Technology Category
- Analytics & Modeling - Digital Twin / Simulation
- Robots - Autonomous Guided Vehicles (AGV)
Applicable Industries
- Automotive
- Transportation
Applicable Functions
- Product Research & Development
Use Cases
- Transportation Simulation
- Vehicle Performance Monitoring
Services
- Testing & Certification
About The Customer
Arcimoto is a company that was founded in 2007 with the goal of catalyzing a shift towards a sustainable transportation system. The name Arcimoto means 'Future I Drive', reflecting their aspiration to develop new technologies and patterns of mobility that enhance environmental efficiency, sustainability, and affordability. They began work on the SRK Generation 8, an all-electric commuter vehicle, in January 2015. This Fun Utility Vehicle (FUV) combines the fun-factor and efficiency of a motorcycle with the stability and protection of a car, offering a unique transportation option for urban dwellers. The FUV boasts 230MPGe and can reach top speeds of 80mph.
The Challenge
Arcimoto, a company founded in 2007 with the mission to build sustainable transportation systems, faced a challenge in creating an optimized platform for their Fun Utility Vehicle (FUV). The FUV was designed to be a three-wheeled, all-electric commuter vehicle that combined the fun-factor and efficiency of a motorcycle with the stability and protection of a car. The challenges included creating a space frame enclosure for protection, a rear swing arm that could handle load requirements, and maintaining the visual design of the vehicle. As a start-up, Arcimoto also faced budget constraints and the pressure to generate interest in the marketplace and among investors. The engineering team had to ensure the vehicle was strong enough to withstand road conditions, and they also wanted to adhere to cross-industry safety tests, such as the roof crush test, to instill confidence in their product.
The Solution
Arcimoto used Altair's HyperMesh and RADIOSS software to overcome their design and safety challenges. HyperMesh provided an environment for rapid model generation, allowing Arcimoto to perform analysis in OptiStruct in a time-efficient manner. This helped them evaluate the strength of different parts of the FUV, such as the rear swing-arm, and validate their decision to use tubular materials for the design. For the roof crush analysis, the team used HyperMesh to model a complex roll cage and RADIOSS to perform the simulations. This allowed them to test different thicknesses and compare against a baseline, giving them confidence in their design's ability to withstand the weight of the test. The use of these software tools enabled Arcimoto to achieve repeatable and accurate results, reduce simulation cycle times, and evaluate multiple design scenarios, leading to better design decisions.
Operational Impact
Quantitative Benefit
Case Study missing?
Start adding your own!
Register with your work email and create a new case study profile for your business.
Related Case Studies.
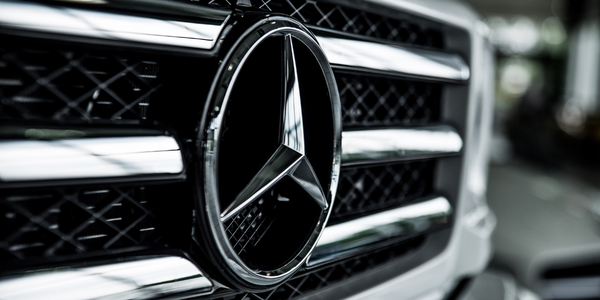
Case Study
Integral Plant Maintenance
Mercedes-Benz and his partner GAZ chose Siemens to be its maintenance partner at a new engine plant in Yaroslavl, Russia. The new plant offers a capacity to manufacture diesel engines for the Russian market, for locally produced Sprinter Classic. In addition to engines for the local market, the Yaroslavl plant will also produce spare parts. Mercedes-Benz Russia and his partner needed a service partner in order to ensure the operation of these lines in a maintenance partnership arrangement. The challenges included coordinating the entire maintenance management operation, in particular inspections, corrective and predictive maintenance activities, and the optimizing spare parts management. Siemens developed a customized maintenance solution that includes all electronic and mechanical maintenance activities (Integral Plant Maintenance).
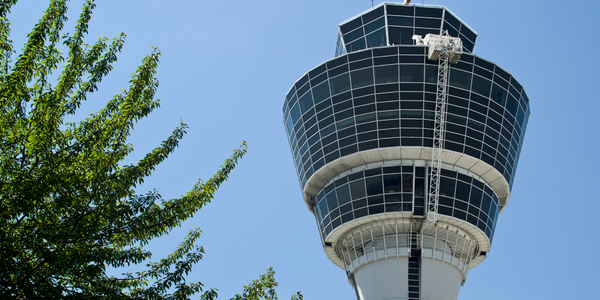
Case Study
Airport SCADA Systems Improve Service Levels
Modern airports are one of the busiest environments on Earth and rely on process automation equipment to ensure service operators achieve their KPIs. Increasingly airport SCADA systems are being used to control all aspects of the operation and associated facilities. This is because unplanned system downtime can cost dearly, both in terms of reduced revenues and the associated loss of customer satisfaction due to inevitable travel inconvenience and disruption.
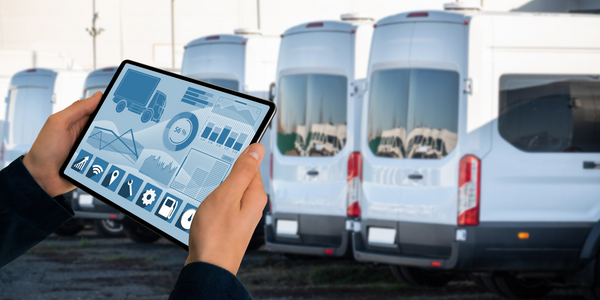
Case Study
IoT-based Fleet Intelligence Innovation
Speed to market is precious for DRVR, a rapidly growing start-up company. With a business model dependent on reliable mobile data, managers were spending their lives trying to negotiate data roaming deals with mobile network operators in different countries. And, even then, service quality was a constant concern.
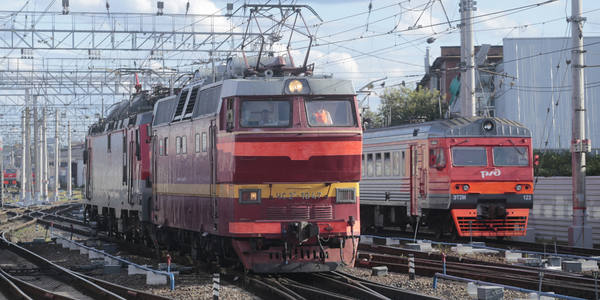
Case Study
Digitize Railway with Deutsche Bahn
To reduce maintenance costs and delay-causing failures for Deutsche Bahn. They need manual measurements by a position measurement system based on custom-made MEMS sensor clusters, which allow autonomous and continuous monitoring with wireless data transmission and long battery. They were looking for data pre-processing solution in the sensor and machine learning algorithms in the cloud so as to detect critical wear.