Customer Company Size
Large Corporate
Region
- America
Country
- United States
Product
- Turvo’s Collaboration Cloud
- Turvo Analytics
- Turvo Integration Hub
- Turvo Driver App
- Turvo Inventory
Tech Stack
- SaaS platform
- APIs
Implementation Scale
- Enterprise-wide Deployment
Impact Metrics
- Cost Savings
- Productivity Improvements
- Customer Satisfaction
Technology Category
- Platform as a Service (PaaS) - Connectivity Platforms
- Analytics & Modeling - Real Time Analytics
Applicable Functions
- Logistics & Transportation
- Warehouse & Inventory Management
Use Cases
- Supply Chain Visibility
- Inventory Management
- Real-Time Location System (RTLS)
Services
- System Integration
- Software Design & Engineering Services
About The Customer
Port City Logistics is a fast-growing logistics service provider in the Port of Savannah area. Since late 2019, the company has evolved into one of North America’s premier logistics service providers. The company initially operated with limited resources, with only five thousand square feet of warehouse space, six employees, and five pickup trucks. However, it has since grown massively and is dedicated to providing absolute transparency and around-the-clock service. The company's growth and dedication to service required a robust technology platform that could provide the best experience and fully enable its operators, partners, carriers, and shipper-customers to plan, execute, settle and collaborate in real-time.
The Challenge
Port City Logistics, a logistics service provider in the Port of Savannah area, has been experiencing substantial growth since late 2019. The company aimed to connect with more shippers and turn away from being a pure commodity to a value-added partner. However, this required a new strategy that would involve connecting with more non-vessel-operating common carriers (NVOCCs), gaining more visibility into inventory levels at the warehouse, ensuring constant oversight and tracking of all trucks and documentation through an app-based experience, providing a secure information gateway for both carriers and shippers, and scaling operations without limits.
The Solution
Port City Logistics selected Turvo’s Collaboration Cloud to meet its needs. The Collaboration Cloud enables 100% visibility and real-time interaction with carriers, partners, and customers. It integrates and unifies Port City Logistics’ people, systems, data, and processes for complete shipment execution from one platform. Turvo’s unique architecture includes the industry’s most advanced SaaS platform with robust automation, APIs, exception management, and self-service integrations via its Integration Hub. Core features of the solution include Turvo Analytics for real-time carrier score carding, Turvo Integration Hub for integrating with multiple systems, Turvo Driver App for real-time communications with drivers, Turvo Inventory for visibility in warehouses, Turvo Appointment Scheduling for easy scheduling, Turvo Orders for configuring shipments after unloading containers, and Turvo Shipments for 24/7 track and trace of all shipments.
Operational Impact
Quantitative Benefit
Case Study missing?
Start adding your own!
Register with your work email and create a new case study profile for your business.
Related Case Studies.
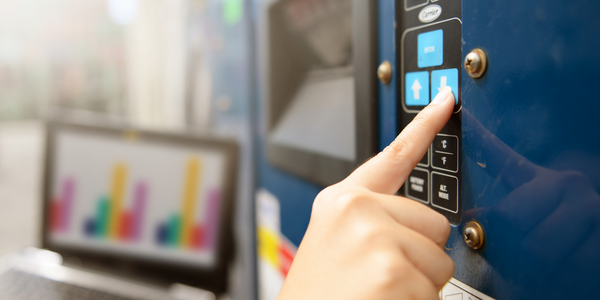
Case Study
Remote Temperature Monitoring of Perishable Goods Saves Money
RMONI was facing temperature monitoring challenges in a cold chain business. A cold chain must be established and maintained to ensure goods have been properly refrigerated during every step of the process, making temperature monitoring a critical business function. Manual registration practice can be very costly, labor intensive and prone to mistakes.
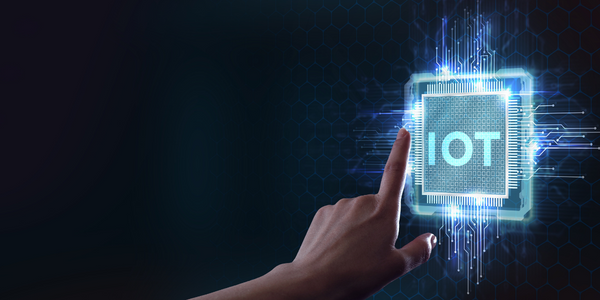
Case Study
Leading Tools Manufacturer Transforms Operations with IoT
Stanley Black & Decker required transparency of real-time overall equipment effectiveness and line productivity to reduce production line change over time.The goal was to to improve production to schedule, reduce actual labor costs and understanding the effects of shift changes and resource shifts from line to line.
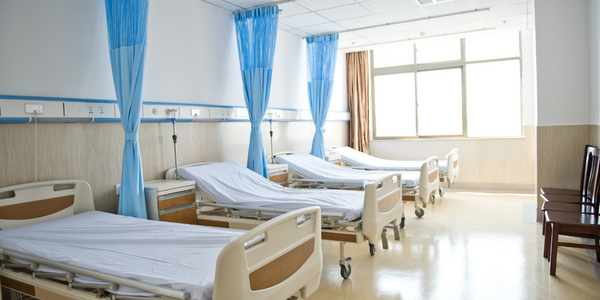
Case Study
Hospital Inventory Management
The hospital supply chain team is responsible for ensuring that the right medical supplies are readily available to clinicians when and where needed, and to do so in the most efficient manner possible. However, many of the systems and processes in use at the cancer center for supply chain management were not best suited to support these goals. Barcoding technology, a commonly used method for inventory management of medical supplies, is labor intensive, time consuming, does not provide real-time visibility into inventory levels and can be prone to error. Consequently, the lack of accurate and real-time visibility into inventory levels across multiple supply rooms in multiple hospital facilities creates additional inefficiency in the system causing over-ordering, hoarding, and wasted supplies. Other sources of waste and cost were also identified as candidates for improvement. Existing systems and processes did not provide adequate security for high-cost inventory within the hospital, which was another driver of cost. A lack of visibility into expiration dates for supplies resulted in supplies being wasted due to past expiry dates. Storage of supplies was also a key consideration given the location of the cancer center’s facilities in a dense urban setting, where space is always at a premium. In order to address the challenges outlined above, the hospital sought a solution that would provide real-time inventory information with high levels of accuracy, reduce the level of manual effort required and enable data driven decision making to ensure that the right supplies were readily available to clinicians in the right location at the right time.
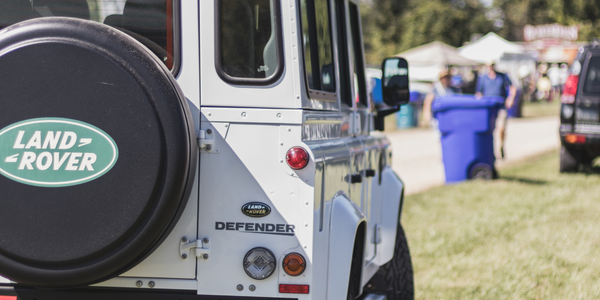
Case Study
Jaguar Land Rover Speeds Order-to-Cash Cycle
At Jaguar Land Rover, vehicles physically move around the facility for testing, configuration setting, rework and rectification, leading to a longer search time to get each vehicle to its next process facility. The main goal is to minimize the vehicles' dwell time between end of line and the delivery chain which was previously a manually intensive process. Jaguar Land Rover's goal was to build on the success of an earlier RFID project and improve the efficiency of delivering vehicles to meet dealer orders.