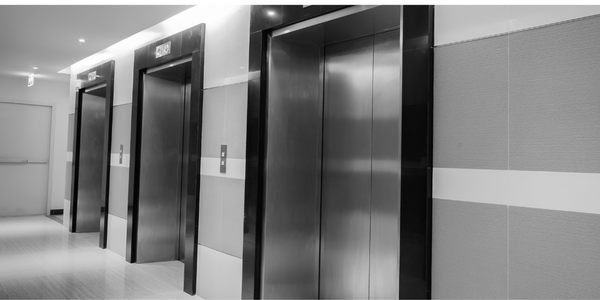
- Analytics & Modeling - Predictive Analytics
- Functional Applications - Remote Monitoring & Control Systems
- Platform as a Service (PaaS) - Connectivity Platforms
- Platform as a Service (PaaS) - Data Management Platforms
- Equipment & Machinery
- Maintenance
- Predictive Maintenance
KONE already provided traditional maintenance services for its more than 400,000 building owner and facilities management customers, but it sought cloud-based analytics technology to capture and use the vast amount of data generated by its elevator and escalator equipment worldwide to transform its service offerings. “We knew that digitalization was changing the industry, and we wanted to become a forerunner, not a follower in this development,” says Markus Huuskonen, the Director of Maintenance Processes and Connected Services at KONE.
KONE chose the IBM Watson IoT Platform running on an IBM Cloud platform to connect, remotely monitor and optimize managing more than 1.1 million elevators and escalators worldwide.
Connecting all that equipment to IBM Watson IoT is a game changer, according to Huuskonen. “We have real-time visibility into what’s happening, and we are then providing that visibility to our customers so that they have more information available. That makes their job easier, especially with their own customers, who are users of the equipment or tenants in the building.”
Analytics embedded in the solution can predict equipment condition, thereby helping KONE customers better manage their equipment over its lifecycle. For example, instead of requiring a customer to call for a service engineer after an equipment breakdown, the solution helps KONE see imminent problems in real-time, quickly dispatching a technician to resolve issues before they can cause system malfunctions or interruptions. In other words, KONE can fix things before they break.
Case Study missing?
Start adding your own!
Register with your work email and create a new case study profile for your business.
Related Case Studies.
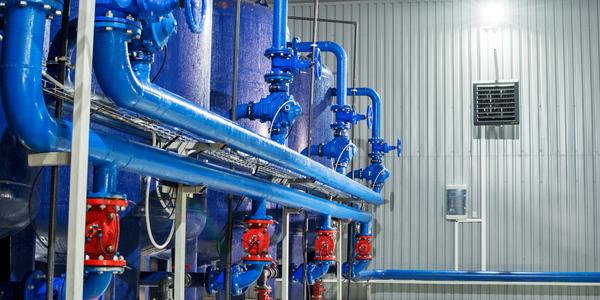
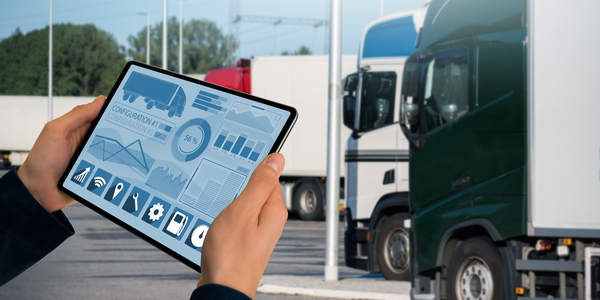
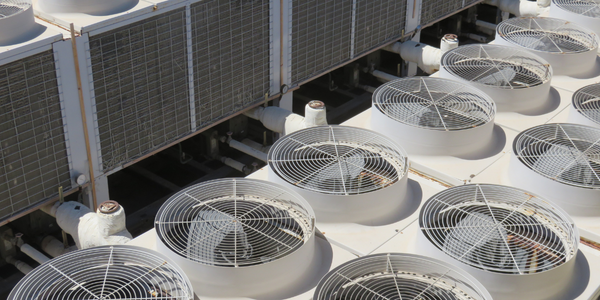
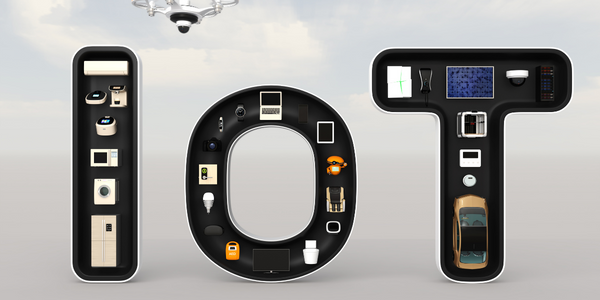
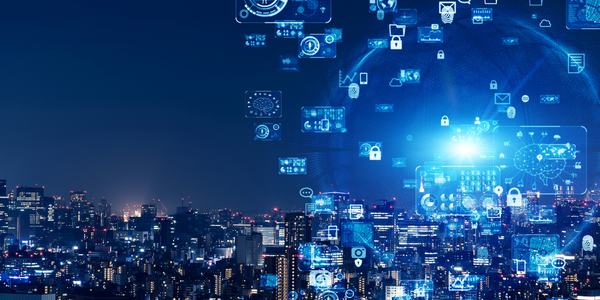
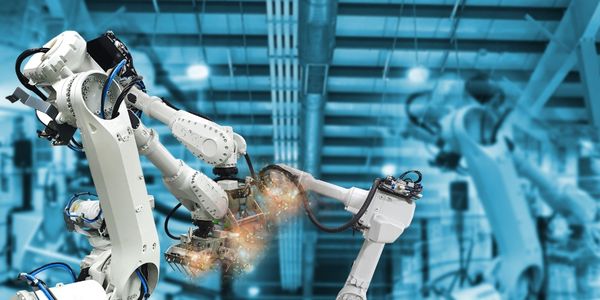