Technology Category
- Sensors - Autonomous Driving Sensors
- Sensors - Level Sensors
Applicable Industries
- Automotive
- Retail
Applicable Functions
- Sales & Marketing
Use Cases
- Retail Store Automation
- Visual Quality Detection
About The Customer
BMW Group Germany is a part of the globally renowned BMW brand, known for its automotive engineering excellence. The company produces 2.5 million vehicles annually, making it one of the largest commercial enterprises in Germany. At its national wholesale and retail business in Germany, BMW Group Germany uses data analytics to inform sales and marketing strategies, drive conversations with dealerships, and exceed KPIs at both national and regional levels. The company was seeking a solution to unify its disparate data systems and improve data consistency across the enterprise.
The Challenge
BMW Group Germany, one of the largest commercial enterprises in Germany, was facing significant data challenges. The company was dealing with multiple data sources, databases, and in-house systems, making it difficult to collate, analyze, and visualize information effectively. Employees were conducting their own isolated analytics and reporting, leading to data discrepancies. The senior leadership team recognized the need for a unified analytics platform that would provide a 360-degree view of data, support data-driven decision-making, and foster cross-functional synergies within the company.
The Solution
BMW Group Germany implemented Tableau as their overarching visual analytics solution. The back-end infrastructure was carefully designed to ensure seamless integration of Tableau with the existing systems. Tableau's automation features were particularly beneficial, allowing dashboards to be updated automatically with new data from different sources. This ensured that users always had access to the latest information for analysis. The ease of use of Tableau also enabled employees without a data background to quickly understand and use the platform. The company created a single automated dashboard to track KPIs at the senior executive level, allowing for in-depth analysis by car model, sales period, region, and more.
Operational Impact
Quantitative Benefit
Case Study missing?
Start adding your own!
Register with your work email and create a new case study profile for your business.
Related Case Studies.
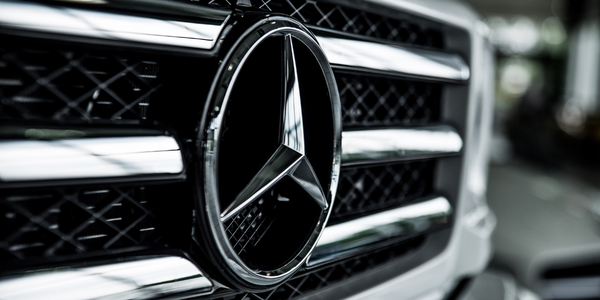
Case Study
Integral Plant Maintenance
Mercedes-Benz and his partner GAZ chose Siemens to be its maintenance partner at a new engine plant in Yaroslavl, Russia. The new plant offers a capacity to manufacture diesel engines for the Russian market, for locally produced Sprinter Classic. In addition to engines for the local market, the Yaroslavl plant will also produce spare parts. Mercedes-Benz Russia and his partner needed a service partner in order to ensure the operation of these lines in a maintenance partnership arrangement. The challenges included coordinating the entire maintenance management operation, in particular inspections, corrective and predictive maintenance activities, and the optimizing spare parts management. Siemens developed a customized maintenance solution that includes all electronic and mechanical maintenance activities (Integral Plant Maintenance).
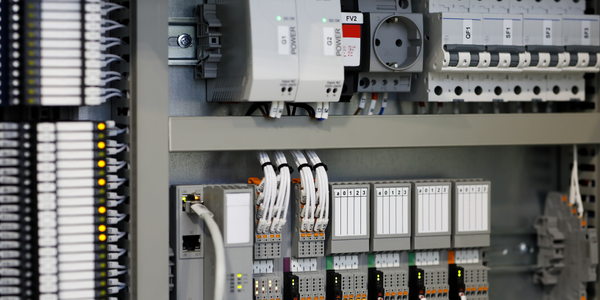
Case Study
Improving Production Line Efficiency with Ethernet Micro RTU Controller
Moxa was asked to provide a connectivity solution for one of the world's leading cosmetics companies. This multinational corporation, with retail presence in 130 countries, 23 global braches, and over 66,000 employees, sought to improve the efficiency of their production process by migrating from manual monitoring to an automatic productivity monitoring system. The production line was being monitored by ABB Real-TPI, a factory information system that offers data collection and analysis to improve plant efficiency. Due to software limitations, the customer needed an OPC server and a corresponding I/O solution to collect data from additional sensor devices for the Real-TPI system. The goal is to enable the factory information system to more thoroughly collect data from every corner of the production line. This will improve its ability to measure Overall Equipment Effectiveness (OEE) and translate into increased production efficiencies. System Requirements • Instant status updates while still consuming minimal bandwidth to relieve strain on limited factory networks • Interoperable with ABB Real-TPI • Small form factor appropriate for deployment where space is scarce • Remote software management and configuration to simplify operations