公司规模
SME
地区
- Europe
国家
- France
产品
- COMSOL Multiphysics
技术栈
- Multiphysics Simulation
- Finite Element Analysis (FEA)
实施规模
- Enterprise-wide Deployment
影响指标
- Energy Saving
- Productivity Improvements
- Innovation Output
技术
- 分析与建模 - 数字孪生/模拟
- 分析与建模 - 预测分析
- 分析与建模 - 实时分析
适用行业
- 可再生能源
- 半导体
适用功能
- 流程制造
- 产品研发
用例
- 预测性维护
- 过程控制与优化
- 数字孪生
服务
- 软件设计与工程服务
- 系统集成
关于客户
EMIX is a company specializing in the production of photovoltaic-quality silicon using an innovative continuous cold crucible casting (4C) process. They hold several patents and an exclusive worldwide operating license for this technology. EMIX has been using multiphysics simulation for eight years to optimize their production parameters and improve the efficiency of their manufacturing process. The company aims to reduce the cost of silicon wafers and improve their purity to make solar energy more competitive with traditional fossil fuels.
挑战
The semiconductor industry relies heavily on silicon wafers, which are also crucial for photovoltaic (PV) applications. However, the cost per unit of power generated by solar cells needs to be reduced to make solar energy competitive with fossil fuels. EMIX's challenge was to optimize their continuous cold crucible casting (4C) process to produce high-purity silicon efficiently. This process involves numerous variables, including cooling methods, pull rates, and electromagnetic fields, which need to be optimized to improve production efficiency and reduce costs.
解决方案
EMIX uses COMSOL Multiphysics software to perform simulations that optimize various parameters of their 4C process. These simulations include multiscale electromagnetic and 3D continuous casting simulations, which help estimate inductance and impedance, optimize crucible design, and improve electrical efficiency. The simulations also allow for the input of parameters such as electromagnetic power, crystallization rate, and cooling zone height. By using these simulations, EMIX has been able to achieve a compromise between high production rates and low stresses in the silicon ingots. The Heat Transfer in Fluids and Laminar Flow interfaces in COMSOL were used to calculate phase changes in the silicon as it solidified in the crucible.
运营影响
数量效益
Case Study missing?
Start adding your own!
Register with your work email and create a new case study profile for your business.
相关案例.
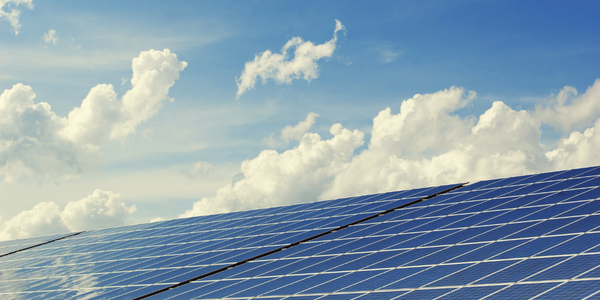
Case Study
Remote Monitoring & Predictive Maintenance App for a Solar Energy System
The maintenance & tracking of various modules was an overhead for the customer due to the huge labor costs involved. Being an advanced solar solutions provider, they wanted to ensure early detection of issues and provide the best-in-class customer experience. Hence they wanted to automate the whole process.
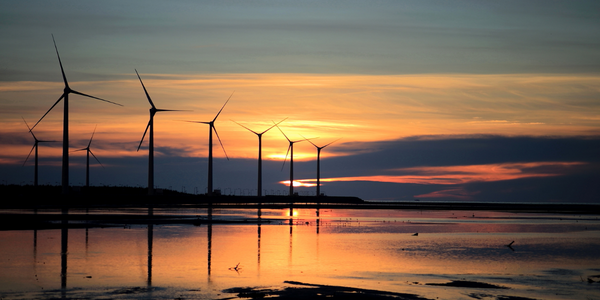
Case Study
Vestas: Turning Climate into Capital with Big Data
Making wind a reliable source of energy depends greatly on the placement of the wind turbines used to produce electricity. Turbulence is a significant factor as it strains turbine components, making them more likely to fail. Vestas wanted to pinpoint the optimal location for wind turbines to maximize power generation and reduce energy costs.
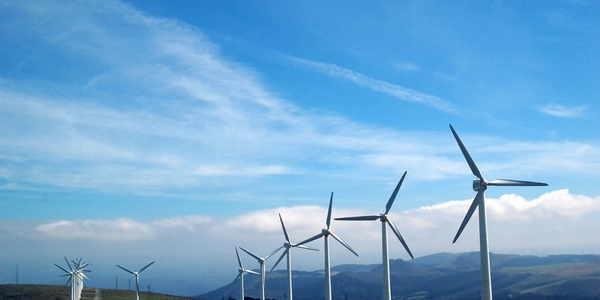
Case Study
Siemens Wind Power
Wind provides clean, renewable energy. The core concept is simple: wind turbines spin blades to generate power. However, today's systems are anything but simple. Modern wind turbines have blades that sweep a 120 meter circle, cost more than 1 million dollars and generate multiple megawatts of power. Each turbine may include up to 1,000 sensors and actuators – integrating strain gages, bearing monitors and power conditioning technology. The turbine can control blade speed and power generation by altering the blade pitch and power extraction. Controlling the turbine is a sophisticated job requiring many cooperating processors closing high-speed loops and implementing intelligent monitoring and optimization algorithms. But the real challenge is integrating these turbines so that they work together. A wind farm may include hundreds of turbines. They are often installed in difficult-to-access locations at sea. The farm must implement a fundamentally and truly distributed control system. Like all power systems, the goal of the farm is to match generation to load. A farm with hundreds of turbines must optimize that load by balancing the loading and generation across a wide geography. Wind, of course, is dynamic. Almost every picture of a wind farm shows a calm sea and a setting sun. But things get challenging when a storm goes through the wind farm. In a storm, the control system must decide how to take energy out of gusts to generate constant power. It must intelligently balance load across many turbines. And a critical consideration is the loading and potential damage to a half-billion-dollar installed asset. This is no environment for a slow or undependable control system. Reliability and performance are crucial.
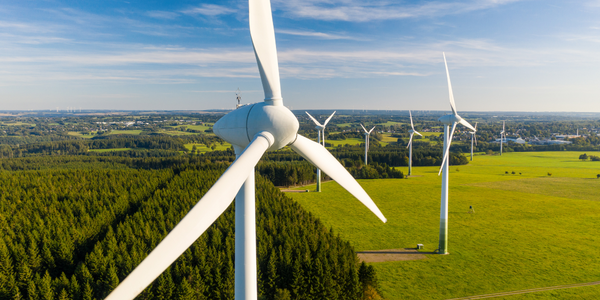
Case Study
Remote Monitoring and Control for a Windmill Generator
As concerns over global warming continue to grow, green technologies are becoming increasingly popular. Wind turbine companies provide an excellent alternative to burning fossil fuels by harnessing kinetic energy from the wind and converting it into electricity. A typical wind farm may include over 80 wind turbines so efficient and reliable networks to manage and control these installations are imperative. Each wind turbine includes a generator and a variety of serial components such as a water cooler, high voltage transformer, ultrasonic wind sensors, yaw gear, blade bearing, pitch cylinder, and hub controller. All of these components are controlled by a PLC and communicate with the ground host. Due to the total integration of these devices into an Ethernet network, one of our customers in the wind turbine industry needed a serial-to-Ethernet solution that can operate reliably for years without interruption.
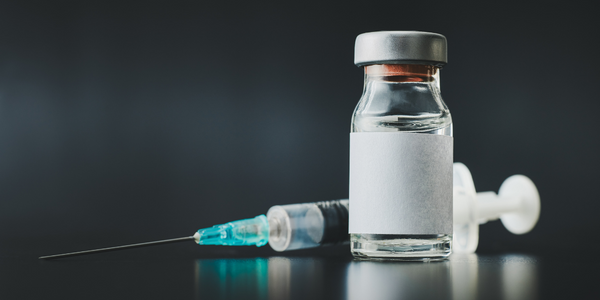
Case Study
Temperature monitoring for vaccine fridges
Dulas wanted a way to improve the reliability of the cold chain, facilitating maintenance and ensuring fewer vaccines are spoiled. Dulas wanted an M2M solution which would enable them to record and report the temperature inside vaccine refrigerators.
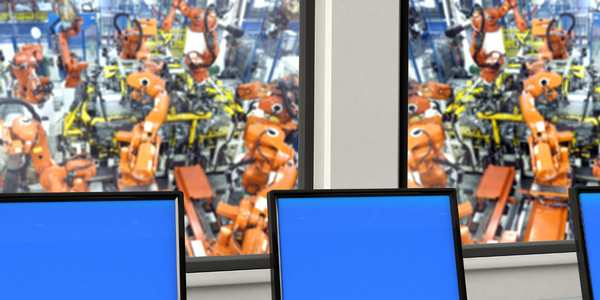
Case Study
KINESYS Semiconductor Factory Automation Software
KINESYS Software provides both Integrated Device Manufacturer (IDM) and Original Equipment Manufacturer (OEM) customers world-class software products and solutions for advanced wafer and device traceability and process management. KINESYS offers state of the art database technology with a core focus on SEMI standards. KINESYS’ challenge was to make back-end processing failure-free and easy to use for clients while supporting licensing models more adaptable to changing industry needs.