公司规模
Large Corporate
地区
- America
国家
- United States
产品
- QlikView
实施规模
- Enterprise-wide Deployment
影响指标
- Productivity Improvements
- Cost Savings
技术
- 分析与建模 - 实时分析
适用功能
- 离散制造
- 销售与市场营销
用例
- 自动化制造系统
- 供应链可见性(SCV)
关于客户
Larson Manufacturing is the largest supplier of storm doors and windows in the United States. The company is based in South Dakota and operates multiple manufacturing and distribution centers. Larson Manufacturing sells its products via a rich partner network as well as online channels. The company operates in the manufacturing industry and has a significant presence in the market.
挑战
Larson Manufacturing, the largest supplier of storm doors and windows in the US, was facing several challenges. The company was struggling to obtain timely access to accurate information. The limited time for analyzing and correlating data was another significant challenge. Furthermore, there was a lack of executive visibility into the company's operations and performance. These challenges were hindering the company's ability to make informed decisions and optimize its operations.
解决方案
To address these challenges, Larson Manufacturing deployed QlikView across the organization's supply chain enterprise. QlikView is a business intelligence tool that provides self-service data visualization, reporting, and analytics capabilities. The company now has more than 70 production QlikView applications, including business-critical discovery applications in sales and marketing, manufacturing, distribution, finance, HR, and procurement. These applications enable the company to analyze and correlate data effectively, providing timely and accurate information for decision-making.
运营影响
Case Study missing?
Start adding your own!
Register with your work email and create a new case study profile for your business.
相关案例.
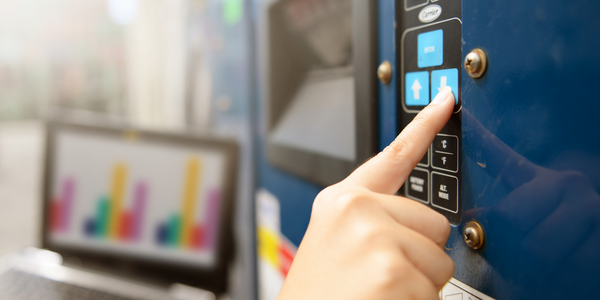
Case Study
Remote Temperature Monitoring of Perishable Goods Saves Money
RMONI was facing temperature monitoring challenges in a cold chain business. A cold chain must be established and maintained to ensure goods have been properly refrigerated during every step of the process, making temperature monitoring a critical business function. Manual registration practice can be very costly, labor intensive and prone to mistakes.
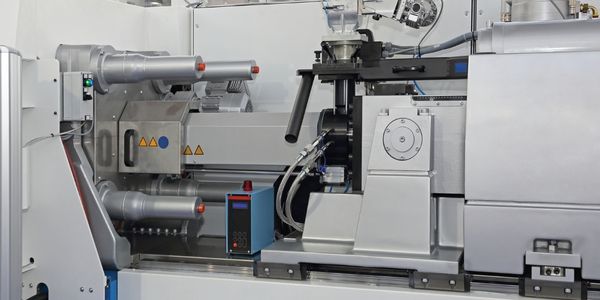
Case Study
Plastic Spoons Case study: Injection Moulding
In order to meet customer expectations by supplying a wide variety of packaging units, from 36 to 1000 spoons per package, a new production and packaging line needed to be built. DeSter wanted to achieve higher production capacity, lower cycle time and a high degree of operator friendliness with this new production line.
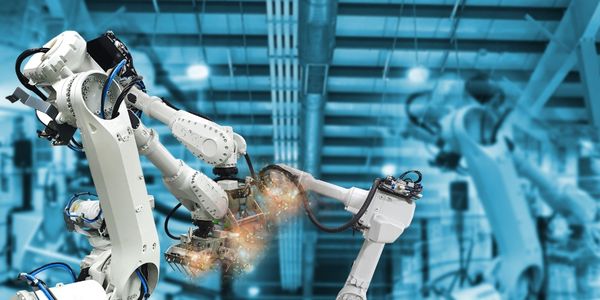
Case Study
Robot Saves Money and Time for US Custom Molding Company
Injection Technology (Itech) is a custom molder for a variety of clients that require precision plastic parts for such products as electric meter covers, dental appliance cases and spools. With 95 employees operating 23 molding machines in a 30,000 square foot plant, Itech wanted to reduce man hours and increase efficiency.
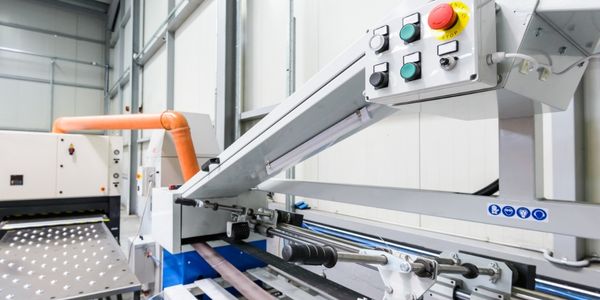
Case Study
Fully Automated Visual Inspection System
Tofflon has developed a fully automatic machine that uses light to inspect vials, medicine bottles, or infusion containers for glass fragments, aluminum particles, rubber grains, hairs, fibers, or other contaminants. It also detects damaged containers with cracks or inclusions (microscopic imperfections), automatically removing faulty or contaminated products. In order to cover all production processes for freeze-dried pharmaceuticals, Tofflon needed to create an open, consistent, and module-based automation concept.
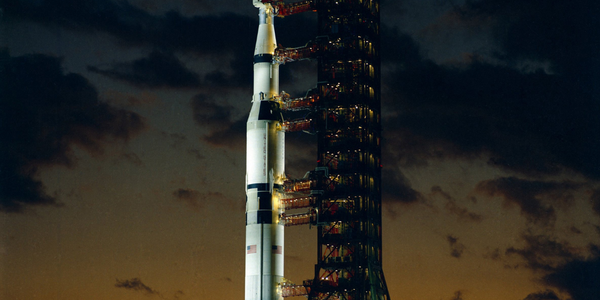
Case Study
SAP Leonardo Enabling Rocket Science
At times, ULA has as many as 15 different operating systems dedicated to overlapping processes, such as rocket design, testing, and launch. Multiple systems created unnecessary costs and unwanted confusion among workers at offices, factories, and launch sites in different location. In order to improve collaboration and transparency during vital activities that directly influence mission success, ULA wanted to improve data sharing and streamline manufacturing processes.