技术
- 分析与建模 - 数字孪生/模拟
- 基础设施即服务 (IaaS) - 虚拟私有云
适用行业
- 包装
- 塑料
适用功能
- 采购
- 产品研发
用例
- 智能包装
- 制造过程模拟
服务
- 测试与认证
- 培训
关于客户
Amcor 硬质塑料是食品、饮料、医疗保健、个人和家庭护理包装领域的领先产品供应商。该公司总部位于密歇根州安娜堡,在 13 个县拥有超过 59 家制造工厂,拥有 6,000 多名员工。在硬质塑料行业工作,对可持续实践的需求很高。该公司不断寻找创新、轻质的容器设计,既美观又易于消费者操作,同时又不影响质量、性能或安全性。仿真在确保 Amcor 的轻量级软件包满足功能要求方面发挥着重要作用。
挑战
Amcor Rigid Plastics 是各个包装领域的领先产品供应商,在保持包装性能、环境影响和货架吸引力之间保持平衡,同时将成本保持在最低限度方面面临着挑战。该公司面临着创造更环保产品的压力。 Amcor 还寻求创新且轻便的容器设计,既美观又易于消费者操作,同时又不影响质量、性能或安全性。该公司使用 Altair 的 HyperWorks 套件为 CAD 团队的概念设计创建精确的有限元模型,以评估其在虚拟世界中的表现。然而,他们希望探索加速与新包装产品开发相关的工程和分析任务的方法。用于研究新包装设计在各种负载和冲击场景下的性能的虚拟测试过程消耗了模拟团队的大量时间。
解决方案
Altair ProductDesign 的企业解决方案小组 (ESG) 与 Amcor 的仿真专家合作,确定设计过程中可以在哪些方面节省时间和成本。他们建议 Amcor 可以利用 Impact Simulation Director (ISD),它可以自动执行与模型设置、分析、后处理和报告相关的繁重手动任务。 Altair ProductDesign 与 Amcor 团队密切合作,了解现有的影响模拟流程,以确定如何最好地实施 ISD,以避免中断正在进行的产品开发周期。组织了现场培训课程,以帮助快速有效地采用该解决方案。一旦实施,ISD 就能够通过允许用户定义每个零件的网格标准、自动对模型进行网格划分,然后快速检查网格质量和状态来加速建模过程。该解决方案指导分析师完成冲击模拟过程,从 CAD 几何创建求解器平台以进行各种分析。
运营影响
数量效益
Case Study missing?
Start adding your own!
Register with your work email and create a new case study profile for your business.
相关案例.
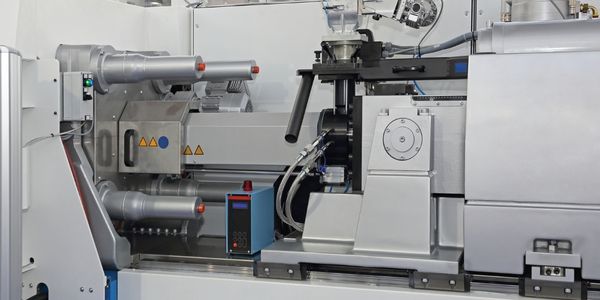
Case Study
Plastic Spoons Case study: Injection Moulding
In order to meet customer expectations by supplying a wide variety of packaging units, from 36 to 1000 spoons per package, a new production and packaging line needed to be built. DeSter wanted to achieve higher production capacity, lower cycle time and a high degree of operator friendliness with this new production line.

Case Study
IoT Data Analytics Case Study - Packaging Films Manufacturer
The company manufactures packaging films on made to order or configure to order basis. Every order has a different set of requirements from the product characteristics perspective and hence requires machine’s settings to be adjusted accordingly. If the film quality does not meet the required standards, the degraded quality impacts customer delivery causes customer dissatisfaction and results in lower margins. The biggest challenge was to identify the real root cause and devise a remedy for that.
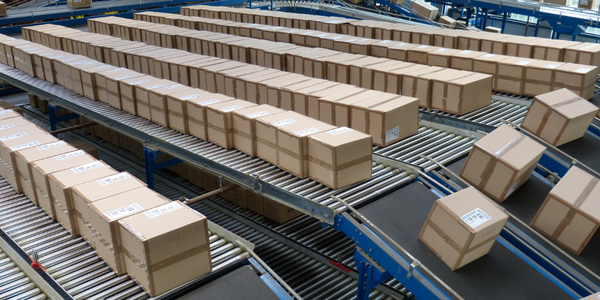
Case Study
Zenon the Ideal Basis for An Ergonomic HMI
KHS develops and produces machines and equipment for filling and packaging in the drinks industry. Because drinks manufacturing, filling and packaging consist of a number of highly complex processes, the user-friendly and intuitive operation of equipment is increasingly gaining in significance. In order to design these processes as simple as possible for the user, KHS decided to introduce a uniform, transparent and standardized solution to the company. The HMI interface should meet the requirement for people with different qualifications and enable them to work on a standard platform.
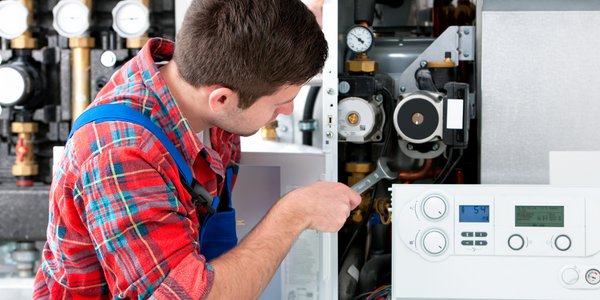
Case Study
Boiler Control System for Plastic Manufacturing Applications
Factory automation applications must be equipped to handle and monitor the myriads of information from attached devices. For plastic manufacturing applications, the boiler control system plays a critical role by gathering and regulating information to ensure production is accurate and smooth. In this particular case, the customer combines eight subsystems that include power meters, water meters, alarm output, displays, and I/O status to be controlled by several intelligent controllers with Modbus RTU interface. The Modbus TCP protocol is used for this application due to the distance. System Requirements: • Modbus serial to Modbus TCP translation • Multiple slaves/masters support • Automatic Modbus TCP response time detection
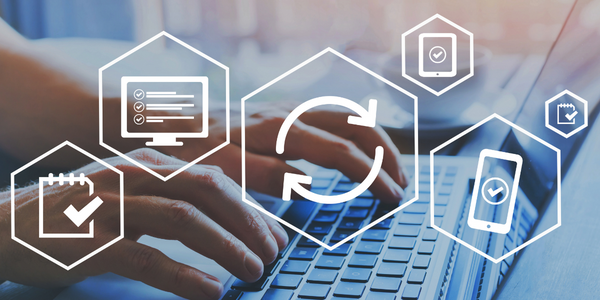
Case Study
Ascend Performance Materials Case Study
Ascend operations must access multiple software systems to manage day-to-day operations in an effective and secure manner. These systems generate large sets of data which contain critical information pertaining to management systems, planning and cost information in business systems and energy consumption. As a result, Ascend management was challenged with creating relevant reports reflecting performance measures in overall context of their operational process. The company’s previous process entailed collecting and analyzing data manually which was not effective, since the information collected was generated after the fact, and was too complex for collaborative use across the organization.
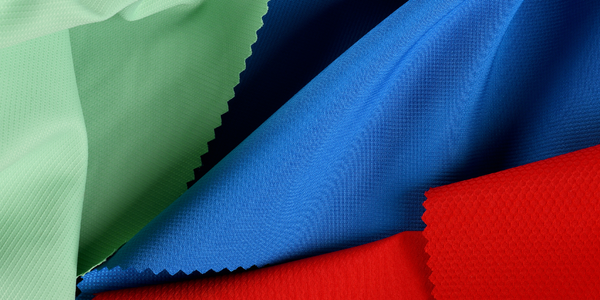
Case Study
Remake Enterprise-to-production System
The client was running a legacy material flow tracking system and wanted to replace the system with a more effective one as the system was increasingly expensive to maintain and support and also was not extendable. The client's IT landscape was filled with modern applications and it was difficult to interface the material flow tracking system with modern applications.