公司规模
Large Corporate
地区
- America
国家
- United States
产品
- AVEVA Intelligence
- AVEVA Workflow
- IntelaTrac
技术栈
- Data Warehousing
- Business Process Management
- RFID Equipment Tags
实施规模
- Enterprise-wide Deployment
影响指标
- Cost Savings
- Productivity Improvements
- Digital Expertise
技术
- 应用基础设施与中间件 - 数据交换与集成
- 应用基础设施与中间件 - 中间件、SDK 和库
适用功能
- 离散制造
- 质量保证
用例
- 自动化制造系统
- 预测性维护
- Condition Monitoring
服务
- 系统集成
- 软件设计与工程服务
关于客户
Ascend Performance Materials is a global leader in the production of Nylon 6,6, a type of nylon used in the production of textiles, carpet, and molded plastics. The company has four integrated manufacturing facilities located throughout the southeast region of the U.S. Ascend was behind the times in the implementation and use of modern technology to optimize its operations. The company had to access multiple software systems to manage day-to-day operations in an effective and secure manner. These systems generated large sets of data which contained critical information pertaining to management systems, planning and cost information in business systems and energy consumption.
挑战
Ascend Performance Materials, a global leader in the production of Nylon 6,6, was facing challenges in tracking data to ensure production efficiency and product quality. There was a lack of process consistency throughout the plants. The company was not leveraging modern technology to optimize its operations. Ascend operations had to access multiple software systems to manage day-to-day operations in an effective and secure manner. These systems generated large sets of data which contained critical information pertaining to management systems, planning and cost information in business systems and energy consumption. As a result, Ascend management was challenged with creating relevant reports reflecting performance measures in overall context of their operational process. The company’s previous process entailed collecting and analysing data manually which was not effective, since the information collected was generated after the fact, and was too complex for collaborative use across the organisation.
解决方案
Ascend Performance Materials implemented Mobile Operator Rounds combined with AVEVA Intelligence and Workflow to create a “Visual Factory” to improve its manufacturing operations. The company created a “Visual Factory” by combining Intelligence and Workflow, along with IntelaTrac to leverage key information data from multiple sources. Intelligence software addressed the challenges faced by Ascend to leverage the hidden insights in industrial data. The software automated the transformation of time series and transactional data across multiple sources and turned large amounts of industrial “big data” into actionable metrics and key performance indicator (KPI) information. Metrics and context data is kept in an open information model, providing a single version of the current data. This is stored in data warehouses and enterprise business intelligence tools enabling Ascend management to make strategic sense out of the production data. Ascend also implemented AVEVA Workflow software, an advanced workflow application that enables companies to digitise manual and automated processes that include people, equipment, and/or systems. Ascend also used IntelaTrac, a mobile workforce and decision support system that features configurable software and ruggedized mobile hardware solutions.
运营影响
数量效益
Case Study missing?
Start adding your own!
Register with your work email and create a new case study profile for your business.
相关案例.
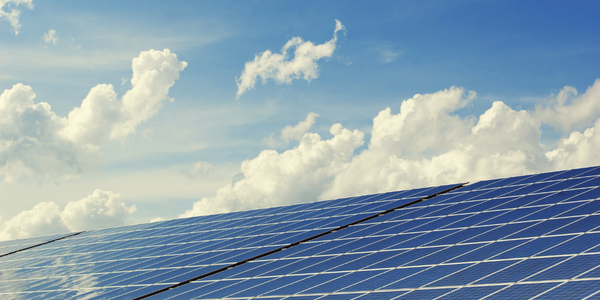
Case Study
Remote Monitoring & Predictive Maintenance App for a Solar Energy System
The maintenance & tracking of various modules was an overhead for the customer due to the huge labor costs involved. Being an advanced solar solutions provider, they wanted to ensure early detection of issues and provide the best-in-class customer experience. Hence they wanted to automate the whole process.
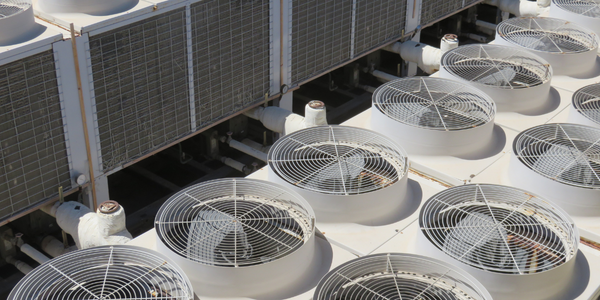
Case Study
Predictive Maintenance for Industrial Chillers
For global leaders in the industrial chiller manufacturing, reliability of the entire production process is of the utmost importance. Chillers are refrigeration systems that produce ice water to provide cooling for a process or industrial application. One of those leaders sought a way to respond to asset performance issues, even before they occur. The intelligence to guarantee maximum reliability of cooling devices is embedded (pre-alarming). A pre-alarming phase means that the cooling device still works, but symptoms may appear, telling manufacturers that a failure is likely to occur in the near future. Chillers who are not internet connected at that moment, provide little insight in this pre-alarming phase.
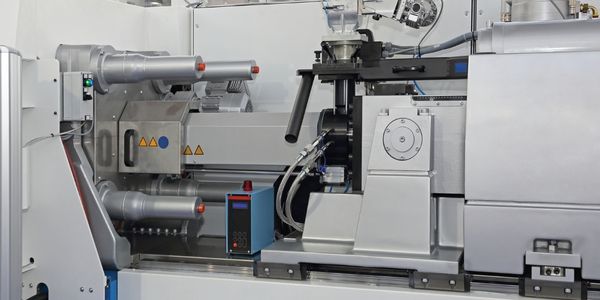
Case Study
Plastic Spoons Case study: Injection Moulding
In order to meet customer expectations by supplying a wide variety of packaging units, from 36 to 1000 spoons per package, a new production and packaging line needed to be built. DeSter wanted to achieve higher production capacity, lower cycle time and a high degree of operator friendliness with this new production line.
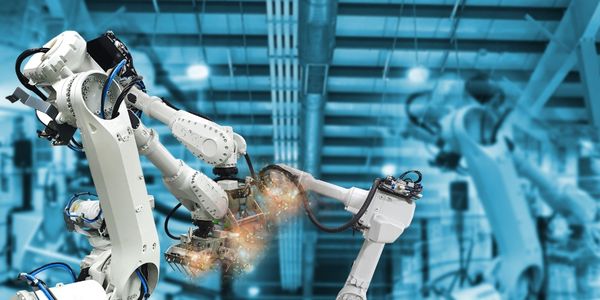
Case Study
Robot Saves Money and Time for US Custom Molding Company
Injection Technology (Itech) is a custom molder for a variety of clients that require precision plastic parts for such products as electric meter covers, dental appliance cases and spools. With 95 employees operating 23 molding machines in a 30,000 square foot plant, Itech wanted to reduce man hours and increase efficiency.
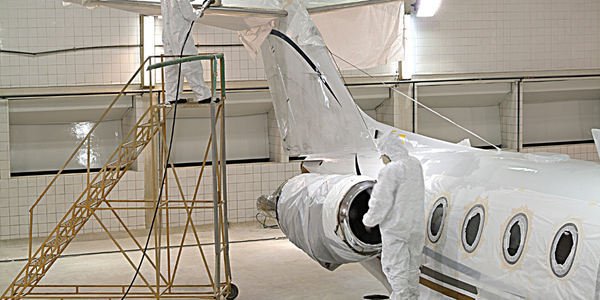
Case Study
Aircraft Predictive Maintenance and Workflow Optimization
First, aircraft manufacturer have trouble monitoring the health of aircraft systems with health prognostics and deliver predictive maintenance insights. Second, aircraft manufacturer wants a solution that can provide an in-context advisory and align job assignments to match technician experience and expertise.
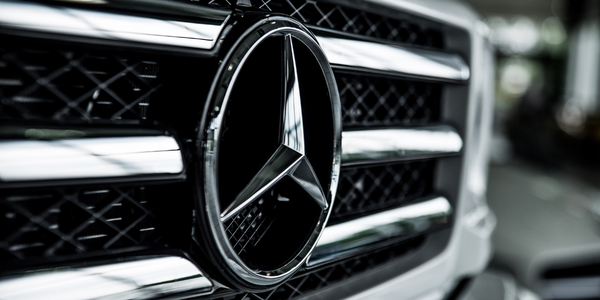
Case Study
Integral Plant Maintenance
Mercedes-Benz and his partner GAZ chose Siemens to be its maintenance partner at a new engine plant in Yaroslavl, Russia. The new plant offers a capacity to manufacture diesel engines for the Russian market, for locally produced Sprinter Classic. In addition to engines for the local market, the Yaroslavl plant will also produce spare parts. Mercedes-Benz Russia and his partner needed a service partner in order to ensure the operation of these lines in a maintenance partnership arrangement. The challenges included coordinating the entire maintenance management operation, in particular inspections, corrective and predictive maintenance activities, and the optimizing spare parts management. Siemens developed a customized maintenance solution that includes all electronic and mechanical maintenance activities (Integral Plant Maintenance).