and Health Administration (MSHA) regulations. Yet the product needed to allow for simple deployment to truly be a groundbreaking solution - increasing miner safety and changing daily operations for the better.
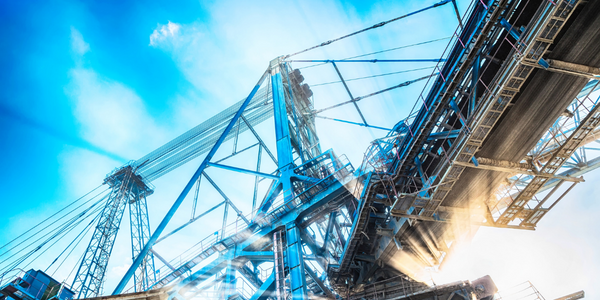
Case Study
Mining Firm Quadruples Production, with Internet of Everything
Dundee Precious Metal’s flagship mine, in Chelopech, Bulgaria, produces a gold, copper, and silver concentrate set a goal to increase production by 30%. Dundee wanted to increase production quality and output without increasing headcount and resources, improve miner safety, and minimize cost.
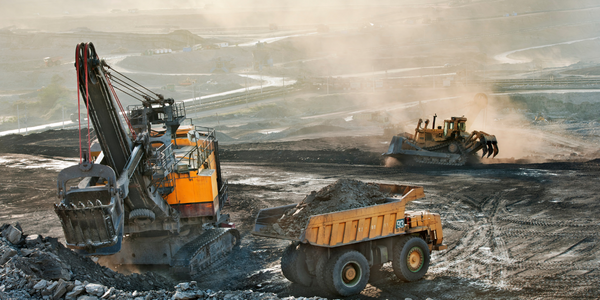
Case Study
Fastenal Builds the Future of Manufacturing with MachineMetrics
Fastenal's objective was to better understand their machine downtime, utilization, quality issues, and to embrace cutting-edge manufacturing technology/process improvement capabilities to bring their team to the next level. However, there was a lack of real-time data, visualization, and actionable insights made this transition impossible.
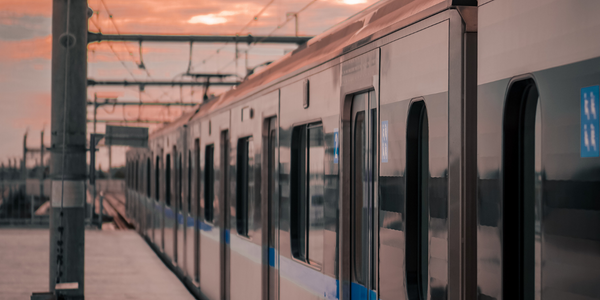
Case Study
Building Smart IoT-Connected Railways
• Difficult environment. Communications equipment on trains must function properly in harsh conditions, such as environment temperatures ranging from -25°C to +85°C, according to the EU standard EN50155.• Railway regulations. All products in a train must adhere to strict standards, relating to working vibration, power consumption, and lifetime.• Lengthy process. Time to market in the railway industry can take years from concept to mass production, so product design requires a solid long term vision.
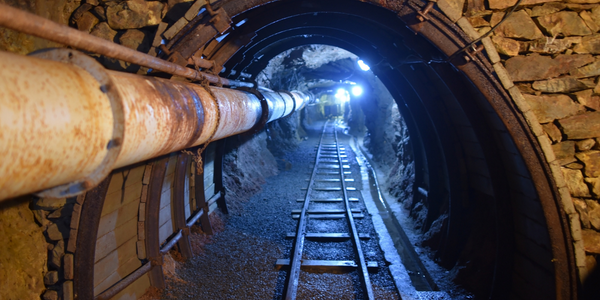
Case Study
Joy Mining Systems
Joy equipment faces many challenges. The first is machine integration and control. The business end of the machine has a rapidly-spinning cylinder with 6-inch diamond-studded cutting teeth. It chews through rock at rates measured in tens of tons per minute. The system grinds through the rock in front, creating a rectangular mine tunnel. Hydraulic lifters support the ceiling as the machine moves forward. Automated drills and screws drive 3-ft long screws into the ceiling to stabilize it. The rock and coal fall into a set of gathering "fingers" below the cutting cylinder. These fingers scoop up the rock and coal and deposit it onto a conveyor belt. The conveyor passes under the machine and out the back. A train of conveyor belt cars, up to a mile long, follows the cutter into the mine. The rock shoots along this train at over 400 feet per minute until it empties into rail cars at the end. Current systems place an operator cage next to the cutter. Choking dust (potentially explosive), the risk of collapse and the proximity of metal and rock mayhem make the operator cage a hazardous location.
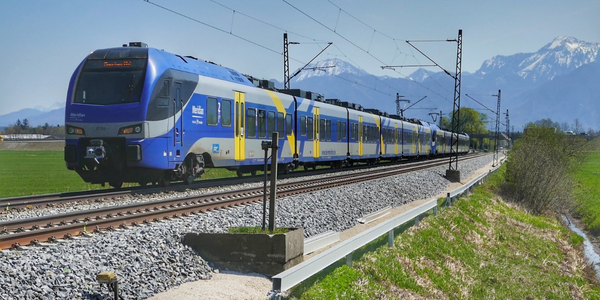
Case Study
Connected Transportation: A Smarter Brain for Your Train with Intel
A modern locomotive, for example, has as many as 200 sensors generating more than a billion data points per second. Vibration sensors surround critical components, video cameras scan the track and cab, while other sensors monitor RPM, power, temperature, the fuel mix, exhaust characteristics, and more.Most of today’s locomotives lack sufficient on-board processing power to make full use of all this data. To make matters worse, the data from different subsystems, such as the brakes, fuel system, and engine, remain separate, stored in isolated “boxes” that prevent unified analysis. The data is available, but the technology needed to process it in the most effective manner is not. As new sensors are added to the machine, the problem escalates.