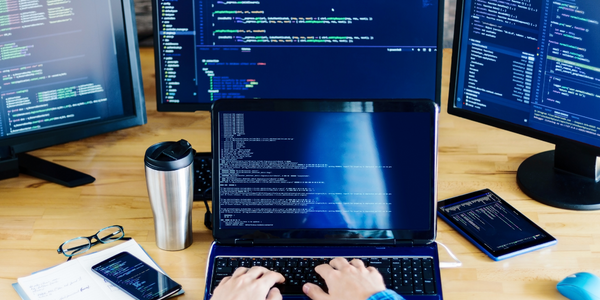
Technology Category
- Infrastructure as a Service (IaaS) - Backup & Recovery
Applicable Industries
- Automotive
About The Customer
The customer manufactures automobile filters which are subsequently distributed to spare parts businesses.
The Challenge
Tasks such as manual documentation and the fact that new software and hardware is constantly being integrated to the automation network makes the lives of maintenance staff difficult.
The Solution
Versiondog is an integrated data management system that can detect and document changes made to the production line network. Due to the high number of daily and weekly backups to the network, Versiondog ensures that the most recent software version is always running on every single component in the network, making maintenance work easier.
Data Collected
Backup, Change Management, Downtime, Inventory Levels, Maintenance Requirements
Operational Impact
Case Study missing?
Start adding your own!
Register with your work email and create a new case study profile for your business.
Related Case Studies.
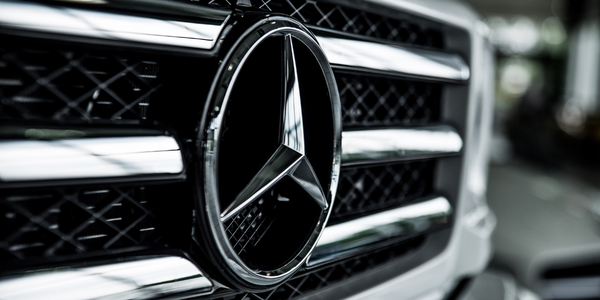
Case Study
Integral Plant Maintenance
Mercedes-Benz and his partner GAZ chose Siemens to be its maintenance partner at a new engine plant in Yaroslavl, Russia. The new plant offers a capacity to manufacture diesel engines for the Russian market, for locally produced Sprinter Classic. In addition to engines for the local market, the Yaroslavl plant will also produce spare parts. Mercedes-Benz Russia and his partner needed a service partner in order to ensure the operation of these lines in a maintenance partnership arrangement. The challenges included coordinating the entire maintenance management operation, in particular inspections, corrective and predictive maintenance activities, and the optimizing spare parts management. Siemens developed a customized maintenance solution that includes all electronic and mechanical maintenance activities (Integral Plant Maintenance).

Case Study
Monitoring of Pressure Pumps in Automotive Industry
A large German/American producer of auto parts uses high-pressure pumps to deburr machined parts as a part of its production and quality check process. They decided to monitor these pumps to make sure they work properly and that they can see any indications leading to a potential failure before it affects their process.