技术
- 功能应用 - 仓库管理系统 (WMS)
- 其他 - 电池
适用行业
- 汽车
- 可再生能源
适用功能
- 销售与市场营销
- 仓库和库存管理
用例
- 拣选/分拣/定位
- 时间敏感网络
服务
- 系统集成
关于客户
Wallbox 是一家创建先进电动汽车充电和能源管理系统的公司。该公司成立于 2015 年,旨在改变世界使用能源的方式。在短短七年的时间里,Wallbox 已在全球设立了商业办事处,员工数量已增至约 1,250 名,并在三大洲设立了四个制造中心。最初,Wallbox专注于解决国内用户的电动汽车充电需求。然而,此后它的市场多元化,包括企业和公众。该公司正在从单纯以产品为中心转向销售服务,通过预先制定的服务级别协议提供充电器监控和运营服务。
挑战
Wallbox 是一家电动汽车充电和能源管理公司,在管理数据方面面临着重大挑战。自2015年成立以来,公司经历了快速发展,员工人数在短时间内从50人扩展至1000多人。这种增长导致不同部门使用的工具和应用程序数量增加,从而形成阻碍洞察力和质量控制的数据孤岛。公司数据分散在各个平台,质量问题难以追溯和解决。此外,仪表板中嵌入的业务逻辑的发展也很复杂。另一个挑战是定期更新定制集成所需的工具,事实证明这是一个成本高昂且耗时的过程。 Wallbox 需要一种解决方案来打破这些孤岛并将其所有数据整合到一个易于访问的位置。
解决方案
为了解决数据管理挑战,Wallbox 转向 Fivetran,这是一家以其可靠性和广泛的连接器而闻名的提供商。该公司设计了一个以云数据仓库为中心的现代数据堆栈,选择 Snowflake 作为其企业数据仓库,并选择 dbt 作为其建模工具。此设置允许 Wallbox 执行提取、加载、转换 (ELT) 操作,从而在数据仓库本身内转换数据。该解决方案的实施使 Wallbox 能够在几个月内启动并运行其第一个数据平台,从而以更具可扩展性的方式促进增长。与 Fivetran 的集成使 Wallbox 能够整合 30 到 40 个数据源,从而显着增加其仓库中数据的数量和价值。
运营影响
数量效益
Case Study missing?
Start adding your own!
Register with your work email and create a new case study profile for your business.
相关案例.
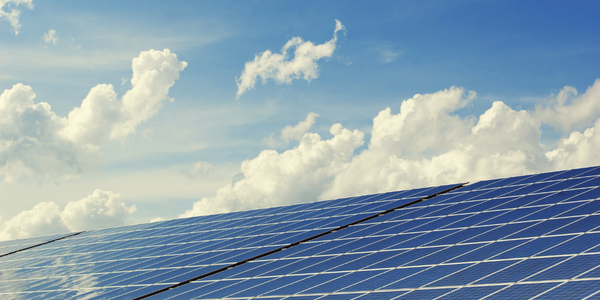
Case Study
Remote Monitoring & Predictive Maintenance App for a Solar Energy System
The maintenance & tracking of various modules was an overhead for the customer due to the huge labor costs involved. Being an advanced solar solutions provider, they wanted to ensure early detection of issues and provide the best-in-class customer experience. Hence they wanted to automate the whole process.
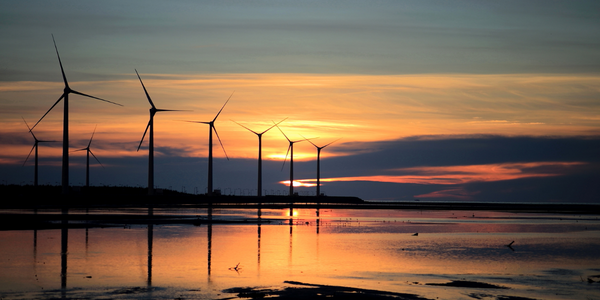
Case Study
Vestas: Turning Climate into Capital with Big Data
Making wind a reliable source of energy depends greatly on the placement of the wind turbines used to produce electricity. Turbulence is a significant factor as it strains turbine components, making them more likely to fail. Vestas wanted to pinpoint the optimal location for wind turbines to maximize power generation and reduce energy costs.
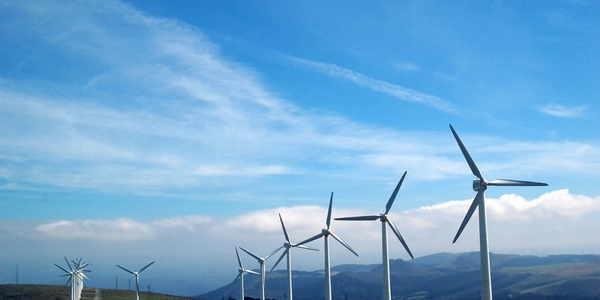
Case Study
Siemens Wind Power
Wind provides clean, renewable energy. The core concept is simple: wind turbines spin blades to generate power. However, today's systems are anything but simple. Modern wind turbines have blades that sweep a 120 meter circle, cost more than 1 million dollars and generate multiple megawatts of power. Each turbine may include up to 1,000 sensors and actuators – integrating strain gages, bearing monitors and power conditioning technology. The turbine can control blade speed and power generation by altering the blade pitch and power extraction. Controlling the turbine is a sophisticated job requiring many cooperating processors closing high-speed loops and implementing intelligent monitoring and optimization algorithms. But the real challenge is integrating these turbines so that they work together. A wind farm may include hundreds of turbines. They are often installed in difficult-to-access locations at sea. The farm must implement a fundamentally and truly distributed control system. Like all power systems, the goal of the farm is to match generation to load. A farm with hundreds of turbines must optimize that load by balancing the loading and generation across a wide geography. Wind, of course, is dynamic. Almost every picture of a wind farm shows a calm sea and a setting sun. But things get challenging when a storm goes through the wind farm. In a storm, the control system must decide how to take energy out of gusts to generate constant power. It must intelligently balance load across many turbines. And a critical consideration is the loading and potential damage to a half-billion-dollar installed asset. This is no environment for a slow or undependable control system. Reliability and performance are crucial.
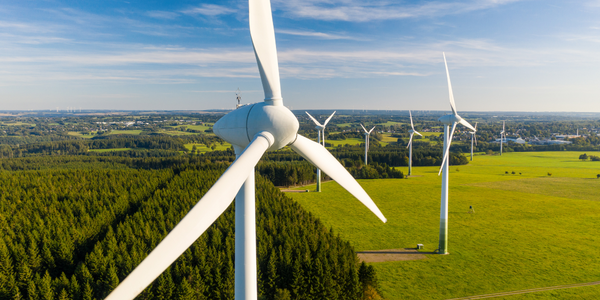
Case Study
Remote Monitoring and Control for a Windmill Generator
As concerns over global warming continue to grow, green technologies are becoming increasingly popular. Wind turbine companies provide an excellent alternative to burning fossil fuels by harnessing kinetic energy from the wind and converting it into electricity. A typical wind farm may include over 80 wind turbines so efficient and reliable networks to manage and control these installations are imperative. Each wind turbine includes a generator and a variety of serial components such as a water cooler, high voltage transformer, ultrasonic wind sensors, yaw gear, blade bearing, pitch cylinder, and hub controller. All of these components are controlled by a PLC and communicate with the ground host. Due to the total integration of these devices into an Ethernet network, one of our customers in the wind turbine industry needed a serial-to-Ethernet solution that can operate reliably for years without interruption.
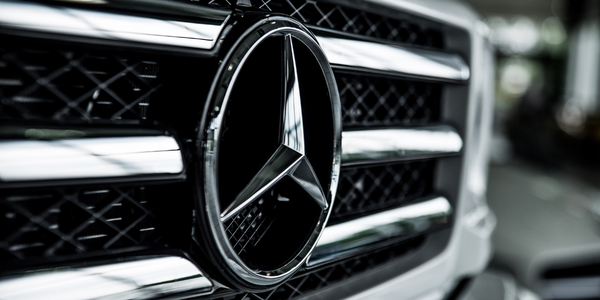
Case Study
Integral Plant Maintenance
Mercedes-Benz and his partner GAZ chose Siemens to be its maintenance partner at a new engine plant in Yaroslavl, Russia. The new plant offers a capacity to manufacture diesel engines for the Russian market, for locally produced Sprinter Classic. In addition to engines for the local market, the Yaroslavl plant will also produce spare parts. Mercedes-Benz Russia and his partner needed a service partner in order to ensure the operation of these lines in a maintenance partnership arrangement. The challenges included coordinating the entire maintenance management operation, in particular inspections, corrective and predictive maintenance activities, and the optimizing spare parts management. Siemens developed a customized maintenance solution that includes all electronic and mechanical maintenance activities (Integral Plant Maintenance).