技术
- 功能应用 - 企业资源规划系统 (ERP)
- 功能应用 - 制造执行系统 (MES)
用例
- 添加剂制造
- 制造过程模拟
关于客户
应用物理技术公司 (APTech) 是显微镜和 3D 打印机用热离子和场发射阴极设计和制造领域的世界领先者。该公司的客户包括 Themo Fisher Scientific 及其母公司日立公司。 APTech 之前运行 Sage ERP 和 IQMS 作为其 MRP,但由于冗余、数据重复录入和高错误率而面临挑战。该公司需要一个现代化的综合系统来简化其运营并支持其发展。
挑战
应用物理技术公司 (APTech) 是显微镜和 3D 打印机用热离子和场发射阴极设计和制造的全球领导者,一直在努力解决过时、不受支持和断开连接的系统。该公司使用 Sage ERP 和 IQMS 作为其 MRP,这导致了冗余、数据重复录入和高错误率。 APTech 认识到需要一个更现代化、更全面的系统,不仅可以简化其运营,还可以随着其增长而扩展。我们面临的挑战是找到一种用户友好、可扩展且可以将所有流程集成到单个平台中的解决方案。
解决方案
在评估了各种 ERP 系统后,APTech 选择了 OptiProERP 和 SAP Business One。该决定受到产品的易用性、现代技术、可扩展性和制造功能的影响。 OptiProERP 作为一家拥有丰富知识、经验和最佳实践的老牌供应商,提供了可以支持 APTech 未来发展的解决方案。 OptiProERP 的实施帮助 APTech 简化了流程、节省了时间,并在公司不断扩张的过程中保持了清晰的员工分工和新角色。该解决方案还使该公司能够优化其运营,从而更容易涉足新产品线。
运营影响
数量效益
Case Study missing?
Start adding your own!
Register with your work email and create a new case study profile for your business.
相关案例.
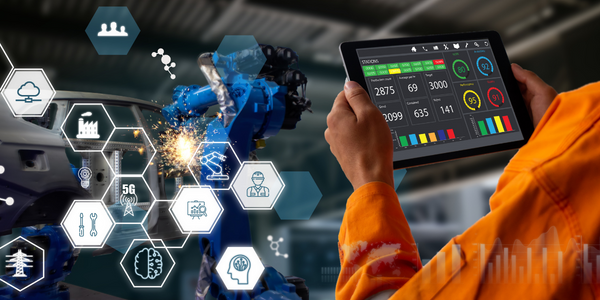
Case Study
Battery manufacturer Industrial Digital Twin
For optimum control of product quality, Banner relies on a high production depth. Its 560 production employees produce nearly all the components in¬-house that they need to make finished batteries on Banner’s six assembly lines. This includes the plastic parts for the battery cases as well as the paste-filled lead oxide grids. Their production involves two to five¬ days rest in maturing chambers to create optimum current absorption and storage capacity. Banner’s ongoing success was accompanied by a continuous, organic growth of the production facilities, adding or extending hall after hall until the complex filled the site that had seemed ever so spacious when the company moved here from a smaller place in 1959. These developments led to a heterogeneous production environment. “This confronts us with significant challenges, particularly concerning intra¬logistics issues, such as scheduling for the maturing chambers,” says Franz Dorninger, technical director at Banner. “We contemplated various ways to overcome this problem, including relocating to new premises.”
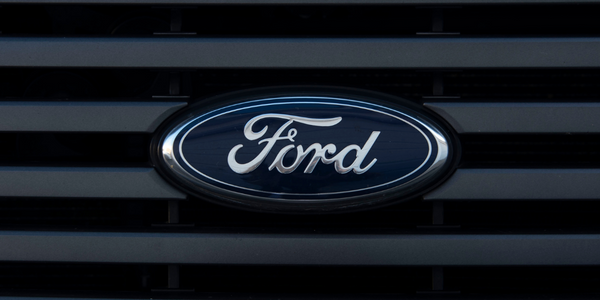
Case Study
Ford Motor Company on the Road to 3D Manufacturing
To date, key challenges have stood in the way of 3D printing becoming a manufacturing tool for the automaker. The first issue is a fundamental one — conventional 3D printing technologies make parts layer-by-layer, slowly crafting one layer at a time, creating parts that aren’t nearly as robust as those stamped or injection molded. While the slow speed of this process is a major drawback, the bigger problem is that the parts produced are not isotropic and not durable enough to be used in production vehicles. In addition, most parts used in vehicles today must withstand temperature extremes from the hottest desert to the coldest Arctic environments and still maintain their integrity. With only a handful of stock materials available for 3D printers, meeting the automaker’s unique demands has not been possible.
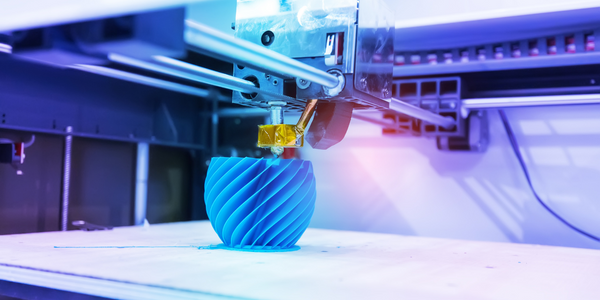
Case Study
3D Printed Prototypes Streamline Equipment Introduction
Vauxhall set out to introduce a modified process hanger with a new part that would be used to support each vehicle body throughout the production process. This part is a critical piece and had to perfectly fit both the machinery and the auto body to create correct clearances and avoid damage during production.
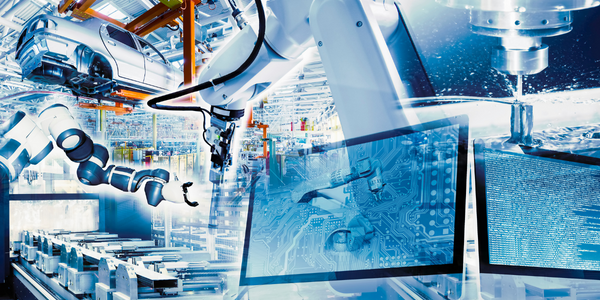
Case Study
Bekaert's Journey to Manufacturing Digitalization with TCS
Bekaert, a major player in the steel wire industry, was facing significant challenges in its manufacturing operations due to outdated data platforms. The company was unable to trace genealogy beyond a week's data and lacked diagnostic analysis of plant operations, which severely hampered decision-making. The absence of automation in benchmarking operations and extensive reporting on plant management further complicated the situation. To enhance efficiency and effectiveness in multiple focus areas, Bekaert needed a modern data platform capable of managing large volumes of data and generating actionable insights. The company aimed to drive quality, overall equipment effectiveness (OEE), and plant productivity based on these insights.
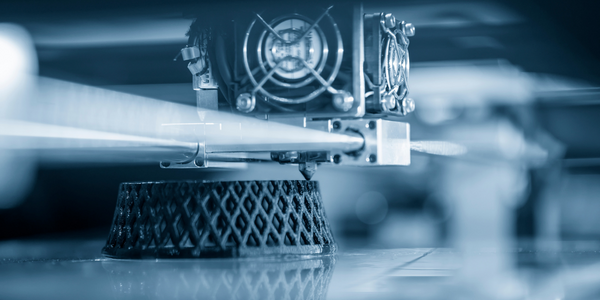
Case Study
3D-Printing of Tooling Parts
Selective Laser Melting (SLM), an additive manufacturing technology, can be used for the production of tooling components with conformal cooling channels. ABB OY, Drives and Controls, was able to tremendously reduce the cycle time for a cabling grommet due to a redesign and optimization of a tooling insert. The optimized geometry of the part not only reduces the cycle time but also leads to less scrap parts in production.The aim of the case study of implementing conformal cooling for this insert was to improve the efficiency of the production and to increase the product quality resulting in less defective products.