技术
- 分析与建模 - 实时分析
- 网络与连接 - 5G
适用行业
- 食品与饮料
- 零售
适用功能
- 采购
用例
- 减废预测
- 零售店自动化
服务
- 系统集成
关于客户
餐馆、杂货店、面包店、餐饮承办商、酒店和其他零售商可以将未售出的食物以大幅折扣捆绑在一个主题“篮子”中,其中包括农产品、糕点、熟食或其他接近保质期的物品。商家会发布当天有哪些商品,顾客可以立即看到附近有哪些商品在售。然后,通过 Phoenix 应用程序,他们只需预订、付款并提醒商店他们正在上门取货。
挑战
Phoenix 的使命是减少各种浪费。这家总部位于法国的初创公司帮助未售出食品的零售商与重视可持续发展和物美价廉的顾客建立联系。自推出以来,已有超过 5000 万份本来会被丢弃的餐食被超过 40 万顾客享用。
解决方案
Phenix 使用 Twilio 可编程 SMS 和 Twilio SendGrid 电子邮件 API 来运行数以万计的日常交互。实时通信是 Phoenix 模型的核心,并且全部由 Twilio 提供支持。使用可编程 SMS 使 Phoenix 团队能够以快速且经济高效的方式启动移动应用程序。使用 Twilio SendGrid 的电子邮件 API 实时发送交易电子邮件。 SendGrid 中提供的自定义触发器使 Phoenix 能够设置多个交易电子邮件序列,从而使卖家和客户无缝地完成实时购买和提货流程。
运营影响
数量效益
Case Study missing?
Start adding your own!
Register with your work email and create a new case study profile for your business.
相关案例.
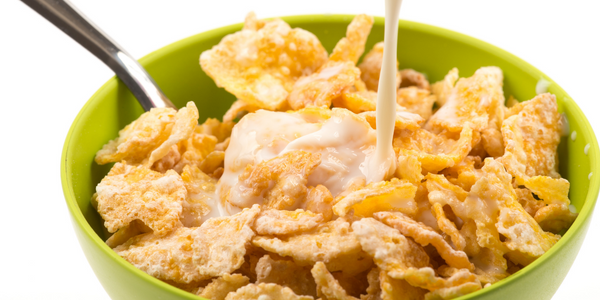
Case Study
The Kellogg Company
Kellogg keeps a close eye on its trade spend, analyzing large volumes of data and running complex simulations to predict which promotional activities will be the most effective. Kellogg needed to decrease the trade spend but its traditional relational database on premises could not keep up with the pace of demand.
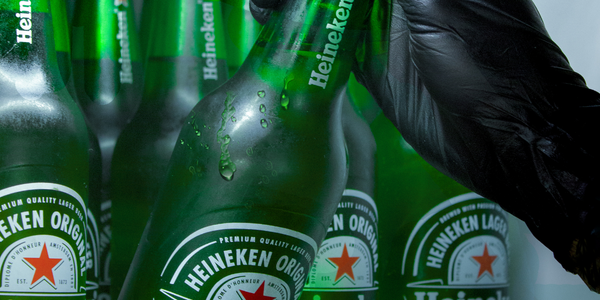
Case Study
HEINEKEN Uses the Cloud to Reach 10.5 Million Consumers
For 2012 campaign, the Bond promotion, it planned to launch the campaign at the same time everywhere on the planet. That created unprecedented challenges for HEINEKEN—nowhere more so than in its technology operation. The primary digital content for the campaign was a 100-megabyte movie that had to play flawlessly for millions of viewers worldwide. After all, Bond never fails. No one was going to tolerate a technology failure that might bruise his brand.Previously, HEINEKEN had supported digital media at its outsourced datacenter. But that datacenter lacked the computing resources HEINEKEN needed, and building them—especially to support peak traffic that would total millions of simultaneous hits—would have been both time-consuming and expensive. Nor would it have provided the geographic reach that HEINEKEN needed to minimize latency worldwide.
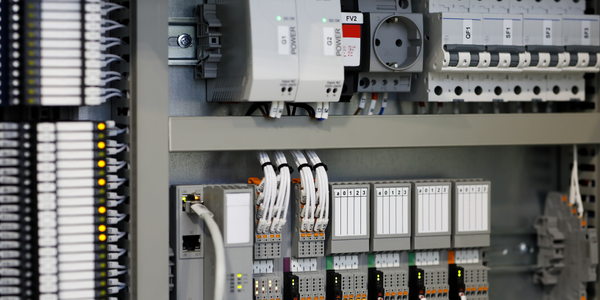
Case Study
Improving Production Line Efficiency with Ethernet Micro RTU Controller
Moxa was asked to provide a connectivity solution for one of the world's leading cosmetics companies. This multinational corporation, with retail presence in 130 countries, 23 global braches, and over 66,000 employees, sought to improve the efficiency of their production process by migrating from manual monitoring to an automatic productivity monitoring system. The production line was being monitored by ABB Real-TPI, a factory information system that offers data collection and analysis to improve plant efficiency. Due to software limitations, the customer needed an OPC server and a corresponding I/O solution to collect data from additional sensor devices for the Real-TPI system. The goal is to enable the factory information system to more thoroughly collect data from every corner of the production line. This will improve its ability to measure Overall Equipment Effectiveness (OEE) and translate into increased production efficiencies. System Requirements • Instant status updates while still consuming minimal bandwidth to relieve strain on limited factory networks • Interoperable with ABB Real-TPI • Small form factor appropriate for deployment where space is scarce • Remote software management and configuration to simplify operations
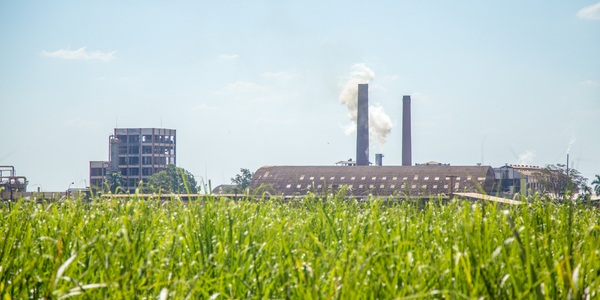
Case Study
Energy Management System at Sugar Industry
The company wanted to use the information from the system to claim under the renewable energy certificate scheme. The benefit to the company under the renewable energy certificates is Rs 75 million a year. To enable the above, an end-to-end solution for load monitoring, consumption monitoring, online data monitoring, automatic meter data acquisition which can be exported to SAP and other applications is required.
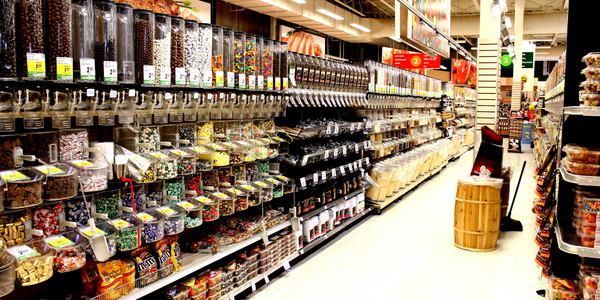
Case Study
How Sirqul’s IoT Platform is Crafting Carrefour’s New In-Store Experiences
Carrefour Taiwan’s goal is to be completely digital by end of 2018. Out-dated manual methods for analysis and assumptions limited Carrefour’s ability to change the customer experience and were void of real-time decision-making capabilities. Rather than relying solely on sales data, assumptions, and disparate systems, Carrefour Taiwan’s CEO led an initiative to find a connected IoT solution that could give the team the ability to make real-time changes and more informed decisions. Prior to implementing, Carrefour struggled to address their conversion rates and did not have the proper insights into the customer decision-making process nor how to make an immediate impact without losing customer confidence.