Technology Category
- Infrastructure as a Service (IaaS) - Cloud Computing
Applicable Industries
- Agriculture
- Automotive
Applicable Functions
- Product Research & Development
Use Cases
- Farm Monitoring & Precision Farming
- Inventory Management
About The Customer
Chrysler is a leading automotive company that has been using computer simulation tools since the 1980s for designing cars and trucks. Over the years, the use of computer-aided engineering and finite element analysis has become a crucial enabler for Chrysler designers. The company has a High-Performance Computing (HPC) center with a processor count of 1,544-cores, all managed by PBS Professional. Chrysler runs a variety of simulations including impact simulations, noise, vibration, and harshness studies, and computational fluid dynamics using a variety of commercial packages. The HPC operation is central to the engineering design process as CAE is involved at every stage. The company has 300 CAE engineers worldwide who feed jobs to the HPC resources through PBS Professional.
The Challenge
Chrysler, a renowned automotive company, was facing a challenge in managing its growing Computer-Aided Engineering (CAE) server farm. Since the 1980s, Chrysler has been using computer simulation tools for designing cars and trucks. Over the years, the use of computer-aided engineering and finite element analysis expanded, leading to a significant increase in the processor count at Chrysler’s High-Performance Computing (HPC) center. By the late 1990s, Chrysler was building up its HPC capacity to meet the growing demand for CAE simulations by installing a number of servers. Initially, Chrysler used a competitor's product for workload management. However, in 2003, they acquired 384 PBS Professional licenses to manage clusters used exclusively for computational fluid dynamics (CFD) jobs. By 2008, the HPC center was operating 10 servers from a mix of vendors using a variety of Intel and AMD chips running Red Hat or SUSE Linux. The core count on the server farm had increased to 1,544.
The Solution
Chrysler decided to move entirely to PBS Works, a strategic decision based partly on cost. Chrysler uses Altair HyperWorks tools for CAE, which run on their HPC systems. Altair’s licensing structure enabled Chrysler to leverage HyperWorks licenses and substantially reduce license costs for workload management software. Running all 1,544 cores on PBS Professional also produced an unforeseen benefit. The 384 cores originally managed by PBS Professional and dedicated to CFD applications did not share any workload with the rest of the server population. Chrysler runs impact simulations using the LS-DYNA solver; noise, vibration, and harshness (NVH) studies in NASTRAN and Abaqus; and CFD in a variety of commercial packages. The HPC operation is the heartbeat of engineering design because CAE is involved at every stage. Three hundred Chrysler CAE engineers, scattered around the world, feed jobs to the HPC resources through PBS Professional using a homegrown script interface.
Operational Impact
Quantitative Benefit
Case Study missing?
Start adding your own!
Register with your work email and create a new case study profile for your business.
Related Case Studies.
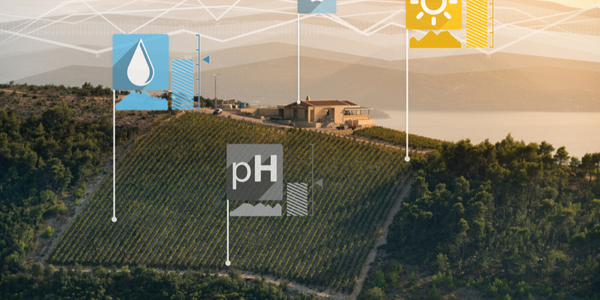
Case Study
Intelligent Farming with ThingWorx Analytics
Z Farms was facing three challenges: costly irrigation systems with water as a limited resource, narrow optimal ranges of soil moisture for growth with difficult maintenance and farm operators could not simply turn on irrigation systems like a faucet.
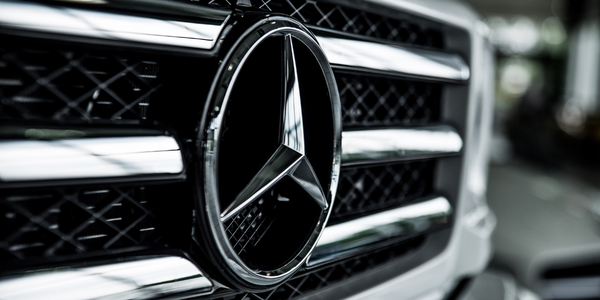
Case Study
Integral Plant Maintenance
Mercedes-Benz and his partner GAZ chose Siemens to be its maintenance partner at a new engine plant in Yaroslavl, Russia. The new plant offers a capacity to manufacture diesel engines for the Russian market, for locally produced Sprinter Classic. In addition to engines for the local market, the Yaroslavl plant will also produce spare parts. Mercedes-Benz Russia and his partner needed a service partner in order to ensure the operation of these lines in a maintenance partnership arrangement. The challenges included coordinating the entire maintenance management operation, in particular inspections, corrective and predictive maintenance activities, and the optimizing spare parts management. Siemens developed a customized maintenance solution that includes all electronic and mechanical maintenance activities (Integral Plant Maintenance).