公司规模
Large Corporate
地区
- Europe
国家
- Germany
产品
- QlikView
技术栈
- XML
- Oracle
- Excel
- Access
- ASCII
实施规模
- Enterprise-wide Deployment
影响指标
- Productivity Improvements
- Cost Savings
技术
- 分析与建模 - 实时分析
用例
- 过程控制与优化
- 质量预测分析
服务
- 数据科学服务
关于客户
The Reifenhäuser Group is the world’s largest and leading supplier of machines and manufacturing plant for the plasticisation of thermoplastic synthetic materials. The company head office is in Troisdorf, NorthRhine Westphalia, Germany. The company is a market leader and derives 80 per cent of its revenue from its export business. Companies use its machines worldwide to manufacture transparent blister packaging and synthetic materials for babies’ nappies. The company is a contract manufacturer and constructs each plant only once. The company has to consider various factors such as the environmental conditions at manufacturing sites and the changing landscape of the synthetic materials and plastic processing industry.
挑战
Reifenhäuser, a leading supplier of machines and manufacturing plant for the plasticisation of thermoplastic synthetic materials, faced challenges due to the changing landscape of the synthetic materials and plastic processing industry. The industry faced demands for plastics to bear the “green dot” to show their suitability for recycling and it’s now necessary to meet even tougher environmental standards to find solutions which are not hydrocarbons-based. The company also had to consider the environmental conditions at manufacturing sites. The company was also facing issues with its previous systems which had failed to provide any comprehensive evaluation of the in-house databases. The costs involved in making even the slightest modifications were prohibitive. Using Excel spreadsheets when working on complex analysis operations was unproductive and the results could not be easily reproduced.
解决方案
Reifenhäuser deployed QlikView to 200 for analysis of turnover and margins, lead and turnaround times, deadline compliance, project schedules, and recycling of product items. The company wanted to make sure that performance figures and visualisation were available for use on all its corporate data— whether in Oracle, Access, XML, or ASCII. The solution had to provide transparency not only on the figures but also on the processes. The company needed to break the data down into the finest detail without tying up its data programmers for weeks on end to work on it. QlikView is always there on the spot when managers have to define performance figures and ratios. This requires input from the various specialist departments but critically a general feeling of acceptance by everyone.
运营影响
Case Study missing?
Start adding your own!
Register with your work email and create a new case study profile for your business.
相关案例.
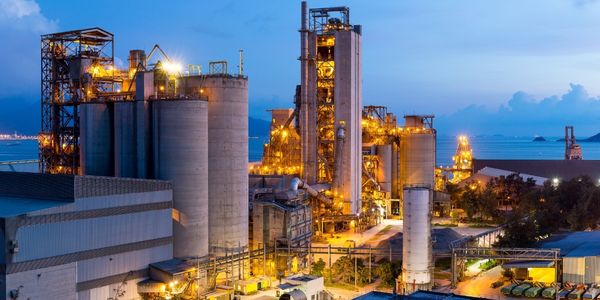
Case Study
System 800xA at Indian Cement Plants
Chettinad Cement recognized that further efficiencies could be achieved in its cement manufacturing process. It looked to investing in comprehensive operational and control technologies to manage and derive productivity and energy efficiency gains from the assets on Line 2, their second plant in India.
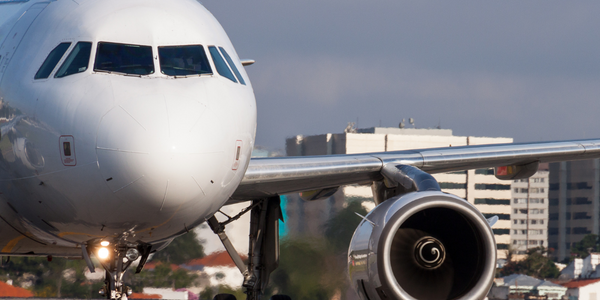
Case Study
Airbus Soars with Wearable Technology
Building an Airbus aircraft involves complex manufacturing processes consisting of thousands of moving parts. Speed and accuracy are critical to business and competitive advantage. Improvements in both would have high impact on Airbus’ bottom line. Airbus wanted to help operators reduce the complexity of assembling cabin seats and decrease the time required to complete this task.
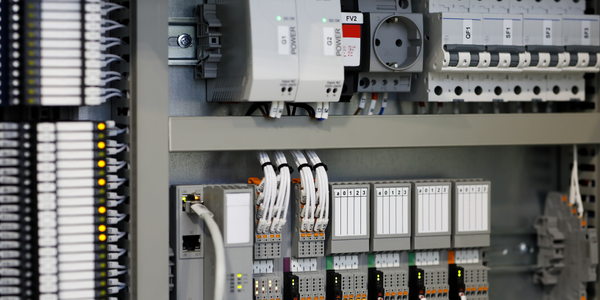
Case Study
Improving Production Line Efficiency with Ethernet Micro RTU Controller
Moxa was asked to provide a connectivity solution for one of the world's leading cosmetics companies. This multinational corporation, with retail presence in 130 countries, 23 global braches, and over 66,000 employees, sought to improve the efficiency of their production process by migrating from manual monitoring to an automatic productivity monitoring system. The production line was being monitored by ABB Real-TPI, a factory information system that offers data collection and analysis to improve plant efficiency. Due to software limitations, the customer needed an OPC server and a corresponding I/O solution to collect data from additional sensor devices for the Real-TPI system. The goal is to enable the factory information system to more thoroughly collect data from every corner of the production line. This will improve its ability to measure Overall Equipment Effectiveness (OEE) and translate into increased production efficiencies. System Requirements • Instant status updates while still consuming minimal bandwidth to relieve strain on limited factory networks • Interoperable with ABB Real-TPI • Small form factor appropriate for deployment where space is scarce • Remote software management and configuration to simplify operations
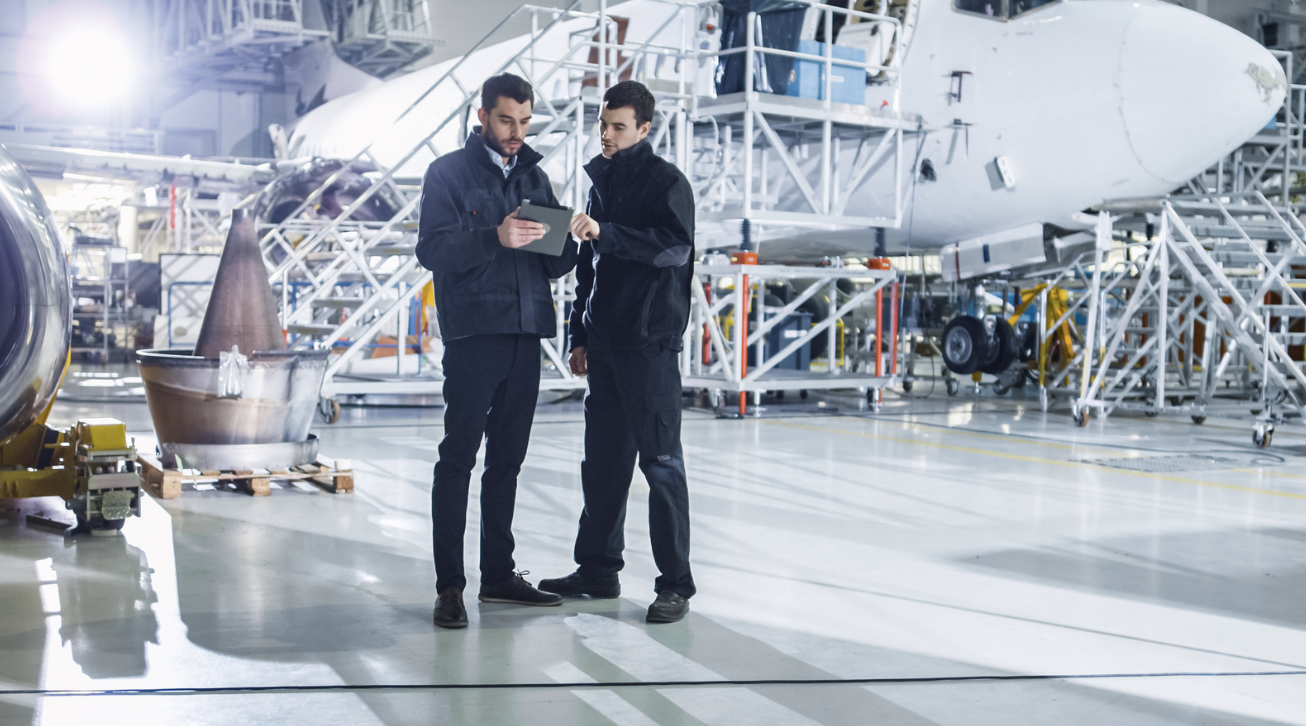
Case Study
Developing Smart Tools for the Airbus Factory
Manufacturing and assembly of aircraft, which involves tens of thousands of steps that must be followed by the operators, and a single mistake in the process could cost hundreds of thousands of dollars to fix, makes the room for error very small.