公司规模
Mid-size Company
地区
- Asia
国家
- Indonesia
产品
- ESRP-SCS-UNO1372 CODESYS
- EKI-5526I unmanaged switches
- ADAM-4571 data gateways
- ADAM-4571L data gateways
技术栈
- Intel Atom® multi-core processor
- Windows® 7 Professional for Embedded Systems
- CODESYS control runtime and visualization software
实施规模
- Enterprise-wide Deployment
影响指标
- Productivity Improvements
- Cost Savings
技术
- 平台即服务 (PaaS) - 连接平台
适用功能
- 离散制造
- 质量保证
用例
- 自动化制造系统
- 机器状态监测
服务
- 系统集成
关于客户
该客户是印度尼西亚一家领先的制造商,自 2009 年以来一直为世界各地的企业合作伙伴提供关键解决方案。该公司的客户遍布瑞典、美国、日本和马来西亚等多个国家。该制造商专注于机械设计、材料选择和工艺设计,为客户提供一流的解决方案,以最大限度地提高其自身产品和运营的效率和价值。该公司年轻而雄心勃勃,致力于进一步提高其声誉和竞争力。
挑战
这家印度尼西亚制造商是全球领先的关键解决方案提供商,为企业合作伙伴提供关键解决方案。该公司正在寻求提高生产线效率。该公司需要设备监控解决方案来提高生产线流程的产出。挑战在于找到一种紧凑且足够灵活的解决方案,可以安装在不同的工厂环境中并支持各种机械和设备。由于全球竞争的现实,该公司还面临预算限制,这限制了基础设施投资的资金。
解决方案
研华提供了一套完整的边缘解决方案套件 ESRP-SCS-UNO1372,其中包括高性能 Intel Atom® 多核处理器、无风扇 DIN 导轨紧凑型外形、适用于嵌入式系统的 Windows® 7 Professional 以及 CODESYS 控制运行时和可视化软件。该解决方案支持实时 PLC 或 PLC/Softmotion 控制,具有灵活的现场总线选项,例如 PROFINET、EtherCAT、EtherNet/IP 和 Modbus TCP/RTU,此外还能够在不同的 HMI 客户端上并行提供数据可视化。研华还提供了 EKI-5526I 非管理型交换机、ADAM-4571 和 ADAM-4571L 数据网关,从而提供易于开发、配置和部署的平台解决方案。该解决方案允许快速部署经济高效的监控系统,以用于各种工厂环境。
运营影响
Case Study missing?
Start adding your own!
Register with your work email and create a new case study profile for your business.
相关案例.
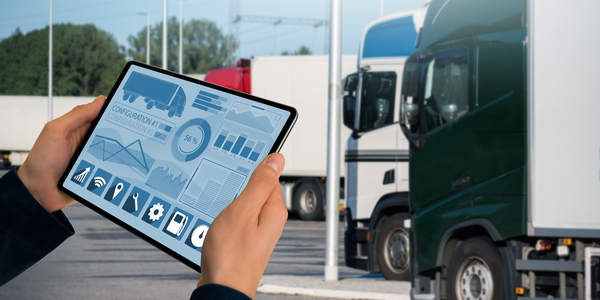
Case Study
IoT enabled Fleet Management with MindSphere
In view of growing competition, Gämmerler had a strong need to remain competitive via process optimization, reliability and gentle handling of printed products, even at highest press speeds. In addition, a digitalization initiative also included developing a key differentiation via data-driven services offers.
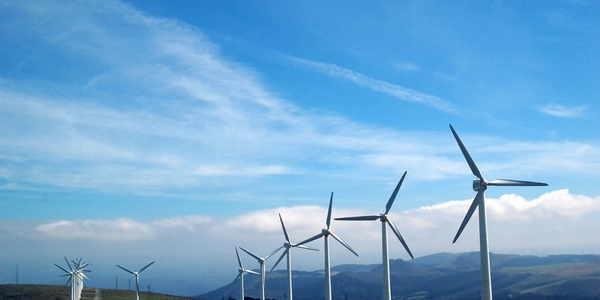
Case Study
Siemens Wind Power
Wind provides clean, renewable energy. The core concept is simple: wind turbines spin blades to generate power. However, today's systems are anything but simple. Modern wind turbines have blades that sweep a 120 meter circle, cost more than 1 million dollars and generate multiple megawatts of power. Each turbine may include up to 1,000 sensors and actuators – integrating strain gages, bearing monitors and power conditioning technology. The turbine can control blade speed and power generation by altering the blade pitch and power extraction. Controlling the turbine is a sophisticated job requiring many cooperating processors closing high-speed loops and implementing intelligent monitoring and optimization algorithms. But the real challenge is integrating these turbines so that they work together. A wind farm may include hundreds of turbines. They are often installed in difficult-to-access locations at sea. The farm must implement a fundamentally and truly distributed control system. Like all power systems, the goal of the farm is to match generation to load. A farm with hundreds of turbines must optimize that load by balancing the loading and generation across a wide geography. Wind, of course, is dynamic. Almost every picture of a wind farm shows a calm sea and a setting sun. But things get challenging when a storm goes through the wind farm. In a storm, the control system must decide how to take energy out of gusts to generate constant power. It must intelligently balance load across many turbines. And a critical consideration is the loading and potential damage to a half-billion-dollar installed asset. This is no environment for a slow or undependable control system. Reliability and performance are crucial.
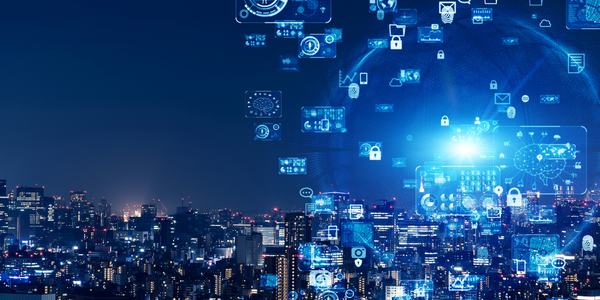
Case Study
Integration of PLC with IoT for Bosch Rexroth
The application arises from the need to monitor and anticipate the problems of one or more machines managed by a PLC. These problems, often resulting from the accumulation over time of small discrepancies, require, when they occur, ex post technical operations maintenance.
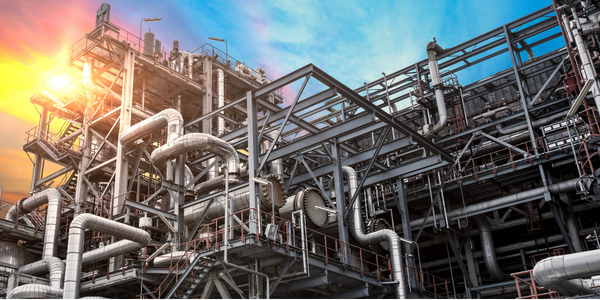
Case Study
Refinery Saves Over $700,000 with Smart Wireless
One of the largest petroleum refineries in the world is equipped to refine various types of crude oil and manufacture various grades of fuel from motor gasoline to Aviation Turbine Fuel. Due to wear and tear, eight hydrogen valves in each refinery were leaking, and each cost $1800 per ton of hydrogen vented. The plant also had leakage on nearly 30 flare control hydrocarbon valves. The refinery wanted a continuous, online monitoring system that could catch leaks early, minimize hydrogen and hydrocarbon production losses, and improve safety for maintenance.
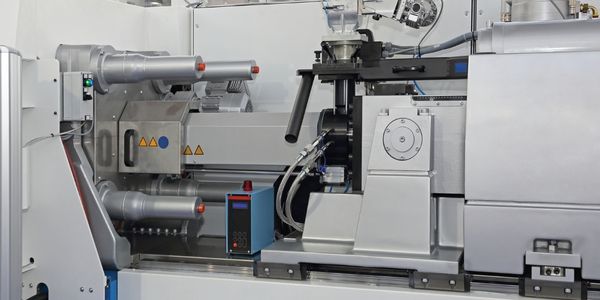
Case Study
Plastic Spoons Case study: Injection Moulding
In order to meet customer expectations by supplying a wide variety of packaging units, from 36 to 1000 spoons per package, a new production and packaging line needed to be built. DeSter wanted to achieve higher production capacity, lower cycle time and a high degree of operator friendliness with this new production line.
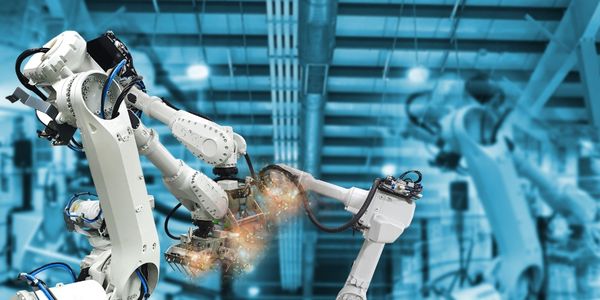
Case Study
Robot Saves Money and Time for US Custom Molding Company
Injection Technology (Itech) is a custom molder for a variety of clients that require precision plastic parts for such products as electric meter covers, dental appliance cases and spools. With 95 employees operating 23 molding machines in a 30,000 square foot plant, Itech wanted to reduce man hours and increase efficiency.