技术
- 分析与建模 - 数字孪生/模拟
- 机器人 - 自动导引车 (AGV)
适用行业
- 汽车
- 建筑与基础设施
适用功能
- 产品研发
- 质量保证
用例
- 结构健康监测
- 车辆性能监测
服务
- 测试与认证
关于客户
Rimac Automobili 是一家为全球汽车公司开发和制造关键电气化系统的科技公司。该公司由首席执行官 Mate Rimac 于 2011 年创立,拥有众多客户,包括汽车原始设备制造商、一级供应商和新兴企业。除了提供符合环境和安全法规的创新电动汽车 (EV) 技术外,Rimac 最近还推出了第二代自己的电动超级跑车 – Rimac C_Two。该公司总部位于克罗地亚萨格勒布郊区,拥有员工 600 多人。 Rimac 的开发部门包括八名结构 CAE 工程师,他们与 HyperWorks 合作支持汽车的结构设计。
挑战
Rimac Automobili 是一家为全球汽车公司提供电气化系统的领先开发商和制造商,在 Rimac C-Two(汽车行业最大的单一碳纤维部件)的单体壳结构设计方面面临着重大挑战。主要的挑战是材料,一种用环氧树脂增强的轻质碳纤维。由于这种碳纤维是一种正交各向异性脆性材料,因此在有限元 (FE) 材料卡中表示它非常困难。设计电动汽车时最重要的参数之一是重量。车辆越轻,车辆续航里程就越多,这可以导致电动汽车的接受度更高。 Rimac 工程师在其概念超级跑车 C_Two 的开发过程中采用轻量化方法,其任务是将单体壳设计为具有前所未有尺寸的单一碳纤维部件。
解决方案
为了克服这一结构挑战,Rimac 工程师利用 Altair HyperWorks。目标是实现真实测试和虚拟测试之间最紧密的关联,以最大限度地减少失败。开发过程从零件提案开始,根据模拟运行的结果,CAE 团队与设计工程师一起制定了提案。然后对模型进行更新,并在每个组件级别再次进行测试,直到团队看到模拟和物理性能之间的完美关联,从而实现按预期执行的设计。车辆工程 CAE 设计团队进行的模拟涉及 123 个载荷工况。这是在组件、系统和车辆级别,以及线性、非线性、静态和动态模拟。整个开发项目的工期为5个月。除了提供软件许可证和专家支持外,Altair 还推出了 HyperWorks Unlimited 虚拟设备 (HWUL-VA),它是 Altair 创新云产品的一部分。
运营影响
数量效益
Case Study missing?
Start adding your own!
Register with your work email and create a new case study profile for your business.
相关案例.
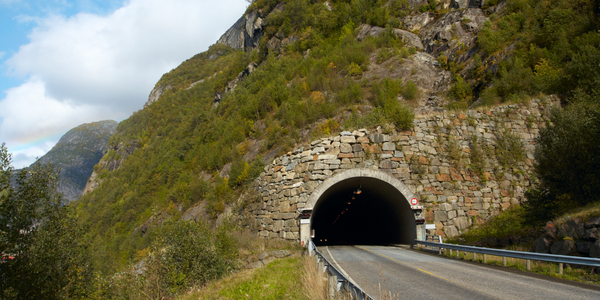
Case Study
IoT System for Tunnel Construction
The Zenitaka Corporation ('Zenitaka') has two major business areas: its architectural business focuses on structures such as government buildings, office buildings, and commercial facilities, while its civil engineering business is targeted at structures such as tunnels, bridges and dams. Within these areas, there presented two issues that have always persisted in regard to the construction of mountain tunnels. These issues are 'improving safety" and "reducing energy consumption". Mountain tunnels construction requires a massive amount of electricity. This is because there are many kinds of electrical equipment being used day and night, including construction machinery, construction lighting, and ventilating fan. Despite this, the amount of power consumption is generally not tightly managed. In many cases, the exact amount of power consumption is only ascertained when the bill from the power company becomes available. Sometimes, corporations install demand-monitoring equipment to help curb the maximum power demanded. However, even in these cases, the devices only allow the total volume of power consumption to be ascertained, or they may issue warnings to prevent the contracted volume of power from being exceeded. In order to tackle the issue of reducing power consumption, it was first necessary to obtain an accurate breakdown of how much power was being used in each particular area. In other words, we needed to be able to visualize the amount of power being consumed. Safety, was also not being managed very rigorously. Even now, tunnel construction sites often use a 'name label' system for managing entry into the work site. Specifically, red labels with white reverse sides that bear the workers' names on both sides are displayed at the tunnel work site entrance. The workers themselves then flip the name label to the appropriate side when entering or exiting from the work site to indicate whether or not they are working inside the tunnel at any given time. If a worker forgets to flip his or her name label when entering or exiting from the tunnel, management cannot be performed effectively. In order to tackle the challenges mentioned above, Zenitaka decided to build a system that could improve the safety of tunnel construction as well as reduce the amount of power consumed. In other words, this new system would facilitate a clear picture of which workers were working in each location at the mountain tunnel construction site, as well as which processes were being carried out at those respective locations at any given time. The system would maintain the safety of all workers while also carefully controlling the electrical equipment to reduce unnecessary power consumption. Having decided on the concept, our next concern was whether there existed any kind of robust hardware that would not break down at the construction work site, that could move freely in response to changes in the working environment, and that could accurately detect workers and vehicles using radio frequency identification (RFID). Given that this system would involve many components that were new to Zenitaka, we decided to enlist the cooperation of E.I.Sol Co., Ltd. ('E.I.Sol') as our joint development partner, as they had provided us with a highly practical proposal.
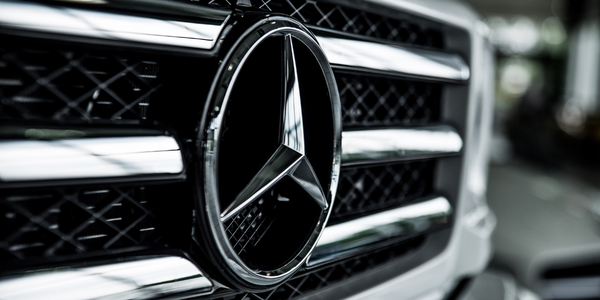
Case Study
Integral Plant Maintenance
Mercedes-Benz and his partner GAZ chose Siemens to be its maintenance partner at a new engine plant in Yaroslavl, Russia. The new plant offers a capacity to manufacture diesel engines for the Russian market, for locally produced Sprinter Classic. In addition to engines for the local market, the Yaroslavl plant will also produce spare parts. Mercedes-Benz Russia and his partner needed a service partner in order to ensure the operation of these lines in a maintenance partnership arrangement. The challenges included coordinating the entire maintenance management operation, in particular inspections, corrective and predictive maintenance activities, and the optimizing spare parts management. Siemens developed a customized maintenance solution that includes all electronic and mechanical maintenance activities (Integral Plant Maintenance).
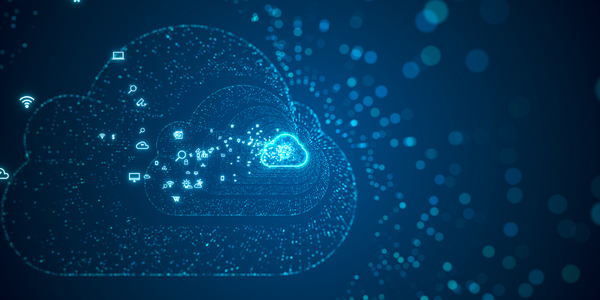
Case Study
Splunk Partnership Ties Together Big Data & IoT Services
Splunk was faced with the need to meet emerging customer demands for interfacing IoT projects to its suite of services. The company required an IoT partner that would be able to easily and quickly integrate with its Splunk Enterprise platform, rather than allocating development resources and time to building out an IoT interface and application platform.