Technology Category
- Analytics & Modeling - Process Analytics
- Analytics & Modeling - Robotic Process Automation (RPA)
Applicable Industries
- Automotive
Applicable Functions
- Product Research & Development
- Quality Assurance
Use Cases
- Leasing Finance Automation
- Material Handling Automation
Services
- Testing & Certification
About The Customer
OPEL is a renowned automotive Original Equipment Manufacturer (OEM) that operates globally. The company is known for its innovative approach to design and manufacturing, constantly seeking ways to improve efficiency and productivity. OPEL is committed to delivering high-quality products to its customers, and as such, is always looking for ways to optimize its processes. The company identified the design process of engine mount systems as a potential area for process automation, with the aim of reducing computer aided engineering (CAE) cycle times, capturing and reusing knowledge in a standardized workflow, and quickly improving the final product quality.
The Challenge
Automotive Original Equipment Manufacturers (OEMs) globally are grappling with the challenge of reducing computer aided engineering (CAE) cycle times. This is due to an increasing number of car variants, a surge in data volume, and intense competitive pressure. OPEL, in response to these challenges, identified the design process of engine mount systems as a potential area for process automation. The objective was to enable NVH engineers to generate input decks even without detailed load case information. The knowledge had to be captured and reused in a standardized workflow. Additionally, automatic optimization and robustness analysis of the mount parameters had to be integrated into the process to quickly improve the final product quality.
The Solution
Altair ProductDesign’s process automation team developed a customized automation solution for OPEL, named 'Engine Mount Studio', using HyperWorks’ modular automation framework. The Engine Mount Studio guides the engineer through the process of data collection and management, analysis setup and run, post-processing, and parameter optimization. The user inputs desired load case combinations and vehicle variants, as well as properties of the mount. Within the optimization module, parameters like mount positions and properties can be optimized. The solution is currently being used in production in midsized and small car projects by CAE and test engineers.
Operational Impact
Case Study missing?
Start adding your own!
Register with your work email and create a new case study profile for your business.
Related Case Studies.
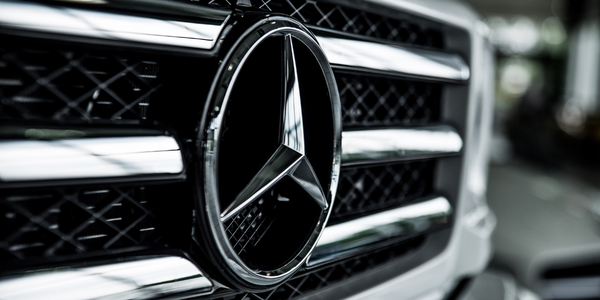
Case Study
Integral Plant Maintenance
Mercedes-Benz and his partner GAZ chose Siemens to be its maintenance partner at a new engine plant in Yaroslavl, Russia. The new plant offers a capacity to manufacture diesel engines for the Russian market, for locally produced Sprinter Classic. In addition to engines for the local market, the Yaroslavl plant will also produce spare parts. Mercedes-Benz Russia and his partner needed a service partner in order to ensure the operation of these lines in a maintenance partnership arrangement. The challenges included coordinating the entire maintenance management operation, in particular inspections, corrective and predictive maintenance activities, and the optimizing spare parts management. Siemens developed a customized maintenance solution that includes all electronic and mechanical maintenance activities (Integral Plant Maintenance).

Case Study
Monitoring of Pressure Pumps in Automotive Industry
A large German/American producer of auto parts uses high-pressure pumps to deburr machined parts as a part of its production and quality check process. They decided to monitor these pumps to make sure they work properly and that they can see any indications leading to a potential failure before it affects their process.