Technology Category
- Application Infrastructure & Middleware - Data Exchange & Integration
- Robots - Autonomous Guided Vehicles (AGV)
Applicable Industries
- Automotive
- Transportation
Applicable Functions
- Product Research & Development
- Quality Assurance
Use Cases
- Time Sensitive Networking
- Vehicle Performance Monitoring
Services
- System Integration
- Testing & Certification
About The Customer
The primary customer for this project was the Australian Defence Organization (ADO), which includes celebrated names such as the Capability Acquisition and Sustainment Group (CASG), Defence Science and Technology Group, Land Engineering Agency, Battlespace Communications and Operations Group, and the Joint Proof and Experimental Unit. The ADO is responsible for the procurement of defence equipment and services for the Australian Defence Force. In this case, the ADO had procured around 2,200 Mercedes-Benz G-Wagon light trucks for the Australian Army, and IDES was tasked with designing, building, and fitting all mission modules for these vehicles.
The Challenge
Integrated Design and Engineering Solutions (IDES), a Melbourne-based engineering product development and systems integration company, was tasked with a challenging assignment by the Australian Defence Organization (ADO). The project, known as LAND 121 Phase 3A, involved the procurement of around 2,200 Mercedes-Benz G-Wagon light trucks for the Australian Army. One of the variants of these vehicles was intended to be used as a surveillance and reconnaissance (S&R) vehicle. The IDES team was required to design a module for this vehicle that would provide adequate protection for the rear observer in the event of a vehicle rollover. The team decided to build a vehicle rollover protection structure (ROPS) in the form of a tubular roll cage structure. However, the traditional method of developing such a structure, which involves iterative physical testing, was deemed too time, effort, and cost-intensive for the project's tight timeline.
The Solution
To overcome the challenge of developing a robust ROPS within the project's tight timeline, the IDES team decided to leverage Altair HyperWorks, a computer-aided engineering (CAE) software suite that they had been using for many years. The team began by creating a finite element model of the pendulum test rig, base vehicle chassis, and S&R module using Altair HyperMesh. They then simulated the physical testing process using Altair Radioss and processed the results in Altair HyperView. This approach allowed the team to optimize the product structures and minimize the need for physical prototyping and testing required for product verification and validation. By using HyperWorks, the IDES team was able to quickly, efficiently, and accurately develop an optimum design for the ROPS.
Operational Impact
Quantitative Benefit
Case Study missing?
Start adding your own!
Register with your work email and create a new case study profile for your business.
Related Case Studies.
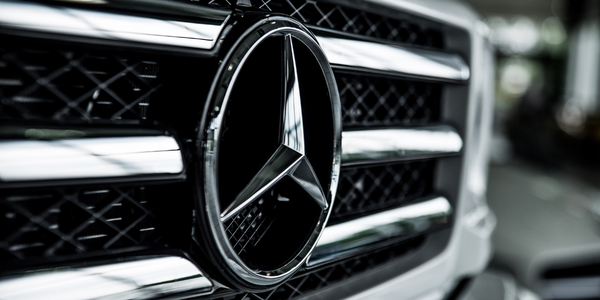
Case Study
Integral Plant Maintenance
Mercedes-Benz and his partner GAZ chose Siemens to be its maintenance partner at a new engine plant in Yaroslavl, Russia. The new plant offers a capacity to manufacture diesel engines for the Russian market, for locally produced Sprinter Classic. In addition to engines for the local market, the Yaroslavl plant will also produce spare parts. Mercedes-Benz Russia and his partner needed a service partner in order to ensure the operation of these lines in a maintenance partnership arrangement. The challenges included coordinating the entire maintenance management operation, in particular inspections, corrective and predictive maintenance activities, and the optimizing spare parts management. Siemens developed a customized maintenance solution that includes all electronic and mechanical maintenance activities (Integral Plant Maintenance).
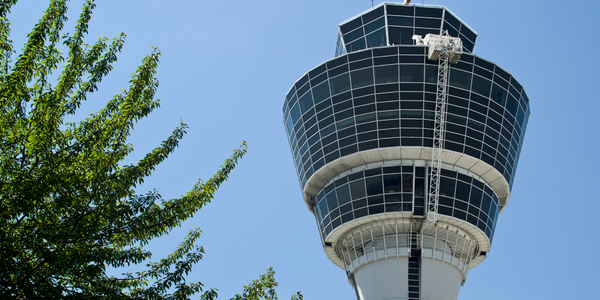
Case Study
Airport SCADA Systems Improve Service Levels
Modern airports are one of the busiest environments on Earth and rely on process automation equipment to ensure service operators achieve their KPIs. Increasingly airport SCADA systems are being used to control all aspects of the operation and associated facilities. This is because unplanned system downtime can cost dearly, both in terms of reduced revenues and the associated loss of customer satisfaction due to inevitable travel inconvenience and disruption.
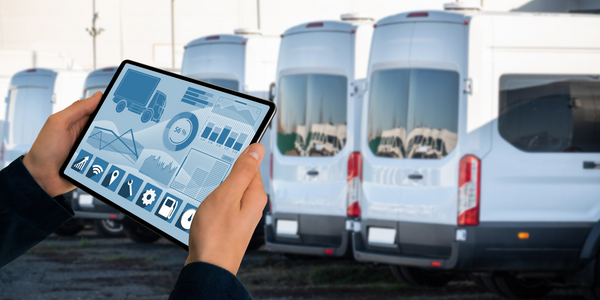
Case Study
IoT-based Fleet Intelligence Innovation
Speed to market is precious for DRVR, a rapidly growing start-up company. With a business model dependent on reliable mobile data, managers were spending their lives trying to negotiate data roaming deals with mobile network operators in different countries. And, even then, service quality was a constant concern.
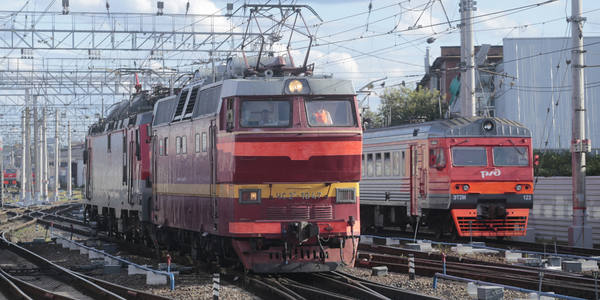
Case Study
Digitize Railway with Deutsche Bahn
To reduce maintenance costs and delay-causing failures for Deutsche Bahn. They need manual measurements by a position measurement system based on custom-made MEMS sensor clusters, which allow autonomous and continuous monitoring with wireless data transmission and long battery. They were looking for data pre-processing solution in the sensor and machine learning algorithms in the cloud so as to detect critical wear.