Customer Company Size
Mid-size Company
Region
- America
Country
- Canada
- United States
Product
- QlikView
Tech Stack
- JD Edwards One World ERP system
- EDI
Implementation Scale
- Enterprise-wide Deployment
Impact Metrics
- Cost Savings
- Productivity Improvements
- Customer Satisfaction
Technology Category
- Analytics & Modeling - Real Time Analytics
Applicable Functions
- Sales & Marketing
- Business Operation
Use Cases
- Supply Chain Visibility
- Inventory Management
- Demand Planning & Forecasting
Services
- Data Science Services
About The Customer
Art In Motion is a Canadian-based leading international fine art publisher and wholesaler framer of innovative wall decor. The company has showrooms throughout North America and an international network of distributors, delivering products to customers in more than 70 countries. Established in 1985, Art In Motion has experienced rapid sales growth with revenues increasing from approximately $50 million in 2001 to $86 million in 2004. The company is organized into four separate sales channels: national, regional, international, and licensing. Each department needs to look at data differently ranging from products, artists, art category, account, sales representative, and more.
The Challenge
Art In Motion, a leading international fine art publisher and wholesaler framer of innovative wall decor, was facing challenges due to its rapid growth. The company installed JD Edwards One World ERP system in 2002 to automate and streamline its business processes. However, the resulting data was overwhelming and the company needed better access to and distribution of data. With varied product lines and four distinct channels of distribution, Art In Motion required easy access to real-time, front-line analysis of sales, inventory, and distribution. The company began its business intelligence initiative and evaluated several solutions before selecting QlikView.
The Solution
Art In Motion selected QlikView because it was easy to build and deploy powerful applications at a far lower cost without the need for external consulting resources. Moreover, QlikView’s graphics and “one click” drill down capabilities made it easy to learn and use. They started with sales analysis and created a series of queries that looks at all types of sales data according to the various criteria, drilling down to territory, customer or a line item on an invoice. The company also used QlikView to track fulfillment and to reduce raw inventory levels by deciding to eliminate one of its warehouses within nine months. They built a supply chain application in QlikView that gave the production team a six-month look-back at demand usage of raw materials and a six-week look forward at the coming orders to determine the right levels of buffer stock to maintain.
Operational Impact
Quantitative Benefit
Case Study missing?
Start adding your own!
Register with your work email and create a new case study profile for your business.
Related Case Studies.
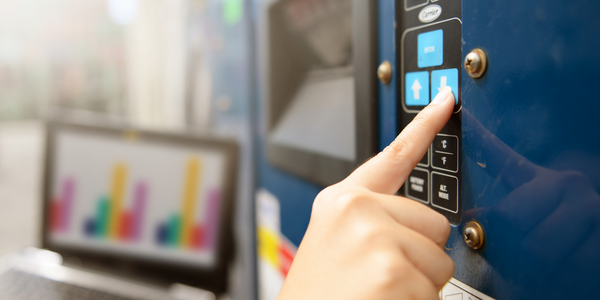
Case Study
Remote Temperature Monitoring of Perishable Goods Saves Money
RMONI was facing temperature monitoring challenges in a cold chain business. A cold chain must be established and maintained to ensure goods have been properly refrigerated during every step of the process, making temperature monitoring a critical business function. Manual registration practice can be very costly, labor intensive and prone to mistakes.
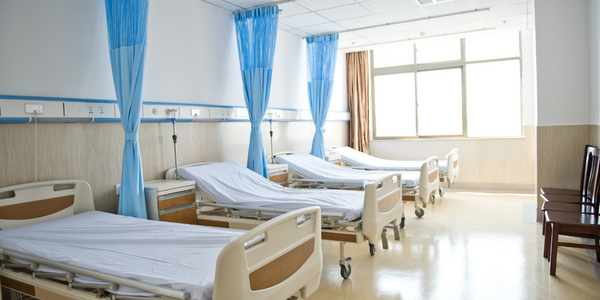
Case Study
Hospital Inventory Management
The hospital supply chain team is responsible for ensuring that the right medical supplies are readily available to clinicians when and where needed, and to do so in the most efficient manner possible. However, many of the systems and processes in use at the cancer center for supply chain management were not best suited to support these goals. Barcoding technology, a commonly used method for inventory management of medical supplies, is labor intensive, time consuming, does not provide real-time visibility into inventory levels and can be prone to error. Consequently, the lack of accurate and real-time visibility into inventory levels across multiple supply rooms in multiple hospital facilities creates additional inefficiency in the system causing over-ordering, hoarding, and wasted supplies. Other sources of waste and cost were also identified as candidates for improvement. Existing systems and processes did not provide adequate security for high-cost inventory within the hospital, which was another driver of cost. A lack of visibility into expiration dates for supplies resulted in supplies being wasted due to past expiry dates. Storage of supplies was also a key consideration given the location of the cancer center’s facilities in a dense urban setting, where space is always at a premium. In order to address the challenges outlined above, the hospital sought a solution that would provide real-time inventory information with high levels of accuracy, reduce the level of manual effort required and enable data driven decision making to ensure that the right supplies were readily available to clinicians in the right location at the right time.