Applicable Industries
- Automotive
Applicable Functions
- Product Research & Development
- Quality Assurance
Use Cases
- Time Sensitive Networking
- Visual Quality Detection
Services
- Testing & Certification
About The Customer
PSA Peugeot Citroën is a globally recognized automobile manufacturer, supported by two broad line brands, Peugeot and Citroën, and the expertise of its employees. With operations in 150 countries, the Group is actively expanding its sales in new, fast-growing markets, having sold 3,549,000 vehicles worldwide in 2011. As a responsible global corporate citizen, PSA Peugeot Citroën constantly innovates in the areas of safety and environmental protection to develop and produce cars that meet the expectations of Peugeot and Citroën customers around the world. 12 of the Group’s models have been awarded 5 stars in Euro NCAP crash tests. PSA Peugeot Citroën is Europe’s leading manufacturer of low-emission vehicles with 1 million units sold emitting less than 125.5g CO2/km in 2012, which makes them the European leader in this area.
The Challenge
PSA Peugeot Citroën, a world-class automobile manufacturer, was facing a significant challenge in the development of engine components, specifically the exhaust manifold. The design of the exhaust manifold is crucial for the optimal performance of combustion engines, and it has to withstand harsh operational conditions. PSA conducts complex thermo mechanical calculations to determine the lifetime of the exhaust manifold. From these calculations, design changes are derived and proposed to the supplier of the component. However, the supplier often found it difficult to correctly interpret the design improvements suggested by the PSA CAE engineers. Furthermore, a full evaluation cycle of such a design change took about three weeks, with no guarantee that it represented the final design status after that time. This led to the situation where only a few design changes and evaluations were possible within the given development timeframe, making the design of the manifold a critical task in the engine development. PSA needed to change the overall development workflow to be faster and to be able to evaluate more design variants in the same time.
The Solution
To address this challenge, PSA utilized HyperWorks’ morphing technology (HyperMorph) inside HyperMesh to quickly change the design of the exhaust manifold. This technology allowed for quick implementation of design changes while avoiding intermediate CAD changes. As a result, only a single CAD revision was needed when all improvements had been implemented. The new workflow with HyperWorks morphing technology significantly reduced the evaluation cycle from three weeks to just two days. This new process gave the CAE engineers the ability to do their own modifications without having to suggest them to the supplier. The morphing technology could also be used for a variety of other engine components such as the cylinder heads, crankcases, housing boxes, and more. The next step in the evolution of the development process will be the use of the morphing technology to perform shape optimization on such components.
Operational Impact
Quantitative Benefit
Case Study missing?
Start adding your own!
Register with your work email and create a new case study profile for your business.
Related Case Studies.
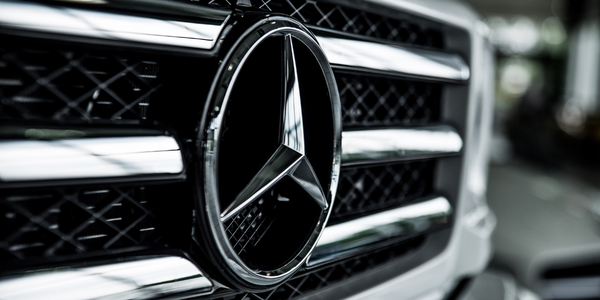
Case Study
Integral Plant Maintenance
Mercedes-Benz and his partner GAZ chose Siemens to be its maintenance partner at a new engine plant in Yaroslavl, Russia. The new plant offers a capacity to manufacture diesel engines for the Russian market, for locally produced Sprinter Classic. In addition to engines for the local market, the Yaroslavl plant will also produce spare parts. Mercedes-Benz Russia and his partner needed a service partner in order to ensure the operation of these lines in a maintenance partnership arrangement. The challenges included coordinating the entire maintenance management operation, in particular inspections, corrective and predictive maintenance activities, and the optimizing spare parts management. Siemens developed a customized maintenance solution that includes all electronic and mechanical maintenance activities (Integral Plant Maintenance).

Case Study
Monitoring of Pressure Pumps in Automotive Industry
A large German/American producer of auto parts uses high-pressure pumps to deburr machined parts as a part of its production and quality check process. They decided to monitor these pumps to make sure they work properly and that they can see any indications leading to a potential failure before it affects their process.