Technology Category
- Cybersecurity & Privacy - Identity & Authentication Management
Applicable Industries
- Automotive
Use Cases
- Livestock Monitoring
- Personnel Tracking & Monitoring
Services
- System Integration
- Training
About The Customer
Thrifty New Zealand is a car rental company owned by the National Roads and Motor Association (NRMA). The company operates across 30 locations with a workforce of around 150 staff members. A few years ago, Thrifty recognized the need to update their outdated, paper-based processes and upgrade their car rental management system. The company appointed a process champion to drive the process improvement efforts and ensure a smooth transition to the new system with minimal disruption to the teams.
The Challenge
Thrifty New Zealand, a car rental company owned by the National Roads and Motor Association (NRMA), was facing operational challenges due to outdated, paper-based processes. The company, with around 150 staff across 30 locations, recognized the need to upgrade their car rental management system. The existing system was not only time-consuming but also lacked easy access to processes for the staff. The management team understood the need for a process champion to drive process improvement efforts and appointed Jackie Reid for the role. The challenge was to ensure a smooth transition to the new car-rental system with minimum effort from the already-busy teams. The teams needed to understand what was changing and how that would impact them.
The Solution
Thrifty New Zealand implemented Nintex Promapp, a process management solution, to streamline their car rental operations. Jackie Reid, who had prior experience with Nintex Promapp, led the transition. The plan involved tagging all processes associated with the car-rental system within Nintex Promapp, allowing teams to identify which processes were affected by the system change. The Thrifty team conducted process discovery workshops with users and software vendors, dividing the processes between each area and examining how they would change post-implementation. Using the outcomes of these workshops, they updated each process to prepare for the system change. The entire process of replacing the car-rental system took just nine months, making it one of the most successful projects the company has undertaken.
Operational Impact
Quantitative Benefit
Case Study missing?
Start adding your own!
Register with your work email and create a new case study profile for your business.
Related Case Studies.
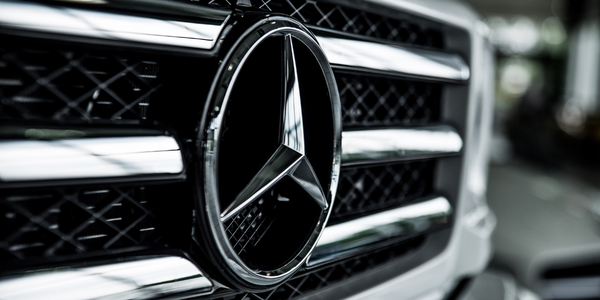
Case Study
Integral Plant Maintenance
Mercedes-Benz and his partner GAZ chose Siemens to be its maintenance partner at a new engine plant in Yaroslavl, Russia. The new plant offers a capacity to manufacture diesel engines for the Russian market, for locally produced Sprinter Classic. In addition to engines for the local market, the Yaroslavl plant will also produce spare parts. Mercedes-Benz Russia and his partner needed a service partner in order to ensure the operation of these lines in a maintenance partnership arrangement. The challenges included coordinating the entire maintenance management operation, in particular inspections, corrective and predictive maintenance activities, and the optimizing spare parts management. Siemens developed a customized maintenance solution that includes all electronic and mechanical maintenance activities (Integral Plant Maintenance).

Case Study
Monitoring of Pressure Pumps in Automotive Industry
A large German/American producer of auto parts uses high-pressure pumps to deburr machined parts as a part of its production and quality check process. They decided to monitor these pumps to make sure they work properly and that they can see any indications leading to a potential failure before it affects their process.