公司规模
Mid-size Company
地区
- America
- Europe
国家
- United States
- Germany
产品
- Turvo Enterprise platform
- Turvo Connect
- Turvo Pay
- Turvo Analytics
- Turvo Driver app
技术栈
- APIs
- Telematics
实施规模
- Enterprise-wide Deployment
影响指标
- Revenue Growth
- Productivity Improvements
- Customer Satisfaction
技术
- 平台即服务 (PaaS) - 连接平台
- 分析与建模 - 实时分析
适用功能
- 物流运输
用例
- 供应链可见性(SCV)
- 远程资产管理
服务
- 系统集成
关于客户
Port X Logistics is a well-known company that provides expedited containerized cargo management, drayage, trans-loading, and OTR trucking. The company serves a diverse group of supply chain professionals including Non-vessel operating common carriers (NVOCCs) that need complete visibility and around the-clock runtime, as well as real-time data access, Steamships that want proactive communication and efficient document management, with streamline document access, and Beneficial cargo owners (BCOs) with hosts of freight forwarders that all require uninterrupted compliance and visibility measures. The company was facing challenges in managing its diverse supply chain due to the use of multiple, disparate systems with a cumbersome manual management process.
挑战
Port X Logistics, a company known for its value in providing expedited containerized cargo management, drayage, trans-loading, and OTR trucking, was facing challenges in managing its diverse supply chain. The company was using multiple, disparate systems with a cumbersome manual management process. This disjointed process often left NVOCCs uncertain of whether a booking was shared and documented appropriately. BCOs had limited access to real-time information, and even upon request, the Port X team could take hours to review the information and provide it. Tracking down the right proof of delivery image, from thousands of files, was a hassle while trying to operate as a trucking company. The need for faster responsiveness fell under the microscope within the confines of the COVID-19 outbreak, forcing companies to mandate the use of contactless paperwork.
解决方案
Port X chose Turvo to bring harmony to its supply chain operation. The company uses the Turvo Enterprise platform, combining Turvo’s collaborative infrastructure, visibility, productivity tools, shipment management, Turvo Connect - with custom APIs, Turvo Pay, and Turvo Analytics. After a thorough review of available logistics solutions, Port X made the decision to unify its logistics management strategy with a Turvo partnership. That partnership creates a culture of excellence amid tech-driven insight and complete visibility into its operations. The process trickles into the downstream supply chain, gaining additional information as drivers use the Turvo Driver app and its embedded telematics functions to provide complete, end-to-end visibility and status. Now, drivers could immediately take and upload photos from within the Turvo Driver app.
运营影响
数量效益
Case Study missing?
Start adding your own!
Register with your work email and create a new case study profile for your business.
相关案例.
.png)
Case Study
Improving Vending Machine Profitability with the Internet of Things (IoT)
The vending industry is undergoing a sea change, taking advantage of new technologies to go beyond just delivering snacks to creating a new retail location. Intelligent vending machines can be found in many public locations as well as company facilities, selling different types of goods and services, including even computer accessories, gold bars, tickets, and office supplies. With increasing sophistication, they may also provide time- and location-based data pertaining to sales, inventory, and customer preferences. But at the end of the day, vending machine operators know greater profitability is driven by higher sales and lower operating costs.
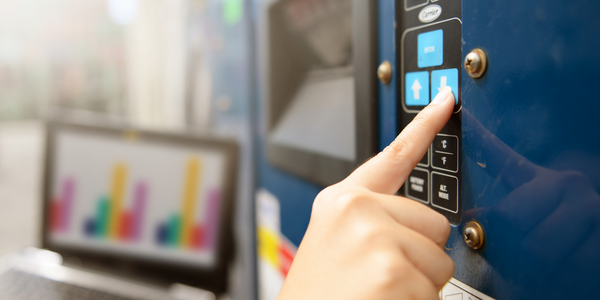
Case Study
Remote Temperature Monitoring of Perishable Goods Saves Money
RMONI was facing temperature monitoring challenges in a cold chain business. A cold chain must be established and maintained to ensure goods have been properly refrigerated during every step of the process, making temperature monitoring a critical business function. Manual registration practice can be very costly, labor intensive and prone to mistakes.
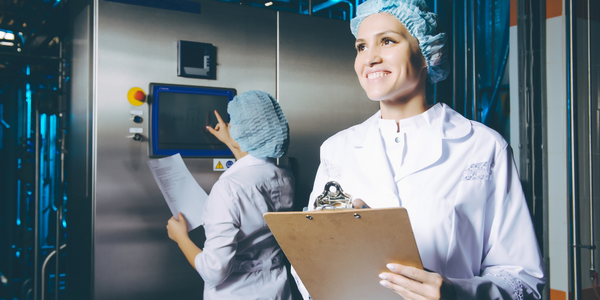
Case Study
Remote Wellhead Monitoring
Each wellhead was equipped with various sensors and meters that needed to be monitored and controlled from a central HMI, often miles away from the assets in the field. Redundant solar and wind generators were installed at each wellhead to support the electrical needs of the pumpstations, temperature meters, cameras, and cellular modules. In addition to asset management and remote control capabilities, data logging for remote surveillance and alarm notifications was a key demand from the customer. Terra Ferma’s solution needed to be power efficient, reliable, and capable of supporting high-bandwidth data-feeds. They needed a multi-link cellular connection to a central server that sustained reliable and redundant monitoring and control of flow meters, temperature sensors, power supply, and event-logging; including video and image files. This open-standard network needed to interface with the existing SCADA and proprietary network management software.
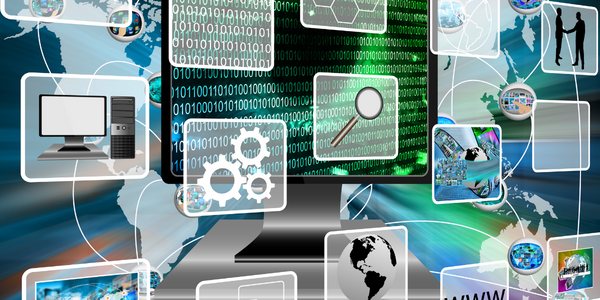
Case Study
Marine and Industrial Displays by Caterpillar
Caterpillar needed a flexible platform for a new generation of connected human-machine interfaces across a wide variety of industrial environments. Examples include marine, petroleum pumping, generators, custom hydraulics, mining, and rail applications.