Technology Category
- Analytics & Modeling - Digital Twin / Simulation
- Functional Applications - Manufacturing Execution Systems (MES)
Applicable Industries
- Automotive
- Life Sciences
Applicable Functions
- Product Research & Development
- Quality Assurance
Use Cases
- Additive Manufacturing
- Manufacturing Process Simulation
Services
- Testing & Certification
About The Customer
LEIBER Group is a company that specializes in the design and production of lightweight metal components. With over 750 employees at its two locations in Europe, LEIBER works with many customers worldwide to use groundbreaking new methods to create lighter parts and products. The company is known for its innovative approach to design and manufacturing, and it has a strong commitment to meeting the evolving needs of the automotive industry. A recent project required LEIBER to redesign a component for a commercial vehicle, demonstrating the company's ability to respond to specific customer requirements and industry trends.
The Challenge
LEIBER Group, a company specializing in the design and production of lightweight metal components, faced a challenge in redesigning a suspension beam for a commercial vehicle. The original part was made of cast iron, but the customer required a lighter yet equally strong component. This challenge was set against the backdrop of the automotive industry's conflicting demands: vehicles need to be lighter to reduce fuel consumption and CO2 emissions, but they also need to be safe, reliable, and competitively priced. For many years, weight reduction was not a primary development goal, leading to heavier vehicles due to new systems that increase safety, comfort, and driving experience. The industry is now seeking new approaches and methodologies to realize optimal lightweight structures.
The Solution
LEIBER Group used solidThinking Inspire and a new material, AluXtrem®, a high tensile forgeable alloy, to design the new component. The engineers defined a design space, added load and boundary conditions, and ran an optimization to generate the ideal structural part. This simulation-driven design process allowed them to create structurally efficient concepts quickly and easily, using material only where it was actually needed. The resulting components were lighter and stiffer than traditionally designed components. To further improve the component’s performance and especially its weight, LEIBER combined the simulation-driven design approach with the use of new materials. AluXtrem® was used in the development and production of the new suspension beam, which was 50 percent lighter than the previously used cast iron component.
Operational Impact
Quantitative Benefit
Case Study missing?
Start adding your own!
Register with your work email and create a new case study profile for your business.
Related Case Studies.
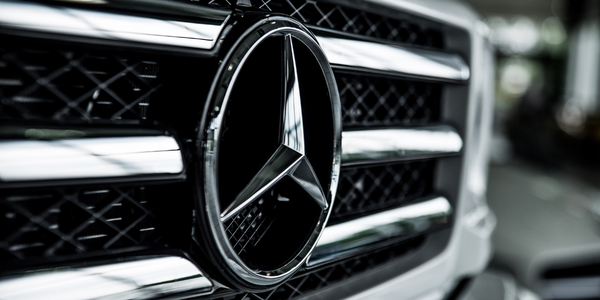
Case Study
Integral Plant Maintenance
Mercedes-Benz and his partner GAZ chose Siemens to be its maintenance partner at a new engine plant in Yaroslavl, Russia. The new plant offers a capacity to manufacture diesel engines for the Russian market, for locally produced Sprinter Classic. In addition to engines for the local market, the Yaroslavl plant will also produce spare parts. Mercedes-Benz Russia and his partner needed a service partner in order to ensure the operation of these lines in a maintenance partnership arrangement. The challenges included coordinating the entire maintenance management operation, in particular inspections, corrective and predictive maintenance activities, and the optimizing spare parts management. Siemens developed a customized maintenance solution that includes all electronic and mechanical maintenance activities (Integral Plant Maintenance).

Case Study
Monitoring of Pressure Pumps in Automotive Industry
A large German/American producer of auto parts uses high-pressure pumps to deburr machined parts as a part of its production and quality check process. They decided to monitor these pumps to make sure they work properly and that they can see any indications leading to a potential failure before it affects their process.