Technology Category
- Infrastructure as a Service (IaaS) - Cloud Computing
- Infrastructure as a Service (IaaS) - Private Cloud
Applicable Industries
- Apparel
- Automotive
Applicable Functions
- Procurement
- Product Research & Development
Use Cases
- Manufacturing Process Simulation
- Vehicle Performance Monitoring
Services
- Cloud Planning, Design & Implementation Services
- Hardware Design & Engineering Services
About The Customer
Mubea is a world-class global supplier of automotive lightweight components. In addition to chassis and motor components, Mubea is currently the only supplier for Tailor Rolled Blanks (TRB). Tailored rolling is a cold rolling process where the rolling nip is constantly varied in order to tailor the sheet thicknesses to meet the needs of an automotive Body in White (BIW) structure. Mubea supports its customers by identifying lightweight potentials in a vehicle, designing proper tailor rolled parts, and by conducting full light weight studies with full vehicle models with their own CAE resources. At Mubea, the engineers employ, amongst other tools, Altair’s HyperWorks CAE Suite to design and optimize parts.
The Challenge
Mubea, a global supplier of automotive lightweight components, is the only supplier for Tailor Rolled Blanks (TRB), a cold rolling process that tailors sheet thicknesses to meet the needs of an automotive Body in White (BIW) structure. The company supports its customers by identifying lightweight potentials in a vehicle, designing proper tailor rolled parts, and conducting full light weight studies with full vehicle models with their own CAE resources. However, the design optimization of Tailor Rolled Blanks is normally based on explicit dynamic simulations, also known as crash simulations. Due to the large size of these crash models, a single simulation run takes between one to twelve hours. Exploring different design concepts leads to various simulation runs and potential optimization, but due to the long run times, this becomes prohibitive and can easily exceed a project’s allotted time frame, which decreases innovations.
The Solution
To conduct all the simulation runs needed for assessment and evaluation of the different design concepts, Mubea uses high-performance computing (HPC) to complete an optimization task in the given time schedule. Mubea handles those simulations typically via their own local HyperWorks Unlimited™ (HWUL) Physical Appliance Cluster. HyperWorks Unlimited Physical Appliance is a private cloud solution with fully configured hardware and software, offering unlimited use of all Altair software within the appliance. This includes best-in-class application software, HPC workload management tools, and industry leading licensing and business model to meet the customer’s growing simulation needs. In the context of the HPC Challenge, HWUL Virtual Appliance was offered jointly with the solutions of Amazon Web Services (AWS) and Intel. The free use of Altair’s HWUL Virtual Appliance was supplemented by free credits from AWS.
Operational Impact
Quantitative Benefit
Case Study missing?
Start adding your own!
Register with your work email and create a new case study profile for your business.
Related Case Studies.
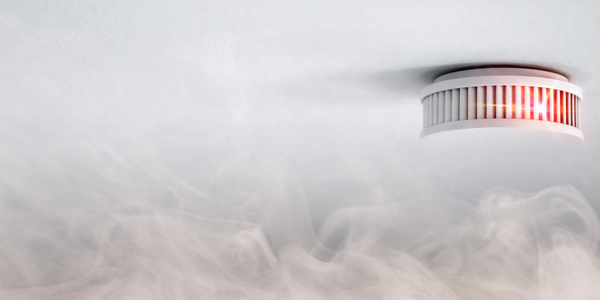
Case Study
Fire Alarm System and Remote Monitoring Sytem
Fire alarm systems are essential in providing an early warning in the event of fire. They help to save lives and protect property whilst also fulfilling the needs of insurance companies and government departments.Fire alarm systems typically consist of several inter-linked components, such as smoke detectors, heat detector, carbon monoxide, manual call points, sounders, alarm and buzzer. The fire alarm system should give immediate information in order to prevent the fire spread and protect live and property.To get maximum protection a shoe manufacturer in Indonesia opted for a new fire alarm system to monitor 13 production sites spread over 160 hectars. Although the company had an existing fire alarm system, it could not be monitored remotely.It was essential that the new system would be able to be monitored from a central control room. It needed to be able to connect to the existing smoke detector and manual call point. Information should be easily collected and passed on to the Supervisory Control and Data Acquisition (SCADA) system. Furthermore, the system should have several features such as alarm management, auto reporting, being connected to many client computers without additional cost, and run 24/7 without fails. The company also needed a system which could be implemented without changing the architecture of the existing fire alarm system.
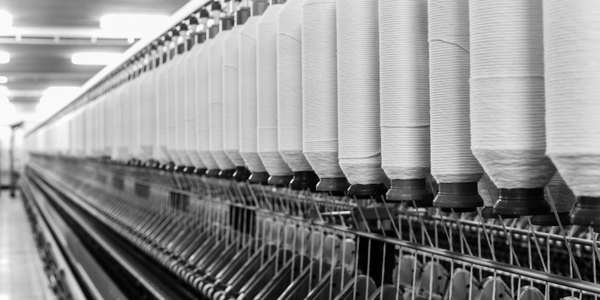
Case Study
IoT Applications and Upgrades in Textile Plant
At any given time, the textile company’s manufacturing facility has up to 2,000 textile carts in use. These carts are pushed from room to room, carrying materials or semi-finished products. Previously, a paper with a hand-written description was attached to each cart. This traditional method of processing made product tracking extremely difficult. Additionally, making sure that every cart of materials or semi-finished products went to its correct processing work station was also a problem. Therefore, the company desired an intelligent solution for tracking assets at their factories. They also wanted a solution that would help them collect process data so they could improve their manufacturing efficiency.
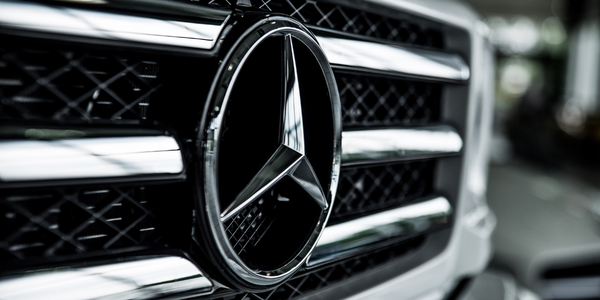
Case Study
Integral Plant Maintenance
Mercedes-Benz and his partner GAZ chose Siemens to be its maintenance partner at a new engine plant in Yaroslavl, Russia. The new plant offers a capacity to manufacture diesel engines for the Russian market, for locally produced Sprinter Classic. In addition to engines for the local market, the Yaroslavl plant will also produce spare parts. Mercedes-Benz Russia and his partner needed a service partner in order to ensure the operation of these lines in a maintenance partnership arrangement. The challenges included coordinating the entire maintenance management operation, in particular inspections, corrective and predictive maintenance activities, and the optimizing spare parts management. Siemens developed a customized maintenance solution that includes all electronic and mechanical maintenance activities (Integral Plant Maintenance).