公司规模
SME
地区
- Europe
国家
- Denmark
产品
- QlikView
技术栈
- QlikView
实施规模
- Enterprise-wide Deployment
影响指标
- Productivity Improvements
- Cost Savings
技术
- 分析与建模 - 实时分析
适用功能
- 销售与市场营销
- 采购
用例
- 库存管理
- 供应链可见性(SCV)
服务
- 软件设计与工程服务
关于客户
Roland Scandinavia A/S is the leading distributor in the Nordic countries of musical instruments and large-format color printers. The company has an annual turnover of DKK 266 million and employs 56 people. The head office of Roland is located in Copenhagen, and the company has offices in Norway, Sweden, and Finland. Roland Scandinavia was established in 1981 and has grown rapidly since its inception. Today, it is the leading distributor in the Nordic countries of electronic musical instruments and large-format printers. The company has 30-35,000 part numbers and 100,000 transactions a year.
挑战
Roland Scandinavia A/S, a leading distributor of musical instruments and large-format color printers in the Nordic countries, was struggling with managing a rapidly increasing volume of data from procurement, storage, and sales. The company had invested in the ERP system Scala to help create the needed overview, but it soon became obvious that it was difficult to draw out useful data. The manual reports in different systems were not providing the necessary insights and the company was in need of a solution that could provide a comprehensive overview of the company data.
解决方案
Roland was recommended QlikView as a solution to their problem. QlikTech had developed a ready-made QlikView Template for Scala and after the first presentation of the system, it only took a few hours before the first graphical representation of the company data was ready. The QlikView software takes up so little space that it fits on a laptop, providing an instant and total overview of the company data. Today, around 15 employees at Roland use QlikView on a daily basis. It is the preferred tool of the Sales Managers, but the users vary from Directors to Sales Assistants.
运营影响
Case Study missing?
Start adding your own!
Register with your work email and create a new case study profile for your business.
相关案例.
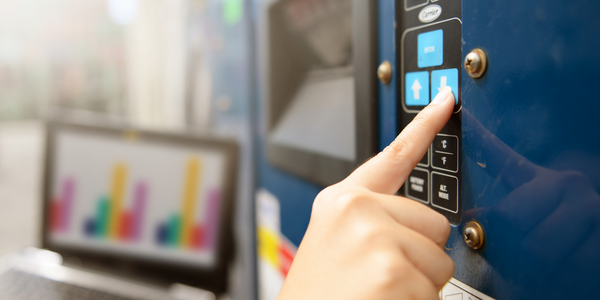
Case Study
Remote Temperature Monitoring of Perishable Goods Saves Money
RMONI was facing temperature monitoring challenges in a cold chain business. A cold chain must be established and maintained to ensure goods have been properly refrigerated during every step of the process, making temperature monitoring a critical business function. Manual registration practice can be very costly, labor intensive and prone to mistakes.
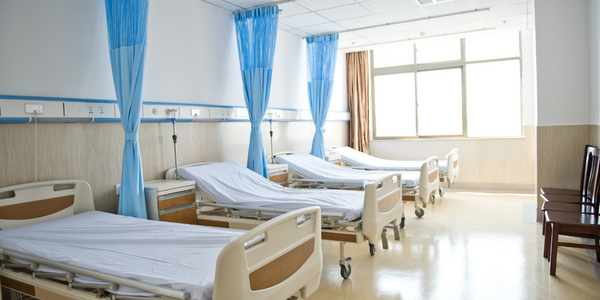
Case Study
Hospital Inventory Management
The hospital supply chain team is responsible for ensuring that the right medical supplies are readily available to clinicians when and where needed, and to do so in the most efficient manner possible. However, many of the systems and processes in use at the cancer center for supply chain management were not best suited to support these goals. Barcoding technology, a commonly used method for inventory management of medical supplies, is labor intensive, time consuming, does not provide real-time visibility into inventory levels and can be prone to error. Consequently, the lack of accurate and real-time visibility into inventory levels across multiple supply rooms in multiple hospital facilities creates additional inefficiency in the system causing over-ordering, hoarding, and wasted supplies. Other sources of waste and cost were also identified as candidates for improvement. Existing systems and processes did not provide adequate security for high-cost inventory within the hospital, which was another driver of cost. A lack of visibility into expiration dates for supplies resulted in supplies being wasted due to past expiry dates. Storage of supplies was also a key consideration given the location of the cancer center’s facilities in a dense urban setting, where space is always at a premium. In order to address the challenges outlined above, the hospital sought a solution that would provide real-time inventory information with high levels of accuracy, reduce the level of manual effort required and enable data driven decision making to ensure that the right supplies were readily available to clinicians in the right location at the right time.