公司规模
Mid-size Company
地区
- America
国家
- United States
产品
- InTouch HMI
- Historian
- Historian Clients
技术栈
- Wonderware
- System Platform
实施规模
- Enterprise-wide Deployment
影响指标
- Productivity Improvements
- Cost Savings
技术
- 应用基础设施与中间件 - 数据交换与集成
适用行业
- 食品与饮料
适用功能
- 流程制造
用例
- 过程控制与优化
- 预测性维护
服务
- 系统集成
关于客户
Hawaiian Commercial & Sugar Company (HC&S) is a sugar producer based in Puunene, Maui. The company operates a 37,000-acre plantation and adjacent factory where it grows and processes sugarcane. HC&S has been in business since the late 19th century and has grown into Hawaii's largest provider of raw sugar, producing about 200,000 tons annually. Despite its significant production, HC&S competes with much larger mainland sugar companies and makers of artificial sweeteners. To maintain its market share, HC&S offers its own specialty sugar brands, which cost more to produce. Therefore, efficiency is crucial for HC&S to remain cost-competitive. In addition to sugar, HC&S also produces a by-product called bagasse, a fibrous residue used as fuel to generate steam and electricity. This electricity is used in the sugar-production process and any excess is sold to the local electric utility.
挑战
Hawaiian Commercial & Sugar Company (HC&S) is a major provider of raw sugar in Hawaii, producing about 200,000 tons annually. However, the company faces stiff competition from larger mainland sugar companies and makers of artificial sweeteners, which have been taking large bites out of the mature sugar market in recent years. To maintain its share of that market, HC&S offers its own specialty sugar brands, which cost more to produce. Therefore, efficiency becomes doubly important to achieve HC&S’s necessary cost-competitiveness. HC&S also makes something else, a “product” that it not only sells, but also uses to increase its efficiency. A fibrous residue called bagasse is used at HC&S as fuel to generate steam and electricity. Most of the steam is used to generate electricity, while the exhaust steam is funneled back into the sugar-production process. Electricity produced at the plant is also recycled back into sugar processing, with the excess power being sold to the local electric utility.
解决方案
Looking for a way to further optimise its operations, HC&S implemented InTouch HMI powered by Wonderware for its ease of use, flexibility and ability to integrate with the Puunene plant’s DCS system and electrical relays. HC&S’ plant intelligence system started out with three separate InTouch HMI client applications – feeding their Historian powered by Wonderware for sugar-plant operations, steam-plant operations and power monitoring - with access to a combined 17,000 tags in a two-tier client/server topology. The company then integrated all of its InTouch HMI client applications into one large system that could be used to gain plant intelligence information. The plant intelligence system has grown from two tiers into a three-tier topology; the single InTouch HMI client application has access to 30,000 tags, enabling employees to access data from throughout the production process from any workstation in the plant or any remote workstation around the world. Several plant operators who are frequent, day-today users of the InTouch HMI have the application installed at their workstations. Other staff, such as upper management, who use InTouch software less often log onto Historian Clients real-time plant portal software to launch InTouch HMI for Terminal Services when they need to access the HMI.
运营影响
数量效益
Case Study missing?
Start adding your own!
Register with your work email and create a new case study profile for your business.
相关案例.
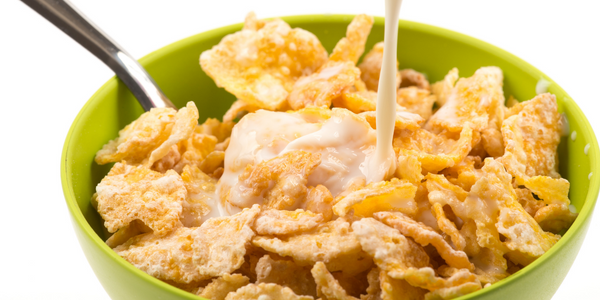
Case Study
The Kellogg Company
Kellogg keeps a close eye on its trade spend, analyzing large volumes of data and running complex simulations to predict which promotional activities will be the most effective. Kellogg needed to decrease the trade spend but its traditional relational database on premises could not keep up with the pace of demand.
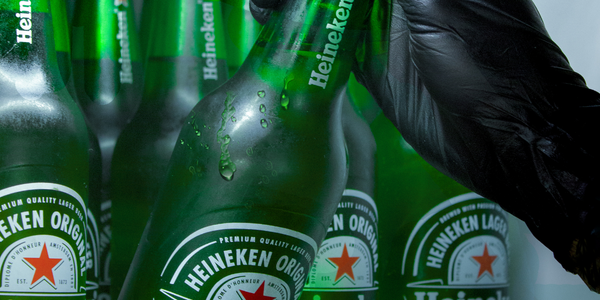
Case Study
HEINEKEN Uses the Cloud to Reach 10.5 Million Consumers
For 2012 campaign, the Bond promotion, it planned to launch the campaign at the same time everywhere on the planet. That created unprecedented challenges for HEINEKEN—nowhere more so than in its technology operation. The primary digital content for the campaign was a 100-megabyte movie that had to play flawlessly for millions of viewers worldwide. After all, Bond never fails. No one was going to tolerate a technology failure that might bruise his brand.Previously, HEINEKEN had supported digital media at its outsourced datacenter. But that datacenter lacked the computing resources HEINEKEN needed, and building them—especially to support peak traffic that would total millions of simultaneous hits—would have been both time-consuming and expensive. Nor would it have provided the geographic reach that HEINEKEN needed to minimize latency worldwide.
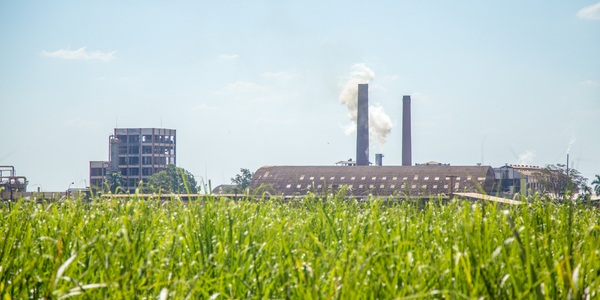
Case Study
Energy Management System at Sugar Industry
The company wanted to use the information from the system to claim under the renewable energy certificate scheme. The benefit to the company under the renewable energy certificates is Rs 75 million a year. To enable the above, an end-to-end solution for load monitoring, consumption monitoring, online data monitoring, automatic meter data acquisition which can be exported to SAP and other applications is required.
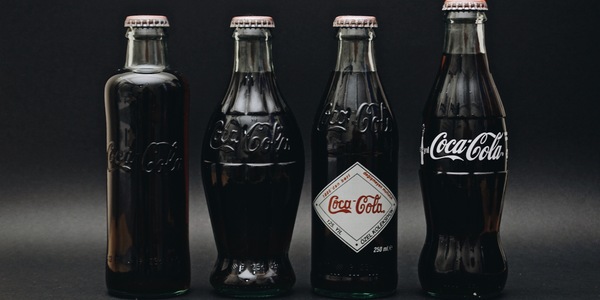
Case Study
Coca Cola Swaziland Conco Case Study
Coco Cola Swaziland, South Africa would like to find a solution that would enable the following results: - Reduce energy consumption by 20% in one year. - Formulate a series of strategic initiatives that would enlist the commitment of corporate management and create employee awareness while helping meet departmental targets and investing in tools that assist with energy management. - Formulate a series of tactical initiatives that would optimize energy usage on the shop floor. These would include charging forklifts and running cold rooms only during off-peak periods, running the dust extractors only during working hours and basing lights and air-conditioning on someone’s presence. - Increase visibility into the factory and other processes. - Enable limited, non-intrusive control functions for certain processes.
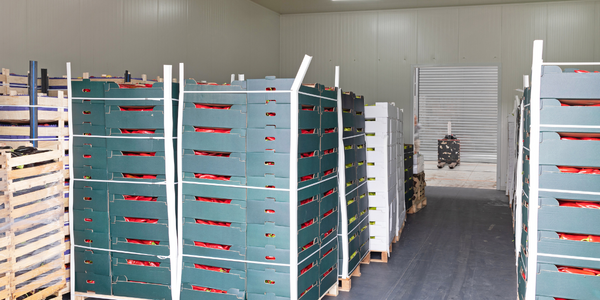
Case Study
Temperature Monitoring for Restaurant Food Storage
When it came to implementing a solution, Mr. Nesbitt had an idea of what functionality that he wanted. Although not mandated by Health Canada, Mr. Nesbitt wanted to ensure quality control issues met the highest possible standards as part of his commitment to top-of-class food services. This wish list included an easy-to use temperature-monitoring system that could provide a visible display of the temperatures of all of his refrigerators and freezers, including historical information so that he could review the performance of his equipment. It also had to provide alert notification (but email alerts and SMS text message alerts) to alert key staff in the event that a cooling system was exceeding pre-set warning limits.
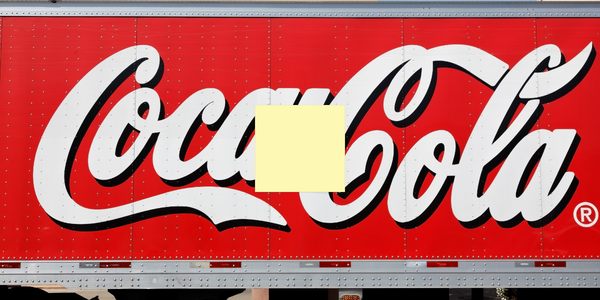
Case Study
Coca-Cola Refreshments, U.S.
Coca-Cola Refreshments owns and manages Coca-Cola branded refrigerators in retail establishments. Legacy systems were used to locate equipment information by logging onto multiple servers which took up to 8 hours to update information on 30-40 units. The company had no overall visibility into equipment status or maintenance history.