公司规模
Large Corporate
地区
- Europe
国家
- Denmark
产品
- Brüel & Kjær Type 4134 condenser microphone
- Brüel & Kjær condenser microphones
- Brüel & Kjær vibration transducers
技术栈
- Multiphysics simulation
- Mechanical modeling
- Electrical signal generation
- Thermal and viscous acoustic loss modeling
实施规模
- Enterprise-wide Deployment
影响指标
- Productivity Improvements
- Innovation Output
- Customer Satisfaction
技术
- 分析与建模 - 预测分析
- 分析与建模 - 数字孪生/模拟
适用行业
- 汽车
- 航天
- 消费品
适用功能
- 产品研发
- 质量保证
用例
- 预测性维护
- 机器状态监测
服务
- 系统集成
- 软件设计与工程服务
- 测试与认证
关于客户
Brüel & Kjær A/S is a leading company in the field of sound and vibration measurement and analysis, with over 40 years of experience. Their customer base includes prominent names such as Airbus, Boeing, Ferrari, Bosch, Honeywell, Caterpillar, Ford, Toyota, Volvo, Rolls-Royce, Lockheed Martin, and NASA. The company specializes in developing and producing condenser microphones and vibration transducers that cover a wide range of frequencies and sound levels. Brüel & Kjær's products are used in various industries to address sound and vibration challenges, ensuring high precision and accuracy in measurements.
挑战
The challenge for Brüel & Kjær is to design industrial and measurement-grade microphones and transducers with a known and consistent error range, even over extended periods. The company must meet diverse industry sound and vibration challenges, from traffic and airport noise to car engine vibration, wind turbine noise, and production quality control. This requires designing microphones and accelerometers that adhere to various measurement standards. The goal is to achieve high precision and accuracy in their devices, which is critical for their customers, including major companies like Airbus, Boeing, Ferrari, Bosch, and NASA.
解决方案
Brüel & Kjær employs simulation as a core part of their R&D process to design and test their microphones and transducers. For microphones, they use multiphysics models to analyze the movement of the diaphragm, electromechanical interactions, resonance frequency, and thermal and viscous acoustic losses. This detailed modeling helps predict interactions between the backplate and diaphragm, influencing the microphone's directional characteristics. Simulations also allow them to test different vent configurations for low-frequency sounds, enabling the exploration of new designs and device limits. For vibration transducers, simulation helps design devices that avoid resonance frequencies within the typical range of 10 to 1000 Hz. Mechanical filters are used to cut away undesired signals caused by transducer resonance. This approach allows Brüel & Kjær to quickly and efficiently test new design solutions for various operating scenarios, bringing them closer to achieving high precision and accuracy in their products.
运营影响
Case Study missing?
Start adding your own!
Register with your work email and create a new case study profile for your business.
相关案例.
.png)
Case Study
Improving Vending Machine Profitability with the Internet of Things (IoT)
The vending industry is undergoing a sea change, taking advantage of new technologies to go beyond just delivering snacks to creating a new retail location. Intelligent vending machines can be found in many public locations as well as company facilities, selling different types of goods and services, including even computer accessories, gold bars, tickets, and office supplies. With increasing sophistication, they may also provide time- and location-based data pertaining to sales, inventory, and customer preferences. But at the end of the day, vending machine operators know greater profitability is driven by higher sales and lower operating costs.
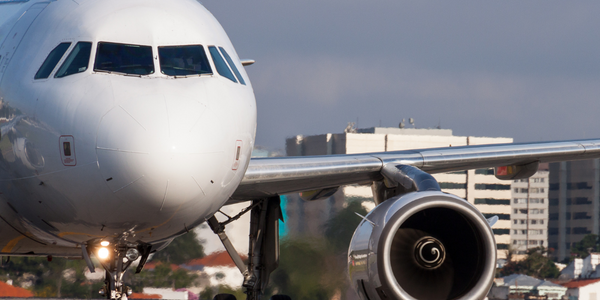
Case Study
Airbus Soars with Wearable Technology
Building an Airbus aircraft involves complex manufacturing processes consisting of thousands of moving parts. Speed and accuracy are critical to business and competitive advantage. Improvements in both would have high impact on Airbus’ bottom line. Airbus wanted to help operators reduce the complexity of assembling cabin seats and decrease the time required to complete this task.
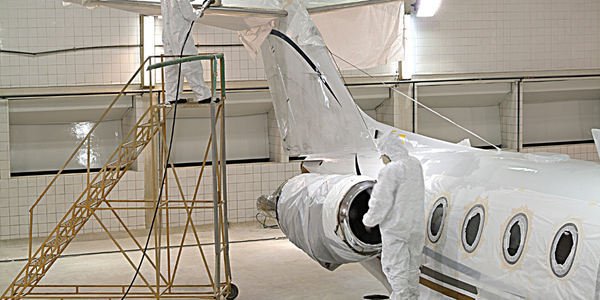
Case Study
Aircraft Predictive Maintenance and Workflow Optimization
First, aircraft manufacturer have trouble monitoring the health of aircraft systems with health prognostics and deliver predictive maintenance insights. Second, aircraft manufacturer wants a solution that can provide an in-context advisory and align job assignments to match technician experience and expertise.
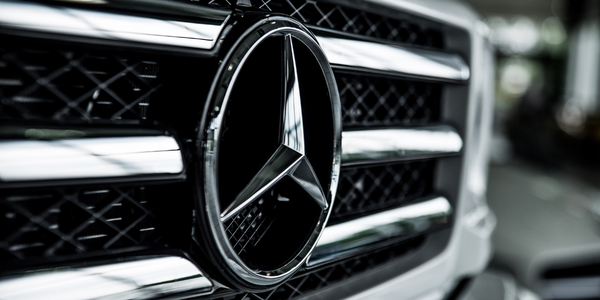
Case Study
Integral Plant Maintenance
Mercedes-Benz and his partner GAZ chose Siemens to be its maintenance partner at a new engine plant in Yaroslavl, Russia. The new plant offers a capacity to manufacture diesel engines for the Russian market, for locally produced Sprinter Classic. In addition to engines for the local market, the Yaroslavl plant will also produce spare parts. Mercedes-Benz Russia and his partner needed a service partner in order to ensure the operation of these lines in a maintenance partnership arrangement. The challenges included coordinating the entire maintenance management operation, in particular inspections, corrective and predictive maintenance activities, and the optimizing spare parts management. Siemens developed a customized maintenance solution that includes all electronic and mechanical maintenance activities (Integral Plant Maintenance).