Technology Category
- Analytics & Modeling - Digital Twin / Simulation
- Functional Applications - Manufacturing Execution Systems (MES)
Applicable Industries
- Automotive
- Equipment & Machinery
Applicable Functions
- Product Research & Development
- Quality Assurance
Use Cases
- Time Sensitive Networking
- Visual Quality Detection
Services
- Hardware Design & Engineering Services
- Testing & Certification
About The Customer
Pragati Engineering, established in 2004, is one of the leading press tool design and manufacturing companies in India. The company manufactures quality made-to-order dies and fixtures for a variety of customers. Pragati Engineering is an ISO 9001:2008 certified organization and has solutions for all kinds of tooling requirements. The company's competency lies in the manufacture of Press Tools Fixtures and Panel Checkers for various critical sheet-metal components and assemblies. With new technologies, facilities, and experience in Press Tooling, the company is confident of seamlessly catering to any requirement in the sheet-metal forming segment. Pragati has an impressive list of clients from various sectors and supplies automotive sheet metal parts to leading companies such as Mahindra & Mahindra, Hitachi, JBM, TATA Ficosa, and Federal Management.
The Challenge
Pragati Engineering, a leading press tool design and manufacturing company in India, faced a significant challenge in their product development process. The company was struggling with the formation of cracks and wrinkles in one of their products during the manufacturing process. The traditional method of trial and error that the team used was unable to predict these occurrences. This method forced the team to manually correct the dies and rebuild new tools, leading to unplanned iterations and physical die tryouts. This not only substantially increased the product development time and cost but also impacted delivery schedules. Furthermore, product quality and output accuracy were compromised due to this traditional method.
The Solution
In their search for a reliable solution to their problem, Pragati Engineering came across Altair’s Inspire Form through a vendor who was already using the software. The team was confident that simulation would play a crucial role in improving product quality and reducing the number of physical prototypes. They procured the Altair Solution and started using it for all their product lines. Altair Inspire Form proved to be a game-changer as it helped the team identify instances of failure, wrinkles, or cracks in sheet metal panel components right at the design stage. This breakthrough eliminated soft tool manufacturing and drastically reduced the number of physical trials. The solution not only reduced product development time but also increased design and output accuracy.
Operational Impact
Quantitative Benefit
Case Study missing?
Start adding your own!
Register with your work email and create a new case study profile for your business.
Related Case Studies.
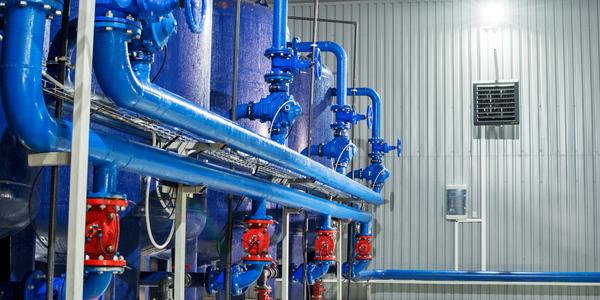
Case Study
Smart Water Filtration Systems
Before working with Ayla Networks, Ozner was already using cloud connectivity to identify and solve water-filtration system malfunctions as well as to monitor filter cartridges for replacements.But, in June 2015, Ozner executives talked with Ayla about how the company might further improve its water systems with IoT technology. They liked what they heard from Ayla, but the executives needed to be sure that Ayla’s Agile IoT Platform provided the security and reliability Ozner required.
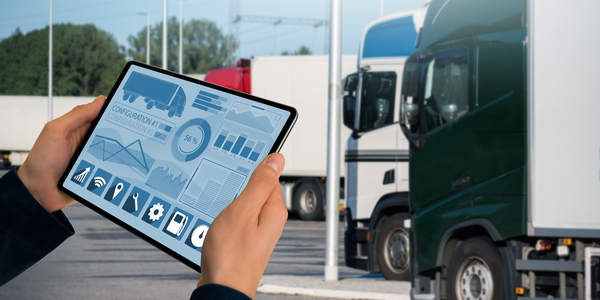
Case Study
IoT enabled Fleet Management with MindSphere
In view of growing competition, Gämmerler had a strong need to remain competitive via process optimization, reliability and gentle handling of printed products, even at highest press speeds. In addition, a digitalization initiative also included developing a key differentiation via data-driven services offers.
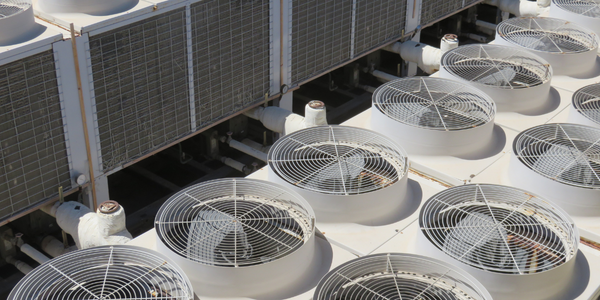
Case Study
Predictive Maintenance for Industrial Chillers
For global leaders in the industrial chiller manufacturing, reliability of the entire production process is of the utmost importance. Chillers are refrigeration systems that produce ice water to provide cooling for a process or industrial application. One of those leaders sought a way to respond to asset performance issues, even before they occur. The intelligence to guarantee maximum reliability of cooling devices is embedded (pre-alarming). A pre-alarming phase means that the cooling device still works, but symptoms may appear, telling manufacturers that a failure is likely to occur in the near future. Chillers who are not internet connected at that moment, provide little insight in this pre-alarming phase.
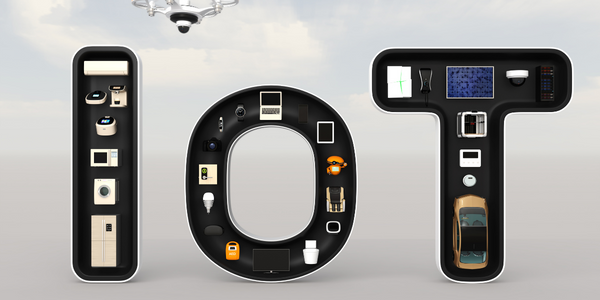
Case Study
Premium Appliance Producer Innovates with Internet of Everything
Sub-Zero faced the largest product launch in the company’s history:It wanted to launch 60 new products as scheduled while simultaneously opening a new “greenfield” production facility, yet still adhering to stringent quality requirements and manage issues from new supply-chain partners. A the same time, it wanted to increase staff productivity time and collaboration while reducing travel and costs.
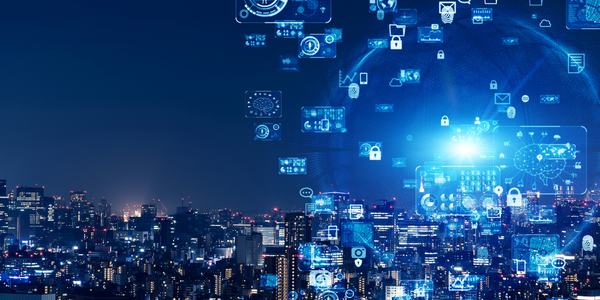
Case Study
Integration of PLC with IoT for Bosch Rexroth
The application arises from the need to monitor and anticipate the problems of one or more machines managed by a PLC. These problems, often resulting from the accumulation over time of small discrepancies, require, when they occur, ex post technical operations maintenance.
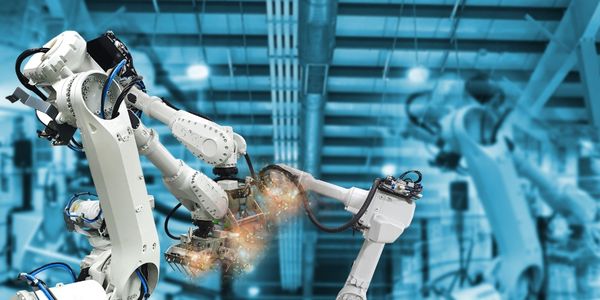
Case Study
Robot Saves Money and Time for US Custom Molding Company
Injection Technology (Itech) is a custom molder for a variety of clients that require precision plastic parts for such products as electric meter covers, dental appliance cases and spools. With 95 employees operating 23 molding machines in a 30,000 square foot plant, Itech wanted to reduce man hours and increase efficiency.