Technology Category
- Functional Applications - Warehouse Management Systems (WMS)
- Platform as a Service (PaaS) - Application Development Platforms
Applicable Industries
- Automotive
- Cement
Applicable Functions
- Warehouse & Inventory Management
Use Cases
- Picking, Sorting & Positioning
- Time Sensitive Networking
Services
- Cloud Planning, Design & Implementation Services
- System Integration
About The Customer
MyCamper is a Swiss start-up founded in 2015 by Michele Matt. The company operates as a platform for the rental of recreational vehicles and campervans, connecting vehicle owners with holidaymakers looking to rent. The idea for the business was born out of the founder's frustration at having his campervan unused in the driveway for 90% of the year. MyCamper quickly grew to become the Airbnb of the campervan/RV community. The company recognized the importance of data collected on its web platform from the start and sought to leverage this data to improve its services and operations.
The Challenge
MyCamper, a Swiss start-up likened to the Airbnb of campervans, faced a significant challenge in managing and analyzing the data collected on its web platform. The company recognized the importance of this data, but initial attempts at analytics were laborious and time-consuming, involving manual extraction of data from Excel spreadsheets. Using Google Analytics proved to be easier but was limited in scope. As an early-stage start-up, MyCamper had more pressing priorities and lacked the in-house skills to manually build out data pipelines. This resulted in a gap in data analytics that needed to be filled. The company also struggled with historicizing data in a way that could be retrieved for analysis. They were unable to track specific data sets, compare historical data to present, or even have a comparable baseline.
The Solution
MyCamper partnered with BI Concepts to develop a modernized analytics cloud platform that could ingest data from multiple sources into a centralized data warehouse for analytics. BI Concepts introduced Tableau to surface insights and Snowflake as a cloud data warehouse. This allowed for a central repository where data could be transformed using Fivetran Transformations and prepared for reporting. Fivetran was used to manage data delivery from source to destination, ensuring MyCamper's data is always accurate and up to date in Snowflake. Fivetran Transformations simplified the process, providing an instant snapshot of the camper owner database to know what campers were available for rent on their site and which campers were booked. Data is sourced primarily from MySQL, MyCamper’s transactional database, and Salesforce, which holds customer information. The next phase is to analyze additional accounting data, using Fivetran to connect sources to their data warehouse to answer questions pertaining to Financial Analytics.
Operational Impact
Quantitative Benefit
Case Study missing?
Start adding your own!
Register with your work email and create a new case study profile for your business.
Related Case Studies.
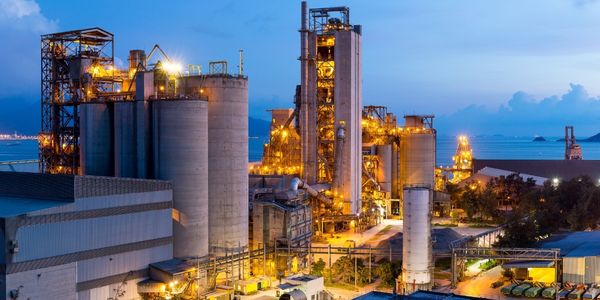
Case Study
System 800xA at Indian Cement Plants
Chettinad Cement recognized that further efficiencies could be achieved in its cement manufacturing process. It looked to investing in comprehensive operational and control technologies to manage and derive productivity and energy efficiency gains from the assets on Line 2, their second plant in India.
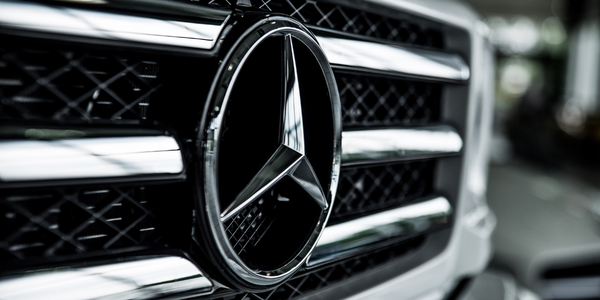
Case Study
Integral Plant Maintenance
Mercedes-Benz and his partner GAZ chose Siemens to be its maintenance partner at a new engine plant in Yaroslavl, Russia. The new plant offers a capacity to manufacture diesel engines for the Russian market, for locally produced Sprinter Classic. In addition to engines for the local market, the Yaroslavl plant will also produce spare parts. Mercedes-Benz Russia and his partner needed a service partner in order to ensure the operation of these lines in a maintenance partnership arrangement. The challenges included coordinating the entire maintenance management operation, in particular inspections, corrective and predictive maintenance activities, and the optimizing spare parts management. Siemens developed a customized maintenance solution that includes all electronic and mechanical maintenance activities (Integral Plant Maintenance).

Case Study
Monitoring of Pressure Pumps in Automotive Industry
A large German/American producer of auto parts uses high-pressure pumps to deburr machined parts as a part of its production and quality check process. They decided to monitor these pumps to make sure they work properly and that they can see any indications leading to a potential failure before it affects their process.