技术
- 基础设施即服务 (IaaS) - 云计算
- 基础设施即服务 (IaaS) - 私有云
适用行业
- 服装
- 汽车
适用功能
- 采购
- 产品研发
用例
- 制造过程模拟
- 车辆性能监测
服务
- 云规划/设计/实施服务
- 硬件设计与工程服务
关于客户
Mubea是世界一流的汽车轻量化零部件全球供应商。除了底盘和电机部件外,Mubea 是目前唯一的拼焊板 (TRB) 供应商。定制轧制是一种冷轧工艺,其中轧制压区不断变化,以调整板材厚度以满足汽车白车身 (BIW) 结构的需求。 Mubea 通过识别车辆的轻量化潜力、设计适当的定制轧制零件以及利用自己的 CAE 资源对整车模型进行全面的轻量化研究来为客户提供支持。在 Mubea,工程师们使用 Altair 的 HyperWorks CAE Suite 等工具来设计和优化零件。
挑战
Mubea 是汽车轻量化零部件的全球供应商,也是定制轧制毛坯 (TRB) 的唯一供应商,TRB 是一种冷轧工艺,可定制板材厚度以满足汽车白车身 (BIW) 结构的需求。该公司通过识别车辆的轻量化潜力、设计适当的定制轧制零件以及利用自己的 CAE 资源对整车模型进行全面的轻量化研究来为客户提供支持。然而,拼焊板的设计优化通常基于显式动态模拟,也称为碰撞模拟。由于这些碰撞模型尺寸较大,单次模拟运行需要 1 到 12 小时。探索不同的设计概念会导致各种模拟运行和潜在的优化,但由于运行时间较长,这变得令人望而却步,并且很容易超出项目分配的时间范围,从而减少创新。
解决方案
为了进行评估和评价不同设计概念所需的所有模拟运行,Mubea 使用高性能计算 (HPC) 在给定的时间表内完成优化任务。 Mubea 通常通过其自己的本地 HyperWorks Unlimited™ (HWUL) 物理设备集群来处理这些模拟。 HyperWorks Unlimited 物理设备是一种私有云解决方案,具有完全配置的硬件和软件,可以无限制地使用设备内的所有 Altair 软件。这包括一流的应用软件、HPC 工作负载管理工具以及行业领先的许可和业务模型,以满足客户不断增长的模拟需求。在 HPC 挑战赛中,HWUL 虚拟设备与 Amazon Web Services (AWS) 和 Intel 的解决方案联合提供。除了免费使用 Altair 的 HWUL 虚拟设备外,AWS 还提供免费积分。
运营影响
数量效益
Case Study missing?
Start adding your own!
Register with your work email and create a new case study profile for your business.
相关案例.
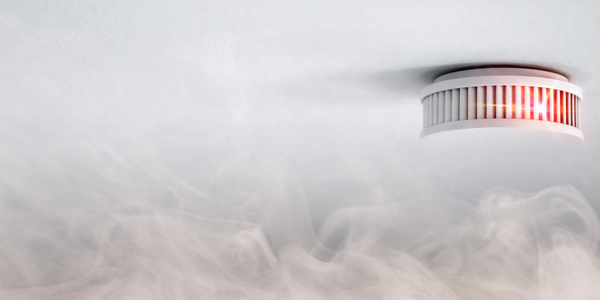
Case Study
Fire Alarm System and Remote Monitoring Sytem
Fire alarm systems are essential in providing an early warning in the event of fire. They help to save lives and protect property whilst also fulfilling the needs of insurance companies and government departments.Fire alarm systems typically consist of several inter-linked components, such as smoke detectors, heat detector, carbon monoxide, manual call points, sounders, alarm and buzzer. The fire alarm system should give immediate information in order to prevent the fire spread and protect live and property.To get maximum protection a shoe manufacturer in Indonesia opted for a new fire alarm system to monitor 13 production sites spread over 160 hectars. Although the company had an existing fire alarm system, it could not be monitored remotely.It was essential that the new system would be able to be monitored from a central control room. It needed to be able to connect to the existing smoke detector and manual call point. Information should be easily collected and passed on to the Supervisory Control and Data Acquisition (SCADA) system. Furthermore, the system should have several features such as alarm management, auto reporting, being connected to many client computers without additional cost, and run 24/7 without fails. The company also needed a system which could be implemented without changing the architecture of the existing fire alarm system.
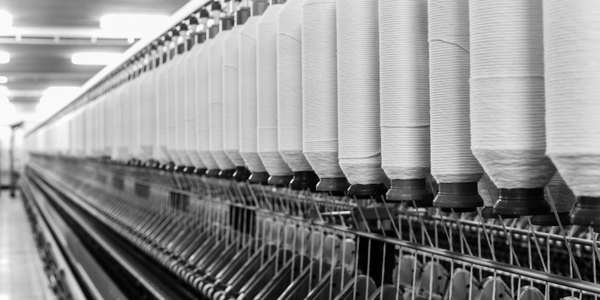
Case Study
IoT Applications and Upgrades in Textile Plant
At any given time, the textile company’s manufacturing facility has up to 2,000 textile carts in use. These carts are pushed from room to room, carrying materials or semi-finished products. Previously, a paper with a hand-written description was attached to each cart. This traditional method of processing made product tracking extremely difficult. Additionally, making sure that every cart of materials or semi-finished products went to its correct processing work station was also a problem. Therefore, the company desired an intelligent solution for tracking assets at their factories. They also wanted a solution that would help them collect process data so they could improve their manufacturing efficiency.
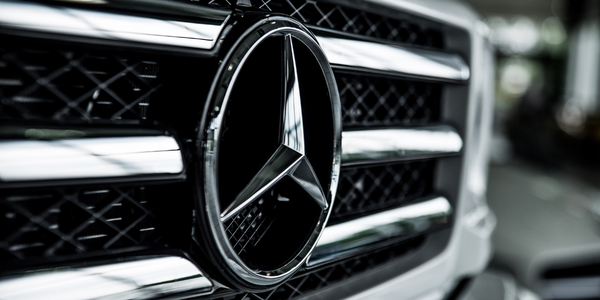
Case Study
Integral Plant Maintenance
Mercedes-Benz and his partner GAZ chose Siemens to be its maintenance partner at a new engine plant in Yaroslavl, Russia. The new plant offers a capacity to manufacture diesel engines for the Russian market, for locally produced Sprinter Classic. In addition to engines for the local market, the Yaroslavl plant will also produce spare parts. Mercedes-Benz Russia and his partner needed a service partner in order to ensure the operation of these lines in a maintenance partnership arrangement. The challenges included coordinating the entire maintenance management operation, in particular inspections, corrective and predictive maintenance activities, and the optimizing spare parts management. Siemens developed a customized maintenance solution that includes all electronic and mechanical maintenance activities (Integral Plant Maintenance).